Method for recovering nickel, cobalt and iron from laterite-nickel ores
A laterite nickel ore and slurry technology, applied in the field of hydrometallurgical process of laterite nickel ore, can solve the problems of high acid consumption, low nickel and cobalt leaching rate, high sulfuric acid consumption, etc., and achieve low operating cost, simple operation and maintenance, The effect of low investment cost
- Summary
- Abstract
- Description
- Claims
- Application Information
AI Technical Summary
Problems solved by technology
Method used
Image
Examples
Embodiment 1
[0033] The present invention will be further described below, as appended figure 1 Shown:
[0034] 1. Take and grind to -80 mesh 500Kg2 # Add 500Kg water to saprolite ore to make saprolite slurry, prepare 500Kg98% concentrated sulfuric acid for use;
[0035] 2. Strictly control the flow rate with a mortar pump and a concentrated sulfuric acid pump. After rapid mixing, the saprolite slurry and concentrated sulfuric acid are flowed into the double-screw pusher reactor. The entire reaction takes 12 minutes. After the reaction, the material is a loose honeycomb solid paste. ,stand-by;
[0036] 3. After cooling down, simply crush the reaction material of the crisp honeycomb solid paste and pour it into the water immersion tank, add 1500Kg of water, carry out the water dissolving step, and stir for about 30 minutes;
[0037] 4. Pump the water-soluble slurry into the plate and frame filter press for solid-liquid separation and filter residue washing, and the pH value ratio is cont...
Embodiment 2
[0051] 1. Take and grind to -80 mesh 500Kg5 # Add 500Kg water to saprolite ore to make saprolite slurry, prepare 450Kg98% concentrated sulfuric acid for use;
[0052] 2. Strictly control the flow rate with a mortar pump and a concentrated sulfuric acid pump. After rapid mixing, the saprolite slurry and concentrated sulfuric acid are flowed into the double-screw pusher reactor. The entire reaction takes 10 minutes, and the material after the reaction is a crisp honeycomb solid paste. ,stand-by;
[0053] 3. After cooling down, simply crush the reaction material of the crisp honeycomb solid paste and pour it into the water immersion tank, add 1500Kg of water, carry out the water dissolving step, and stir for about 30 minutes;
[0054] 4. Pump the water-soluble slurry into the plate and frame filter press for solid-liquid separation and filter residue washing, and the pH value ratio is controlled at 0.5; obtain 230Kg of normal pressure acid leaching filter residue (A2), 1500L of ...
Embodiment 3
[0067] The normal-pressure acid leaching stage of the present embodiment is the same as that of Example 1, and in the pressure leaching stage, 1 # Sinka Limonite changed to 4 # Indonesian limonite.
[0068] Take 3000g4 # For limonite, add washing solution (E1) 6000ml to be mixed with limonite slurry and then move it into the autoclave, then add 3000ml of normal pressure acid leaching filtrate (B1) into the autoclave. After sealing the autoclave, control the temperature and heat. When the temperature rises to 215° C., continue heating at a constant temperature for 50 minutes, then stop heating and cool down. After cooling down to 80°C, the reaction slurry was removed from the autoclave for solid-liquid separation and the filter residue was washed to obtain 2800g of pressurized leaching residue (C3), 7550ml of pressurized leaching solution (D3) and 4500ml of washing solution (F3). See Table 3-1, Table 3-2 and Table 3-3 for the components of pressure leaching residue (C3), pre...
PUM
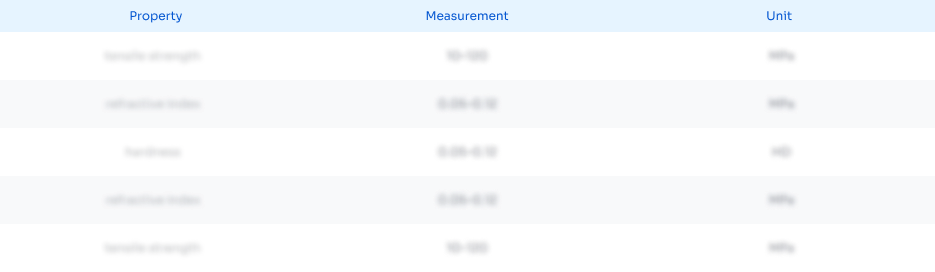
Abstract
Description
Claims
Application Information

- R&D Engineer
- R&D Manager
- IP Professional
- Industry Leading Data Capabilities
- Powerful AI technology
- Patent DNA Extraction
Browse by: Latest US Patents, China's latest patents, Technical Efficacy Thesaurus, Application Domain, Technology Topic, Popular Technical Reports.
© 2024 PatSnap. All rights reserved.Legal|Privacy policy|Modern Slavery Act Transparency Statement|Sitemap|About US| Contact US: help@patsnap.com