A method and device for dry grinding and separation of magnetite
A dry separation method and magnetite technology, applied in chemical instruments and methods, magnetic separation, solid separation, etc., can solve the problem of large particle size of the crusher output affecting the efficiency of magnetic separation, high power consumption and steel consumption of tube mills, and tailings Solve the problems of high cost, achieve the effect of ensuring the recovery rate of all iron, solving the large water consumption, and improving the quality of iron ore
- Summary
- Abstract
- Description
- Claims
- Application Information
AI Technical Summary
Problems solved by technology
Method used
Image
Examples
Embodiment Construction
[0024] The following non-limiting examples illustrate the invention.
[0025] refer to figure 1 As shown, the ore <80mm after crushing and magnetic separation is directly sent to the high-pressure roller buffer bin 1 through the belt, or, after being finely crushed to <30mm, it is sent to the high-pressure roller buffer bin 1, and the ore is first mixed with the coarse-grained return material in the buffer bin , after being squeezed by the high-pressure roller 2, it is sent to the linear vibrating screen 3 for screening by the belt. The sieved material (<3mm) of the linear vibrating screen 3 enters the dry magnetic separator 4 for separation, the waste rock is sent to the waste rock storage yard through the belt, and the coarse concentrate is sent to the wind power separator 5 for classification through the belt conveyor and the hoist. After grading, the coarse powder (<3mm) is sent back to the high-pressure roller buffer chamber 1 through the belt to continue extrusion, and ...
PUM
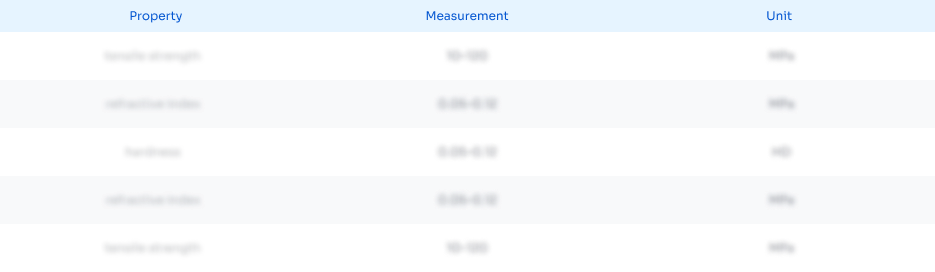
Abstract
Description
Claims
Application Information

- Generate Ideas
- Intellectual Property
- Life Sciences
- Materials
- Tech Scout
- Unparalleled Data Quality
- Higher Quality Content
- 60% Fewer Hallucinations
Browse by: Latest US Patents, China's latest patents, Technical Efficacy Thesaurus, Application Domain, Technology Topic, Popular Technical Reports.
© 2025 PatSnap. All rights reserved.Legal|Privacy policy|Modern Slavery Act Transparency Statement|Sitemap|About US| Contact US: help@patsnap.com