Method for catalyzing gasoline deep desulfurization with Ni-Mo-Co containing catalyst
A ni-mo-co, deep desulfurization technology, applied in chemical instruments and methods, physical/chemical process catalysts, metal/metal oxide/metal hydroxide catalysts, etc. Technical requirements, unseen problems, etc., to achieve the effect of reducing the severity of the reaction, optimizing the loss of octane number, and optimizing the hydrogen consumption
- Summary
- Abstract
- Description
- Claims
- Application Information
AI Technical Summary
Problems solved by technology
Method used
Image
Examples
Embodiment 1
[0032]Weigh 100g of pseudo-boehmite, add 2.5g of fenugreek powder, then add 3% nitric acid aqueous solution, knead and extrude, dry at 120°C for 4h, and then roast at 650°C for 4h to obtain the catalyst carrier. Test the water absorption rate of the carrier according to the conventional method, and then follow the equal volume impregnation method to configure the active component impregnation solution according to the water absorption rate of the carrier. First weigh 45ml of ammonia water, then add 2g of ammonium molybdate, 3g of cobalt nitrate, and 51g of nickel nitrate in turn and stir until dissolved, and finally use ammonia water to make up the volume. The carrier was impregnated by an equal volume impregnation method, so that the catalyst carrier fully absorbed the active component impregnating solution, and then placed for 12 hours, the catalyst was dried at 120°C for 4 hours, and calcined at 500°C for 4 hours to obtain the catalyst sample Cat-1#.
Embodiment 2
[0034] According to the preparation method of the carrier in Example 1, 100 g of the catalyst carrier was prepared, and then the active component impregnating solution was prepared, and the preparation method was the same as that of Example 1. First weigh 50ml of ammonia water, then sequentially add 4g of ammonium molybdate, 10g of cobalt nitrate, and 62g of nickel acetate and stir until dissolved, and finally use ammonia water to constant volume. The impregnation method, drying and roasting conditions of the metal active components were the same as in Example 1, and the catalyst sample Cat-2# was obtained.
Embodiment 3
[0036] According to the preparation method of the carrier in Example 1, 100 g of the catalyst carrier was prepared, and then the active component impregnation liquid was prepared, and the catalyst was impregnated in two steps. First weigh 40ml of ammonia water, then add 4g of ammonium molybdate, 6g of cobalt nitrate, and 34g of nickel acetate and stir until dissolved, and finally use ammonia water to make up the volume. Metal active component impregnation method and drying, roasting conditions are the same as embodiment 1, and make once impregnated catalyst sample; Above-mentioned catalyst sample is carried out secondary impregnation, takes by weighing 40ml ammoniacal liquor, then adds 4g ammonium molybdate, 6g cobalt nitrate, 21g acetic acid Nickel was stirred until dissolved, and finally made up to volume with ammonia water. The impregnation method, drying and roasting conditions of the metal active components were the same as in Example 1, and the catalyst sample Cat-3# was...
PUM
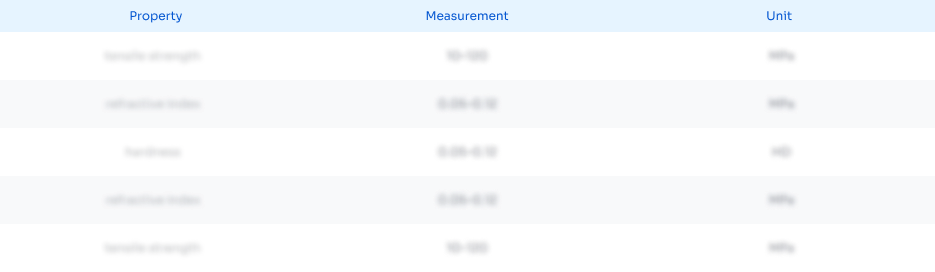
Abstract
Description
Claims
Application Information

- R&D Engineer
- R&D Manager
- IP Professional
- Industry Leading Data Capabilities
- Powerful AI technology
- Patent DNA Extraction
Browse by: Latest US Patents, China's latest patents, Technical Efficacy Thesaurus, Application Domain, Technology Topic, Popular Technical Reports.
© 2024 PatSnap. All rights reserved.Legal|Privacy policy|Modern Slavery Act Transparency Statement|Sitemap|About US| Contact US: help@patsnap.com