Tin stripping waste liquid treating method
A treatment method and waste liquid technology, applied in chemical instruments and methods, water/sewage multi-stage treatment, water/sludge/sewage treatment, etc., can solve problems such as large consumption of ammonia water and waste of resources
- Summary
- Abstract
- Description
- Claims
- Application Information
AI Technical Summary
Problems solved by technology
Method used
Image
Examples
Embodiment 1
[0022] Refer to attached figure 1 , a treatment method for tin stripping waste liquid, comprising the steps of:
[0023] S1. Pretreatment of tin stripping waste liquid
[0024] Add ammonium sulfate solid to the tin stripping waste liquid, adjust the pH value to 1.0-1.5,
[0025] S2. Recovery of metal tin
[0026] The polyacrylamide flocculant is added to the tin stripping waste liquid with a pH value of 1.0-1.5. The amount of the polyacrylamide flocculant added is 0.1% of the pretreated tin stripping waste liquid, so that the metal tin is in the form of tin hydroxide Precipitate, through solid-liquid separation, get wet tin hydroxide and copper-containing waste water, wet tin hydroxide is burned in a rotary kiln, the average temperature is about 800 ℃, get tin hydroxide powder, wet tin hydroxide is burned in a rotary kiln The exhaust gas obtained from burning is discharged after being treated by the four-stage spraying system to meet the standard;
[0027] S3. Recovery of ...
Embodiment 2
[0031] Refer to attached figure 1 , a treatment method for tin stripping waste liquid, comprising the steps of:
[0032] S1. Pretreatment of tin stripping waste liquid
[0033] Add solid sodium sulfate to the tin stripping waste liquid to adjust the pH value to 1.0-1.5,
[0034] S2. Recovery of metal tin
[0035] The polyacrylamide flocculant is added to the tin stripping waste liquid with a pH value of 1.0-1.5. The amount of the polyacrylamide flocculant added is 0.08% of the pretreated tin stripping waste liquid, so that the metal tin is in the form of tin hydroxide Precipitate, through solid-liquid separation, get wet tin hydroxide and copper-containing waste water, wet tin hydroxide is burned in a rotary kiln, the average temperature is about 800 ℃, get tin hydroxide powder, wet tin hydroxide is burned in a rotary kiln The exhaust gas obtained from burning is discharged after being treated by the four-stage spraying system to meet the standard;
[0036] S3. Recovery of...
Embodiment 3
[0040] Refer to attached figure 1 , a treatment method for tin stripping waste liquid, comprising the steps of:
[0041] S1. Pretreatment of tin stripping waste liquid
[0042] Add ammonium sulfate solid to the tin stripping waste liquid, adjust the pH value to 1.0-1.5,
[0043] S2. Recovery of metal tin
[0044] A polyacrylamide flocculant is added to the tin stripping waste liquid with a pH value of 1.0-1.5. The amount of the polyacrylamide flocculant added is 0.15% of the pretreated tin stripping waste liquid, so that the metal tin is in the form of tin hydroxide Precipitate, through solid-liquid separation, get wet tin hydroxide and copper-containing waste water, wet tin hydroxide is burned in a rotary kiln, the average temperature is about 800 ℃, get tin hydroxide powder, wet tin hydroxide is burned in a rotary kiln The exhaust gas obtained from burning is discharged after being treated by the four-stage spraying system to meet the standard;
[0045] S3. Recovery of m...
PUM
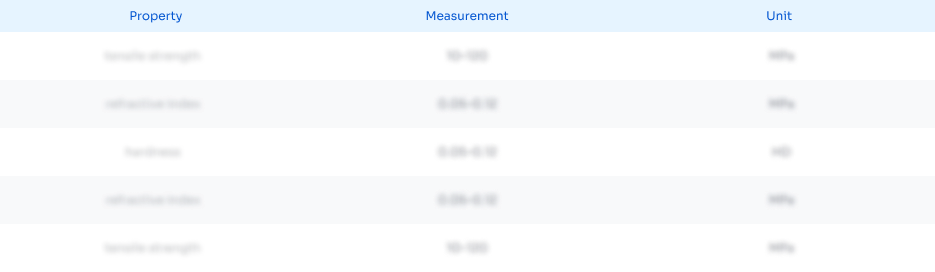
Abstract
Description
Claims
Application Information

- Generate Ideas
- Intellectual Property
- Life Sciences
- Materials
- Tech Scout
- Unparalleled Data Quality
- Higher Quality Content
- 60% Fewer Hallucinations
Browse by: Latest US Patents, China's latest patents, Technical Efficacy Thesaurus, Application Domain, Technology Topic, Popular Technical Reports.
© 2025 PatSnap. All rights reserved.Legal|Privacy policy|Modern Slavery Act Transparency Statement|Sitemap|About US| Contact US: help@patsnap.com