Method for preparing BTS film by virtue of radio frequency magnetron sputtering
A radio frequency magnetron sputtering and thin film technology, applied in the field of magnetron sputtering, can solve the difficulty of epitaxy or growth of preferentially oriented BST thin films, reduce the effective capacitance of ferroelectric thin film capacitors, and reduce the dielectric and ferroelectric properties of ferroelectric thin films and other problems, to achieve good structural properties and visible light transmittance, good application prospects, and the effect of reducing production costs
- Summary
- Abstract
- Description
- Claims
- Application Information
AI Technical Summary
Problems solved by technology
Method used
Examples
Embodiment 1
[0018] A method for preparing BTS thin films by radio frequency magnetron sputtering, comprising the steps of:
[0019] 1) Preparation of powder target: first Ba(Sn 0.15 Ti 0.85 )O 3 The powder is injected into the mold, paved, and after the mold is closed, the pressing time is 10 minutes under the pressure of 100Mpa, and then it can be pressed into shape;
[0020] 2) Place the target prepared in step 1) and the substrate with thermal conductivity in the vacuum sputtering chamber;
[0021] 3) Introduce oxygen and argon into the vacuum sputtering chamber, adjust the flow ratio of oxygen and argon to 12:2, set the target spacing to 8mm, set the coating power to 150, and the coating time to 4h. The injection pressure is 1.0Pa, and the heating temperature of the substrate is 200°C;
[0022] 4) After the sputtering is completed, the coated substrate is annealed to obtain the film, wherein the heating time of the annealing treatment is 2 hours, the annealing temperature is set t...
Embodiment 2
[0024] A method for preparing BTS thin films by radio frequency magnetron sputtering, comprising the steps of:
[0025] 1) Preparation of powder target: first Ba(Sn 0.15 Ti 0.85 )O 3 The powder is injected into the mold, paved, and after the mold is closed, the pressing time is 10 minutes under the pressure of 100Mpa, and then it can be pressed into shape;
[0026] 2) Place the target prepared in step 1) and the substrate with thermal conductivity in the vacuum sputtering chamber;
[0027] 3) Introduce oxygen and argon into the vacuum sputtering chamber, adjust the flow ratio of oxygen and argon to 14:2, set the target spacing to 8mm, set the coating power to 175w, and the coating time to 3h. The injection pressure is 1.3Pa, and the heating temperature of the substrate is 200°C;
[0028] 4) After the sputtering is completed, the coated substrate is annealed to obtain the thin film, wherein the heating time of the annealing treatment is 3 hours, the annealing temperature is...
Embodiment 3
[0030] A method for preparing BTS thin films by radio frequency magnetron sputtering, comprising the steps of:
[0031] 1) Preparation of powder target: first Ba(Sn 0.15 Ti 0.85 )O 3 The powder is injected into the mold, paved, and after the mold is closed, the pressing time is 10 minutes under the pressure of 100Mpa, and then it can be pressed into shape;
[0032] 2) Place the target prepared in step 1) and the substrate with thermal conductivity in the vacuum sputtering chamber;
[0033] 3) Introduce oxygen and argon into the vacuum sputtering chamber, adjust the flow ratio of oxygen and argon to 12:2, set the target spacing to 8mm, set the coating power to 160w, and the coating time to 4h. The injection pressure is 1.3Pa, and the heating temperature of the substrate is 300°C;
[0034] 4) After the sputtering is completed, the coated substrate is annealed to obtain the film, wherein the heating time of the annealing treatment is 2 hours, the annealing temperature is set ...
PUM
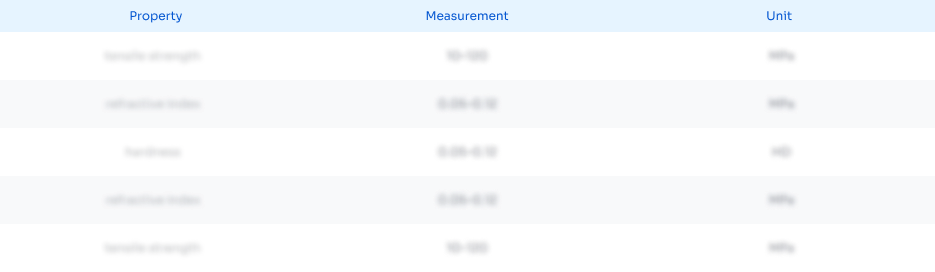
Abstract
Description
Claims
Application Information

- R&D Engineer
- R&D Manager
- IP Professional
- Industry Leading Data Capabilities
- Powerful AI technology
- Patent DNA Extraction
Browse by: Latest US Patents, China's latest patents, Technical Efficacy Thesaurus, Application Domain, Technology Topic, Popular Technical Reports.
© 2024 PatSnap. All rights reserved.Legal|Privacy policy|Modern Slavery Act Transparency Statement|Sitemap|About US| Contact US: help@patsnap.com