Preparation method of shape memory composite material
A composite material and memory technology, applied in the field of the preparation of shape memory composite materials, can solve the problems of low folding efficiency, low shape retention rate, large overall stiffness, etc. strain effect
- Summary
- Abstract
- Description
- Claims
- Application Information
AI Technical Summary
Problems solved by technology
Method used
Examples
specific Embodiment 1
[0015] Select T300 oriented discontinuous carbon fiber tow, the average length of the fiber is 50mm, use the medium temperature shape memory epoxy resin to form a semi-solid adhesive film with a glue machine, and then heat and press the resin film and oriented discontinuous tow through the prepreg equipment Composite to prepare a carbon fiber prepreg with a fiber volume fraction of 50%. Lay the prepreg on the mold according to a certain layering method, heat and pressurize it with an autoclave, and obtain a carbon fiber reinforced shape memory composite material.
specific Embodiment 2
[0016] Select T700 oriented discontinuous carbon fiber tow, the average length of the fiber is 75mm, and weave the carbon fiber tow into plain weave fabric with an area density of 120g / m 2 , the shape-memory Shuangma resin is made into a semi-solid film with a glue machine, and then the resin film and the plain fabric are combined by heating and pressing through a prepreg device to prepare a carbon fiber fabric prepreg with a fiber volume fraction of 35%. The prepreg is laid up on the mold according to a certain layering method, and is cured by heating and pressing with a hot press to obtain a carbon fiber reinforced shape memory composite material.
specific Embodiment 3
[0017] Select T800 oriented discontinuous carbon fiber tow, the average length of the fiber is 30mm, shape memory polyester and polyurethane blend polymer film, the fiber tow and the blend polymer film are compounded by hot pressing on a compound machine to obtain a prepreg. The press is pressurized and heated to form a carbon fiber-reinforced shape-memory polyurethane composite material with a fiber volume fraction of 35%.
PUM
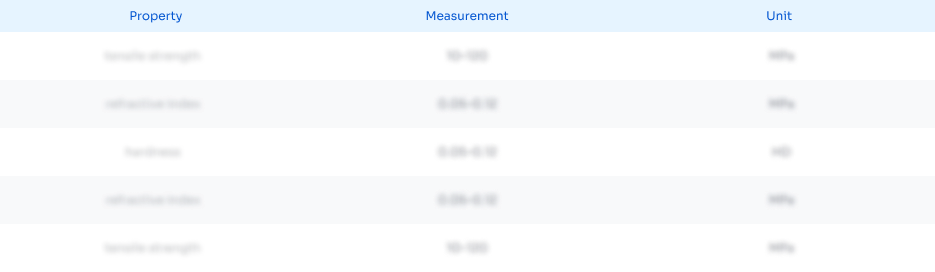
Abstract
Description
Claims
Application Information

- Generate Ideas
- Intellectual Property
- Life Sciences
- Materials
- Tech Scout
- Unparalleled Data Quality
- Higher Quality Content
- 60% Fewer Hallucinations
Browse by: Latest US Patents, China's latest patents, Technical Efficacy Thesaurus, Application Domain, Technology Topic, Popular Technical Reports.
© 2025 PatSnap. All rights reserved.Legal|Privacy policy|Modern Slavery Act Transparency Statement|Sitemap|About US| Contact US: help@patsnap.com