Ceramic heat exchange tube and preparation method thereof
A technology of heat exchange tubes and ceramics, which is applied in the field of ceramic heat exchange tubes and its preparation, can solve the problems of low wear resistance, low bending strength, unsatisfactory anti-seismic performance, and insufficient service life, etc., and achieve improved thermal shock resistance , promote the sintering densification process, and accelerate the effect of sintering speed
- Summary
- Abstract
- Description
- Claims
- Application Information
AI Technical Summary
Problems solved by technology
Method used
Examples
Embodiment 1
[0025] A ceramic heat exchange tube, comprising the following raw materials in mass fractions: 83 parts of alumina, 18 parts of cordierite, 7 parts of aluminum titanate, 0.3 parts of sodium hexametaphosphate, 3 parts of MgO, ZrO 2 2 parts, MnO 2 3 copies, B 2 o 3 2 parts, CuO2 parts, TiO 2 4 parts.
[0026] The preparation method of the above-mentioned ceramic heat exchange tube comprises the following steps:
[0027] 1) Raw material pretreatment: Mix the above-mentioned raw material powders in proportion to obtain a mixture, put the mixture into a ball mill tank, add water and ceramic balls, and perform wet ball milling, pour out the ball-milled materials, and dry them. Put it into an electric furnace, calcinate at 800°C for 3 hours, cool to room temperature, pass the powder through a 300-mesh sieve, and set aside, wherein the mass ratio of the mixture to water and ceramic balls is 1:1:1.5, and the ball milling time is 24 hours ;
[0028] 2) Preparation of ceramic slurr...
Embodiment 2
[0032] A ceramic heat exchange tube, comprising the following raw materials in mass fractions: 70 parts of alumina, 20 parts of cordierite, 5 parts of aluminum titanate, 0.4 parts of sodium hexametaphosphate, 2 parts of MgO, ZrO 23 parts, MnO 2 1 copy, B 2 o 3 3 parts, CuO 1 part, TiO 2 5 servings.
[0033] The preparation method of the above-mentioned ceramic heat exchange tube comprises the following steps:
[0034] 1) Raw material pretreatment: Mix the above-mentioned raw material powders in proportion to obtain a mixture, put the mixture into a ball mill tank, add water and ceramic balls, and perform wet ball milling, pour out the ball-milled materials, and dry them. Put it into an electric furnace, calcinate at 900°C for 2 hours, cool to room temperature, pass the powder through a 280-mesh sieve, and set aside, wherein the mass ratio of the mixture to water and ceramic balls is 1:2:2, and the ball milling time is 20 hours ;
[0035] 2) Preparation of ceramic slurry:...
Embodiment 3
[0039] A ceramic heat exchange tube, comprising the following raw materials in mass fractions: 90 parts of alumina, 15 parts of cordierite, 10 parts of aluminum titanate, 0.2 parts of sodium hexametaphosphate, 6 parts of MgO, ZrO 2 2 parts, MnO 2 3 copies, B 2 o 3 1 part, CuO3 part, TiO 2 3 copies.
[0040] The preparation method of the above-mentioned ceramic heat exchange tube comprises the following steps:
[0041] 1) Raw material pretreatment: Mix the above-mentioned raw material powders in proportion to obtain a mixture, put the mixture into a ball mill tank, add water and ceramic balls, and perform wet ball milling, pour out the ball-milled materials, and dry them. Put it into an electric furnace, calcinate at 900°C for 2 hours, cool to room temperature, pass the powder through a 260-mesh sieve, and set aside, wherein the mass ratio of the mixture to water and ceramic balls is 1:1.5:2, and the ball milling time is 22 hours ;
[0042] 2) Preparation of ceramic slurr...
PUM
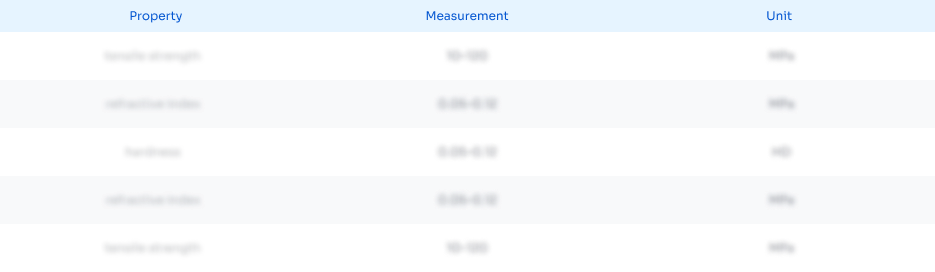
Abstract
Description
Claims
Application Information

- R&D
- Intellectual Property
- Life Sciences
- Materials
- Tech Scout
- Unparalleled Data Quality
- Higher Quality Content
- 60% Fewer Hallucinations
Browse by: Latest US Patents, China's latest patents, Technical Efficacy Thesaurus, Application Domain, Technology Topic, Popular Technical Reports.
© 2025 PatSnap. All rights reserved.Legal|Privacy policy|Modern Slavery Act Transparency Statement|Sitemap|About US| Contact US: help@patsnap.com