Local Flame Heating Ultrasonic Brazing Method of Aluminum Alloy Sealing Structure
A technology of sealing structure and brazing method, applied in metal processing, metal processing equipment, electric heating device, etc., can solve the problems of unfavorable engineering application, complicated process and high cost, and achieve high welding efficiency, simple process and good sealing performance. Effect
- Summary
- Abstract
- Description
- Claims
- Application Information
AI Technical Summary
Problems solved by technology
Method used
Image
Examples
Embodiment Construction
[0017] Such as figure 1 As shown, the embodiment of the present invention is carried out according to the following steps: a, before brazing, polish the surface of the aluminum alloy cover plate 3 and the surface of the box body 1 to be brazed with sandpaper, and wipe and clean it with acetone; b, the low-temperature Sn-based brazing The material 5 is placed on the side of the lapped end of the aluminum alloy sealing surface; c, the brazing material 5 is locally reciprocally heated with the gas flame 2 to melt and maintain the liquid state, but the base metal is not heated; d, applying ultrasonic vibration , wherein the ultrasonic vibration frequency is 18-25KHz, the amplitude is 4-20 μm, the ultrasonic introduction position is on the upper plate of the sealed structure, and the ultrasonic wave is applied to each position for 0.1-60s, and the ultrasonic head 4 is moved to make the solder on the joint surface of the entire structure realize joint filling; e , After the ultrason...
PUM
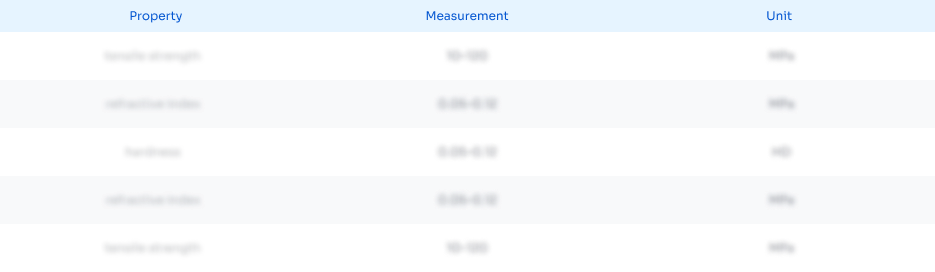
Abstract
Description
Claims
Application Information

- R&D
- Intellectual Property
- Life Sciences
- Materials
- Tech Scout
- Unparalleled Data Quality
- Higher Quality Content
- 60% Fewer Hallucinations
Browse by: Latest US Patents, China's latest patents, Technical Efficacy Thesaurus, Application Domain, Technology Topic, Popular Technical Reports.
© 2025 PatSnap. All rights reserved.Legal|Privacy policy|Modern Slavery Act Transparency Statement|Sitemap|About US| Contact US: help@patsnap.com