Moving bed methanol aromatization method for coproducing liquefied gas
A liquefied gas and aromatization technology, which is applied in chemical instruments and methods, preparation of liquid hydrocarbon mixtures, gas fuels, etc., can solve the problem that the thermal balance of the reaction regeneration system is difficult to maintain, the efficiency of the gas-solid separation system is affected, and the yield of the target product is reduced. and other problems, to avoid thermal decomposition, overcome the large degree of back mixing, and improve the production capacity
- Summary
- Abstract
- Description
- Claims
- Application Information
AI Technical Summary
Problems solved by technology
Method used
Image
Examples
Embodiment 1
[0044] Example one (see figure 1 ): Containing the first and second reactors, and the separation step adopts a depentane tower and a deliquefied gas tower for fractional distillation.
[0045] The fresh methanol feed is pumped outside the boundary area, and the pressure is increased to 1.76 MPaG and the temperature is 25°C. The fresh methanol feed 1 first enters the second reactor (equivalent to the end reactor) after heat exchange with the reaction product to increase the temperature, and then processes the pre-passivated catalyst from the first reactor (equivalent to the first end reactor). Contact reaction to moving bed, liquid hourly space velocity is 5.0h -1 , The intermediate product (ie the reaction product of the second reactor) is produced, the pressure is 1.74 or 1.75MPaG, the temperature is 350°C, or 320°C. After leaving the second reactor, the product enters the first reactor and reacts with the highly active catalyst from the regenerator in a radial moving bed contac...
Embodiment 2
[0051] Example two (see figure 2 ): Containing the first and second reactors, the separation step adopts the depentanizer and the deliquefied gas tower for fractional distillation, the circulating gas 3 is firstly subjected to ammonia cold heat exchange and pump boost before entering the deliquefied gas tower, and the methanol raw material is separated The 2 strands enter the two reactors respectively.
[0052] Fresh methanol feed 1 is pumped outside the boundary area, the pressure is increased to 0.3 MPaG, the temperature is 25 ℃, the fresh methanol feed 1 is heated by heat exchange with the reaction product, and then divided into 2 shares: raw material 1 and raw material 2, respectively as the first The reactor (equivalent to the first end reactor) and the second reactor (equivalent to the end reactor) are fed with a flow ratio of 1:9. Raw material 2 enters the second reactor, and carries out a radial moving bed contact reaction with the pre-passivated catalyst from the first ...
Embodiment 3
[0058] Example three (see image 3 ): Including the first, second, and third reactors, the separation step adopts the depentanizer and the deliquefied gas tower for fractional distillation, the recycle gas 3 is pressurized by the dry gas compressor before entering the deliquefied gas tower, and the methanol raw material Divided into 3 strands respectively into the three reactors.
[0059] The fresh methanol feed is pumped outside the boundary area, and the pressure is increased to 0.6 MPaG and the temperature is 25°C. The fresh methanol feed 1 is divided into 3 shares after heat exchange with the reaction product: Raw material 1, Raw material 2, Raw material 3, which are respectively used as the first reactor (equivalent to the initial reactor), the second reactor, and the third reaction The reactor (equivalent to the end reactor) feeds, and the flow ratio is 1:2:8. The raw material 3 enters the third reactor and undergoes a radial moving bed contact reaction with the pre-passiv...
PUM
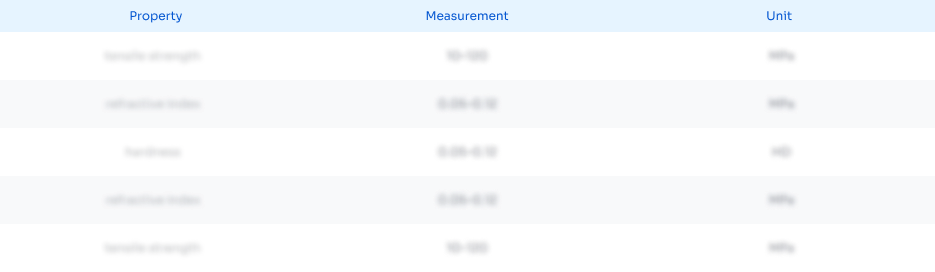
Abstract
Description
Claims
Application Information

- Generate Ideas
- Intellectual Property
- Life Sciences
- Materials
- Tech Scout
- Unparalleled Data Quality
- Higher Quality Content
- 60% Fewer Hallucinations
Browse by: Latest US Patents, China's latest patents, Technical Efficacy Thesaurus, Application Domain, Technology Topic, Popular Technical Reports.
© 2025 PatSnap. All rights reserved.Legal|Privacy policy|Modern Slavery Act Transparency Statement|Sitemap|About US| Contact US: help@patsnap.com