Method for performing insulating treatment on metal magnetic powder and preparing metal magnetic powder
A technology of insulation treatment and magnetic powder core, which is applied in the field of metal magnetic powder insulation treatment and preparation of metal magnetic powder core, can solve the problems of increased eddy current loss of magnetic core, increased core loss, and reduced magnetic powder insulation performance, etc., to reduce eddy current loss and improve Effects of core strength and increased frequency of use
- Summary
- Abstract
- Description
- Claims
- Application Information
AI Technical Summary
Problems solved by technology
Method used
Examples
Embodiment 1
[0026] Phosphoric acid, boric acid, water, and acetone are prepared into a mixed solution. First, boric acid and water form a boric acid aqueous solution, and the ratio is controlled at 1:1. Then, the ratio of boric acid aqueous solution, phosphoric acid, and acetone is 2:1:20 by mass to form a mixed solution. solution. Take the prepared passivation solution and add it to the iron powder. The weight ratio of the passivation solution to the iron powder is 1:8. Mix thoroughly to make it uniform. Phosphate and borate layers formed on the surface of the iron powder become the source of diffusion. Transfer the surface passivated iron powder to ZrO 2 In the box, under the protection of vacuum atmosphere, the temperature is rapidly raised to 600 degrees, the holding time is 1 hour, and the furnace is cooled. The B and P inorganic layers on the surface of the metal magnetic powder will diffuse into the metal magnetic powder, and a high-resistivity B and P element diffusion layer will...
Embodiment 2
[0028] Phosphoric acid, boric acid, water, and acetone are prepared into a mixed solution. First, boric acid and water form a boric acid aqueous solution, and the ratio is controlled at 1:1. Then, the ratio of boric acid aqueous solution, phosphoric acid, and acetone is 2:2:5 by mass to form a mixed solution. solution. Take the prepared passivation solution and add it to the iron-silicon powder. The weight ratio of the passivation solution to the iron-silicon powder is 1:12. Formation of phosphate and borate layers becomes a source of diffusion. Transfer the ferrosilicon powder after surface passivation to ZrO 2 In the box, under the protection of vacuum atmosphere, the temperature is rapidly raised to 800 degrees, the holding time is 24 hours, and the furnace is cooled. The B and P inorganic layers on the surface of the metal magnetic powder will diffuse into the metal magnetic powder, and the B and P element diffusion layers with high resistivity will be formed under the i...
Embodiment 3
[0030]Phosphoric acid, boric acid, water, and acetone are prepared into a mixed solution. First, boric acid and water form a boric acid aqueous solution, and the ratio is controlled at 1:1. Then, the ratio of boric acid aqueous solution, phosphoric acid, and acetone is 2:3:10 by mass to form a mixed solution. solution. Take the prepared passivation solution and add it to the iron-silicon-nickel powder. The weight ratio of the passivation solution to the iron-silicon-nickel powder is 1:9. Phosphate and borate layers formed on the surface of silicon nickel powder become the source of diffusion. Transfer the ferrosilicon nickel powder after surface passivation to ZrO 2 In the box, under the protection of vacuum atmosphere, the temperature is rapidly raised to 700 degrees, the holding time is 3 hours, and the furnace is cooled. The B and P inorganic layers on the surface of the metal magnetic powder will diffuse into the metal magnetic powder, and the B and P element diffusion l...
PUM
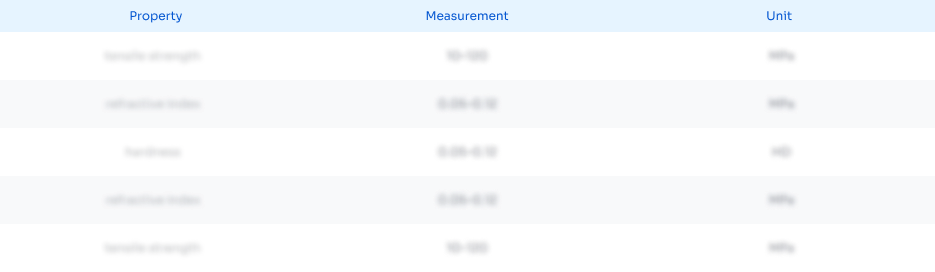
Abstract
Description
Claims
Application Information

- R&D
- Intellectual Property
- Life Sciences
- Materials
- Tech Scout
- Unparalleled Data Quality
- Higher Quality Content
- 60% Fewer Hallucinations
Browse by: Latest US Patents, China's latest patents, Technical Efficacy Thesaurus, Application Domain, Technology Topic, Popular Technical Reports.
© 2025 PatSnap. All rights reserved.Legal|Privacy policy|Modern Slavery Act Transparency Statement|Sitemap|About US| Contact US: help@patsnap.com