Smelting method of sulfur bearing steel
A smelting method and technology for sulfur-containing steel, applied in the field of iron and steel metallurgy, can solve the problems of clogging of the nozzle of the continuous casting machine, large fluctuation of sulfur content, instability, etc., to achieve stable product quality, avoid secondary pollution, and improve cleanliness. Effect
- Summary
- Abstract
- Description
- Claims
- Application Information
AI Technical Summary
Problems solved by technology
Method used
Examples
Embodiment 1
[0023] The present invention will be further explained below in combination with specific embodiments.
[0024] Adopt this method to smelt bonded hot-rolled round steel 42CrMoS4 (S content requirement is: 0.020-0.035%, Al content requirement is: 0.020-0.050%), comprises the following steps:
[0025] (1) add lime 43kg / t steel, slagging agent 2.53kg / t steel, steel core aluminum 23kg / t steel, steel tapping amount 120 tons, obtain primary molten steel;
[0026] (2) After the molten steel enters the LF furnace, turn on the argon gas to break the slag. The flow rate of the argon gas is set to 800-1000mL / min. kg / t steel and silicon carbide 13kg / t steel is deoxidized, the slag has turned white, add slagging agent 0.8kg / t steel, power off for 20 minutes, feed aluminum wire 2m / t steel, argon gas flow rate is set to 800- 1000mL / min, stir for 3min, adjust the argon gas to 30-40mL / min, feed the sulfur wire 2m / t steel, after feeding the sulfur wire, adjust the argon gas to 150mL / min, stir ...
PUM
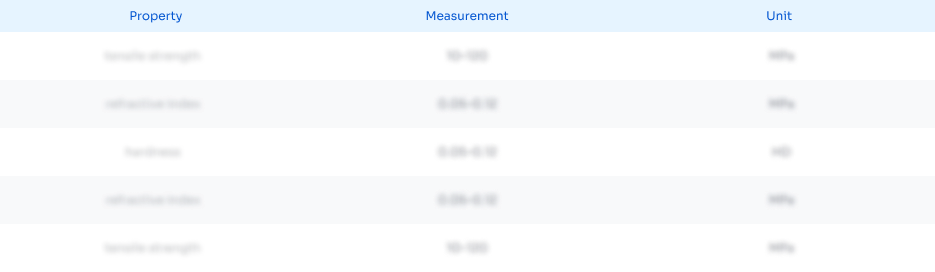
Abstract
Description
Claims
Application Information

- R&D
- Intellectual Property
- Life Sciences
- Materials
- Tech Scout
- Unparalleled Data Quality
- Higher Quality Content
- 60% Fewer Hallucinations
Browse by: Latest US Patents, China's latest patents, Technical Efficacy Thesaurus, Application Domain, Technology Topic, Popular Technical Reports.
© 2025 PatSnap. All rights reserved.Legal|Privacy policy|Modern Slavery Act Transparency Statement|Sitemap|About US| Contact US: help@patsnap.com