Aluminum alloy melting covering agent
A covering agent and aluminum alloy technology, which is applied in the field of aluminum smelting, can solve the problems of reducing aluminum conductivity, poor boron deoxidation effect, magnesium inclusions, etc., achieves strong chemical stability and thermal stability, ensures composition and performance, and promotes flotation flow effect
- Summary
- Abstract
- Description
- Claims
- Application Information
AI Technical Summary
Problems solved by technology
Method used
Image
Examples
Embodiment 1
[0016] The aluminum alloy smelting covering agent in this embodiment is composed of the following components in parts by mass: 8 parts of boron carbide, 5 parts of silica sand, 12 parts of nano ceramics, 12 parts of aluminum oxide, 15 parts of chaff ash, modified 10 parts of perlite and 8 parts of wollastonite.
[0017] The above-mentioned covering agent for aluminum alloy melting comprises the following preparation steps:
[0018] (1) soak the wollastonite and aluminum oxide of the above weight parts with 8% sulfuric acid for 8 hours, wash with deionized water, then soak with 12% sodium hydroxide solution for 5 hours, then wash with deionized water until neutral , and then calcined at 550°C for 2 hours, and broken into fragments with a particle size of 1-3mm;
[0019] (2) Add the boron carbide, silica sand, and nano-ceramics of the above-mentioned parts by mass into 1.2g / L potassium permanganate solution for soaking, remove impurities, then filter and wash to be neutral, cal...
Embodiment 2
[0024] The aluminum alloy smelting covering agent in this embodiment is composed of the following components in parts by mass: 16 parts of boron carbide, 10 parts of silica sand, 25 parts of nano ceramics, 20 parts of aluminum oxide, 26 parts of chaff ash, modified 30 parts of perlite and 20 parts of wollastonite.
[0025] The above-mentioned covering agent for aluminum alloy melting comprises the following preparation steps:
[0026] (1) soak the wollastonite and aluminum oxide of the above weight parts with 12% sulfuric acid for 5 hours, wash with deionized water, then soak with 10% sodium hydroxide solution for 8 hours, then wash with deionized water until neutral , and then calcined at 800°C for 2 hours, and broken into fragments with a particle size of 1-3mm;
[0027] (2) Add the boron carbide, silica sand, and nano-ceramics of the above-mentioned parts by mass into 1.2g / L potassium permanganate solution for soaking, remove impurities, then filter and wash to be neutral,...
Embodiment 3
[0032] The aluminum alloy smelting covering agent in this embodiment is composed of the following components in parts by mass: 12 parts of boron carbide, 8 parts of silica sand, 18 parts of nano ceramics, 16 parts of aluminum oxide, 20 parts of chaff ash, modified 20 parts of perlite and 14 parts of wollastonite.
[0033] The above-mentioned covering agent for aluminum alloy melting comprises the following preparation steps:
[0034] (1) soak the wollastonite and aluminum oxide of the above weight parts with 10% sulfuric acid for 6 hours, wash with deionized water, then soak with 11% sodium hydroxide solution for 7 hours, then wash with deionized water until neutral , and then calcined at 700°C for 2 hours, and broken into fragments with a particle size of 1-3mm;
[0035] (2) Add the boron carbide, silica sand, and nano-ceramics in the above mass fractions into 1.2g / L potassium permanganate solution for soaking to remove impurities, then filter and wash to neutral, and calcin...
PUM
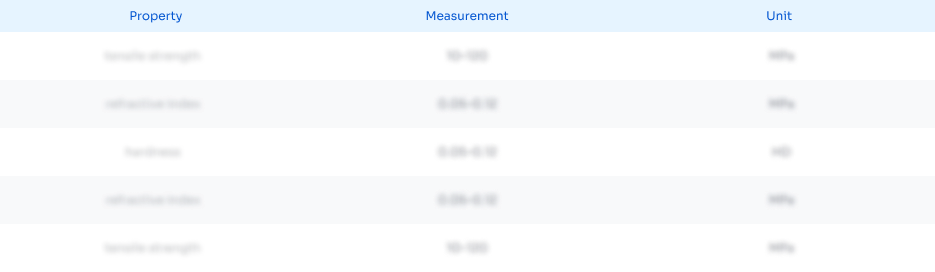
Abstract
Description
Claims
Application Information

- R&D Engineer
- R&D Manager
- IP Professional
- Industry Leading Data Capabilities
- Powerful AI technology
- Patent DNA Extraction
Browse by: Latest US Patents, China's latest patents, Technical Efficacy Thesaurus, Application Domain, Technology Topic, Popular Technical Reports.
© 2024 PatSnap. All rights reserved.Legal|Privacy policy|Modern Slavery Act Transparency Statement|Sitemap|About US| Contact US: help@patsnap.com