Zirconia fiber board and preparation method
A technology of zirconia fiber and zirconia, which is applied in the field of refractory materials, can solve the problems of low strength of zirconia fiberboard, short life of high-temperature pulverization, low thermal conductivity, etc., and achieve improved thermal efficiency and service life, low bulk density and zirconia content high effect
- Summary
- Abstract
- Description
- Claims
- Application Information
AI Technical Summary
Problems solved by technology
Method used
Image
Examples
Embodiment 1
[0035] Example 1: The raw material components and mass percentages of the zirconia fiberboard are: 70% of zirconia fibers with a diameter of 3-5 μm, 20% of zirconia hollow spheres with a particle size of 0.045mm<0.075mm, and 20% of zirconia hollow balls with a particle size of ≤0.003mm Zirconia composite micropowder 9%, the mass percent of monoclinic zirconia micropowder in zirconia composite micropowder is 55%; yttrium oxide and cerium oxide composite stabilizer 1%, the mass percent of yttrium oxide in composite stabilizer is 60%; 0.045mm <The amount of polyvinyl alcohol pellets with a particle size of ≤0.075mm is 15% of the total amount of raw materials added, the amount of polyacrylamide with a particle size of ≤0.045mm is 10% of the total amount of raw materials added, starch, calcium lignosulfonate and paste The addition of refined composite powder is 20% of the total addition of raw materials, the mass percentage of starch in the composite powder is 95%, and the addition ...
Embodiment 2
[0042] Example 2: The raw material components and mass percentages of the zirconia fiberboard are: 72% of zirconia fibers with a diameter of 3-5 μm, 18% of zirconia hollow spheres with a particle size of 0.045mm<0.075mm, and 18% of zirconia hollow spheres with a particle size of ≤0.003mm Zirconia composite micropowder 9%, the mass percent of monoclinic zirconia micropowder in zirconia composite micropowder is 85%; yttrium oxide and cerium oxide composite stabilizer 1%, the mass percent of yttrium oxide in composite stabilizer is 70%; 0.045mm <The amount of polyvinyl alcohol pellets with particle size ≤0.075mm is 7% of the total amount of raw materials added, the amount of graphite ≤0.045mm is 15% of the total amount of raw materials added, starch, calcium lignosulfonate and dextrin composite powder The add-on is 18% of the total add-on of raw materials, and the mass percentage of starch is 75% in the composite powder, and the add-on of water is 9% of the total add-on of raw mat...
Embodiment 3
[0043] Example 3: The raw material components and mass percentages of the zirconia fiberboard are: 78% of zirconia fibers with a diameter of 3-5 μm, 11% of zirconia hollow spheres with a particle size of 0.045mm<0.075mm, and 11% of zirconia hollow spheres with a particle size of ≤0.003mm Zirconia composite micropowder 9.8%, the mass percent of monoclinic zirconia micropowder in zirconia composite micropowder is 40%; Yttrium oxide and cerium oxide composite stabilizer 1.2%, the mass percent of yttrium oxide in composite stabilizer is 35%; and cerium oxide composite stabilizer 1.2%, the addition of 0.045mm<particle size≤0.075mm plastic pellets is 22% of the total addition of raw materials, the addition of graphite ≤0.045mm is 2% of the total addition of raw materials, starch, wood The addition of calcium sulfonate and dextrin is 19% of the composite powder of the total addition of raw materials, and the mass percent of starch in the composite powder is 50%, and the addition of wa...
PUM
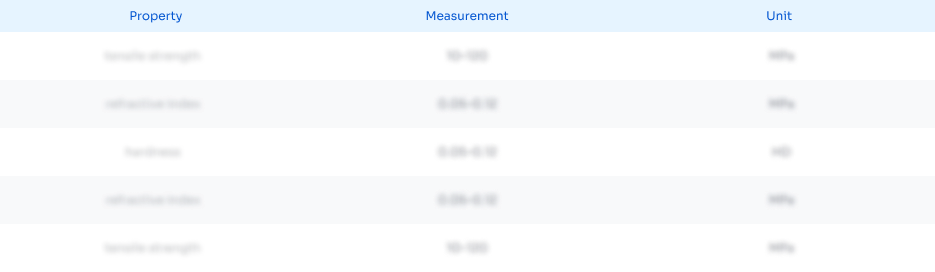
Abstract
Description
Claims
Application Information

- R&D
- Intellectual Property
- Life Sciences
- Materials
- Tech Scout
- Unparalleled Data Quality
- Higher Quality Content
- 60% Fewer Hallucinations
Browse by: Latest US Patents, China's latest patents, Technical Efficacy Thesaurus, Application Domain, Technology Topic, Popular Technical Reports.
© 2025 PatSnap. All rights reserved.Legal|Privacy policy|Modern Slavery Act Transparency Statement|Sitemap|About US| Contact US: help@patsnap.com