Composite Fe-based molecular sieve based catalyst and preparing method thereof
A technology of molecular sieve and catalyst, which is applied in the field of composite iron-based molecular sieve catalyst and its preparation, can solve the problems that it is not easy to realize large-scale industrial mass production, uneven distribution of active components, cumbersome multiple impregnation processes, etc., and achieve easy industrial mass production , Synthetic conditions are easy to control, and the preparation process is simple
- Summary
- Abstract
- Description
- Claims
- Application Information
AI Technical Summary
Problems solved by technology
Method used
Image
Examples
Embodiment 1
[0020] Weigh 2056g of Fe (NO 3 ) 3 ﹒ 9H 2 O and 708gMn(CH 3 COO) 2 ﹒ 4H 2 O in 3021g of deionized water, stirring and dissolving; adding 2335g of ammonia water with a mass concentration of 28%, mixing and stirring for 2h; adding 375g of ethanol and 3000g of ZSM-5 molecular sieve with a SAR ratio of 12.5, mixing and stirring for 3h; In the stainless steel tank, after vacuuming, apply a pressure of 0.15 MPa, put it into a closed stainless steel tank, after vacuuming, apply a pressure of 0.15 MPa, soak for 6 hours, put the mixture into a disk and dry it in an oven at 105 ° C, and dry it The dried massive solid is crushed in a pulverizer, placed in a muffle furnace for calcination at 450°C for 6 hours, and the calcined powder is further processed into a powder with a particle size of 100 mesh by a grinder to obtain a composite iron-based Molecular sieve catalyst.
[0021] NH on catalyst powder using a fixed-bed micro-reactor and a five-gas analyzer 3 - SCR conversion effi...
Embodiment 2
[0026] Weigh 2856g of Fe (NO 3 ) 3 ﹒ 9H 2 O and 294gCe(NO 3 ) 3 ﹒ 6H 2 O in 3162g deionized water, stirring and dissolving; adding 3162g of ammonia water with a mass concentration of 28%, mixing and stirring for 4h; adding 768g of n-butanol and 3000g of ZSM-5 molecular sieves with a SAR ratio of 60, mixing and stirring for 5h; Put it into a closed stainless steel tank, after vacuuming, apply a pressure of 0.30MPa, impregnate for 3h, put the mixture into a disk and dry in an oven at 150°C, crush the dried block solid in a pulverizer, place Calcined in a muffle furnace at 550° C. for 4 hours, and the calcined powder was further processed into a powder with a particle size of 180 mesh by a grinder to obtain a composite iron-based molecular sieve catalyst. Scanning electron microscope FE-SEM (SU8000) was used to observe the surface morphology of the sample, the results are shown in Figure 4 , the small particles of oxides on the outer surface of the molecular sieve crysta...
Embodiment 3
[0028] Weigh 2500g of Fe(NO 3 ) 3 ﹒ 9H 2 O and 320gCo(CH 3 COO) 2 ﹒ 4H 2 O was dissolved in 3500g deionized water by stirring; 2400g of ammonia water with a mass concentration of 28% was added, mixed and stirred for 3h; 500g of methanol and 3000g of molecular sieves of SAPO-34 with a Si / Al ratio of 0.95 were added, mixed and stirred for 3h; Put it into a closed stainless steel tank, after vacuuming, apply a pressure of 0.15MPa, impregnate for 3 hours, put the mixture into a disk and dry it in an oven at 125°C, crush the dried block solid in a pulverizer, place Calcined at 550° C. for 6 hours in a muffle furnace, and the calcined powder was further processed into a powder with a particle size of 180 mesh by a grinder to obtain a composite iron-based molecular sieve catalyst.
PUM
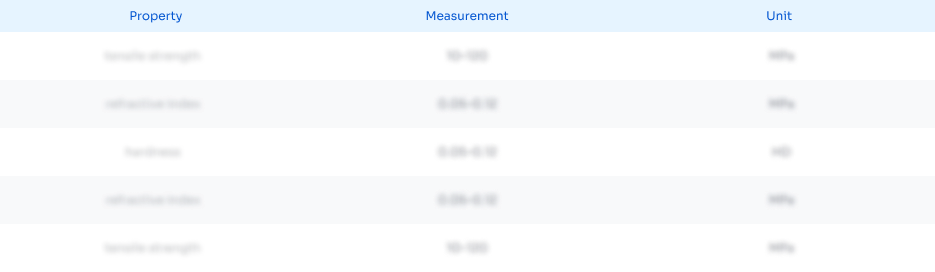
Abstract
Description
Claims
Application Information

- R&D
- Intellectual Property
- Life Sciences
- Materials
- Tech Scout
- Unparalleled Data Quality
- Higher Quality Content
- 60% Fewer Hallucinations
Browse by: Latest US Patents, China's latest patents, Technical Efficacy Thesaurus, Application Domain, Technology Topic, Popular Technical Reports.
© 2025 PatSnap. All rights reserved.Legal|Privacy policy|Modern Slavery Act Transparency Statement|Sitemap|About US| Contact US: help@patsnap.com