Preparation of membrane for preventing injury from laser beam
A technology of laser damage and anti-reflection coating, applied in optics, optical components, instruments, etc., can solve the problem of low anti-laser damage threshold of anti-reflection coating, and achieve the effects of low cost, simple preparation and easy availability of raw materials
- Summary
- Abstract
- Description
- Claims
- Application Information
AI Technical Summary
Problems solved by technology
Method used
Examples
Embodiment 1
[0014] 20ml tetraethyl orthosilicate, 3.2ml water, 110ml absolute ethanol, 0.1ml NH 3 ·H 2 O and 0.1ml (200) PEG were mixed and stirred thoroughly, then put into a closed container, and aged at 20°C for 150 days to obtain a SiO2 sol coating solution, which was made into an anti-reflection film by spin coating method, and the optical properties were as follows: Table 1.
Embodiment 2
[0016] The added methyl orthosilicate is 20ml, water is 2.0ml, absolute ethanol is 50ml, NH 3 ·H 2 O is 0.05ml, PEG is 0.5ml (200), and the rest are the same as in Example 1. The optical properties are shown in Table 1.
Embodiment 3
[0018] The added tetraethyl orthosilicate is 20ml, water is 10ml, absolute ethanol is 200ml, NH 3 ·H 2 O is 0.1ml, PEG is 1.0ml (200), and the rest are the same as in Example 1. The optical properties are shown in Table 1.
PUM
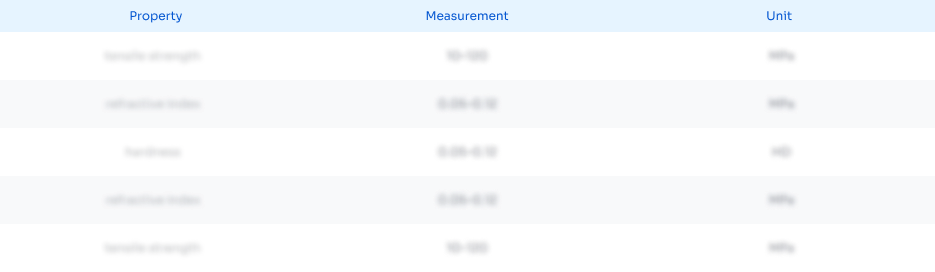
Abstract
Description
Claims
Application Information

- R&D
- Intellectual Property
- Life Sciences
- Materials
- Tech Scout
- Unparalleled Data Quality
- Higher Quality Content
- 60% Fewer Hallucinations
Browse by: Latest US Patents, China's latest patents, Technical Efficacy Thesaurus, Application Domain, Technology Topic, Popular Technical Reports.
© 2025 PatSnap. All rights reserved.Legal|Privacy policy|Modern Slavery Act Transparency Statement|Sitemap|About US| Contact US: help@patsnap.com