Iron and steel product surface treating agent and preparation method thereof
A technology of surface treatment agent and parts, which is applied in the direction of metal material coating process, etc., can solve the problems of phosphating solution destruction of active components, waste of acid solution, time-consuming, etc., to reduce the amount of waste water, shorten the process flow, and reduce production cost effect
- Summary
- Abstract
- Description
- Claims
- Application Information
AI Technical Summary
Problems solved by technology
Method used
Examples
Embodiment approach
[0017] As an embodiment of the present invention, a surface treatment agent for iron and steel parts, the weight ratio of its components is: 12-17% phosphoric acid with a concentration of 85%, 3-8% composite phosphate, and a concentration of 65%. 7-12% of nitric acid, 5-10% of corrosion inhibitor, 1-3% of water-based surfactant, 3-6% of zinc chrome yellow, 4-7% of polyol ester, and the balance is water;
[0018] The above-mentioned corrosion inhibitor is one of sodium citrate, sodium sulfite, zinc sulfate or a mixture of any two or more;
[0019] The above-mentioned polyol esters are one or a mixture of any two or more of pentaerythritol esters, glycolipids, and neopentyl polyol esters.
[0020] As a preferred embodiment, the weight percentage distribution ratio of the components of the surface treatment agent for iron and steel products is: 15% of phosphoric acid with a concentration of 85%, 5% of composite phosphate, 10% of nitric acid with a concentration of 65%, Corrosion...
Embodiment 1
[0028] Under normal pressure, according to: 12% of phosphoric acid with a concentration of 85%, 3% of compound phosphate, 7% of nitric acid with a concentration of 65%, 10% of sodium sulfite, 3% of water-based surfactant, 6% of zinc chrome yellow, pentaerythritol ester 7%, the balance is the weight ratio of water. Prepare each component, and put the above components in the corresponding container, then take a part of water from the container filled with water and add it to the reactor and put it in the reactor. Heat the water to 50°C, then add phosphoric acid, compound phosphate, sodium sulfite, pentaerythritol ester, water-based surfactant, zinc chrome yellow to the reactor according to the above weight ratio while stirring, and wait until the above components are completely dissolved Cool the obtained solution to normal temperature, then add nitric acid under ventilated conditions, and finally add the remaining water to obtain the surface treatment agent for steel parts of th...
Embodiment 2
[0034] Embodiment 2 is compared with embodiment 1, only the weight proportion of each component changes to some extent, and other content is exactly the same as embodiment 1, does not go into details here, the weight proportion of each component among the present embodiment 2 is : 85% phosphoric acid 17%, compound phosphate 8%, 65% nitric acid 12%, sodium sulfite 5%, water-based surfactant 1%, zinc chrome yellow 3%, pentaerythritol ester 4%, the balance is water.
[0035] Same as Example 1, after the preparation of the treatment agent is completed, it is placed in a transparent container for static storage. During the process of storing the surface treatment agent for steel parts obtained in Example 2, the liquid in the container remains clear and transparent. No precipitate was seen.
[0036] The above-mentioned surface treatment agent for steel parts after 3 months of static storage was also put into a large-scale seamless steel pipe production enterprise in China in early ...
PUM
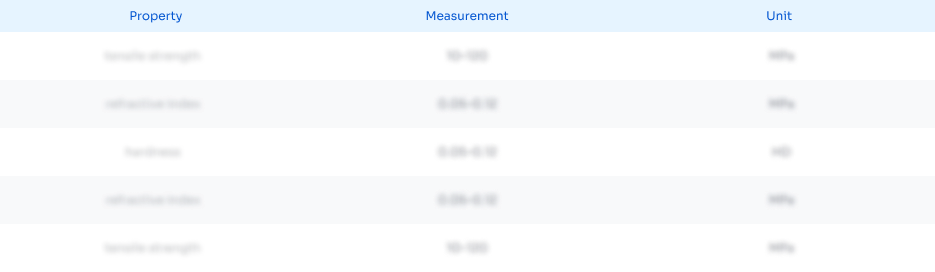
Abstract
Description
Claims
Application Information

- R&D
- Intellectual Property
- Life Sciences
- Materials
- Tech Scout
- Unparalleled Data Quality
- Higher Quality Content
- 60% Fewer Hallucinations
Browse by: Latest US Patents, China's latest patents, Technical Efficacy Thesaurus, Application Domain, Technology Topic, Popular Technical Reports.
© 2025 PatSnap. All rights reserved.Legal|Privacy policy|Modern Slavery Act Transparency Statement|Sitemap|About US| Contact US: help@patsnap.com