Regenerative burners for heating furnaces
A regenerative and heating furnace technology, applied in the field of regenerative burners and heating furnaces, can solve the problems that the size of the nozzle is difficult to meet the design requirements, high-temperature flue gas overflow and fire leakage, and cannot be repaired and replaced, etc., to achieve convenience Arrangement and maintenance, good flame organization, compact structure effect
- Summary
- Abstract
- Description
- Claims
- Application Information
AI Technical Summary
Problems solved by technology
Method used
Image
Examples
Embodiment 1
[0033] See Figure 2 to Figure 5 , The present invention discloses a regenerative burner for a heating furnace. The burner includes: a burner brick part 1, an air inlet unit 2, a heat storage box 3, a burner brick part 1 and a furnace wall Between the first flange 4, the second flange 5 arranged on both sides of the air inlet unit 2, and the third flange 6 arranged between the air inlet unit 2 and the air pipe; the air inlet unit 2 is arranged on the burner Between the mouth brick part 1, the heat storage tank 3.
[0034] The burner brick part 1 includes a burner brick 1.1 made of high temperature and erosion resistant mullite castable material and a metal shell part 1.2; the two parts are poured together during production, and the air and gas channels are combined in On an independent burner brick, the structure is the same as a conventional burner. The inner ring is a gas nozzle and the outer ring is an air nozzle, which effectively organizes the combustion.
[0035] The instal...
Embodiment 2
[0040] The difference between this embodiment and the first embodiment is that in this embodiment, the heat storage box is provided with a honeycomb body and a block brick. The honeycomb body is all made of mullite material, which has a large specific surface area, and has a heat storage and heat release rate. Fast, low resistance loss, high temperature efficiency, can preheat the gas to 1000 ℃, maximize the recovery of waste heat. The retaining brick adopts high-alumina brick, which has the characteristics of high temperature resistance, which can effectively resist high-temperature heat radiation from the furnace and protect the honeycomb body.
[0041] A three-way reversing valve is installed on the flue gas and gas pipes in front of the burner, which is used to switch the gas and flue gas during combustion and heat storage. The flue gas branch pipe in front of each burner is equipped with a thermal resistance. When measuring the temperature When the set value is exceeded, the...
PUM
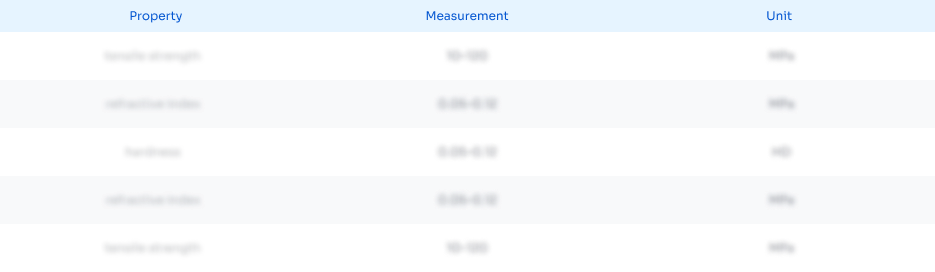
Abstract
Description
Claims
Application Information

- R&D
- Intellectual Property
- Life Sciences
- Materials
- Tech Scout
- Unparalleled Data Quality
- Higher Quality Content
- 60% Fewer Hallucinations
Browse by: Latest US Patents, China's latest patents, Technical Efficacy Thesaurus, Application Domain, Technology Topic, Popular Technical Reports.
© 2025 PatSnap. All rights reserved.Legal|Privacy policy|Modern Slavery Act Transparency Statement|Sitemap|About US| Contact US: help@patsnap.com