Converter final slag thickening method
A technology for thickening and final slag, applied in the field of metallurgy, can solve the problems of low slag blocking success rate, low final slag basicity, and high lime consumption, so as to improve the slag blocking success rate, increase the MgO content, and improve the metal yield. Effect
- Summary
- Abstract
- Description
- Claims
- Application Information
AI Technical Summary
Problems solved by technology
Method used
Image
Examples
Embodiment 1
[0025] Embodiment 1: A 50-ton oxygen converter with top-bottom combined blowing is used, and the amount of feed is the amount of each furnace.
[0026] 1) After the converter is tapped, the furnace is protected by slag splashing to make the slag sticky. Then add scrap steel and add molten iron. The converter adopts single-slag and all-slag-retaining operation mode, and the amount of slag remaining is about 4.5 tons, which is smelted according to the normal mode. The position of the gun before and during the middle stage of smelting is 1200mm. Open blowing oxygen pressure 0.9 ~ 1.0MPa, process oxygen pressure 0.7 ~ 0.75MPa. The slag material adopts a batch method. After 40 seconds of blowing, add 1900kg of lime, 400kg of sludge balls, 300kg of raw dolomite (250kg reserved), and 500kg of sintered ore (750kg reserved); after 5 minutes of blowing, the The remaining sintered ore is divided into 5 batches, and one batch is added every minute, and the amount of each batch is 150kg...
PUM
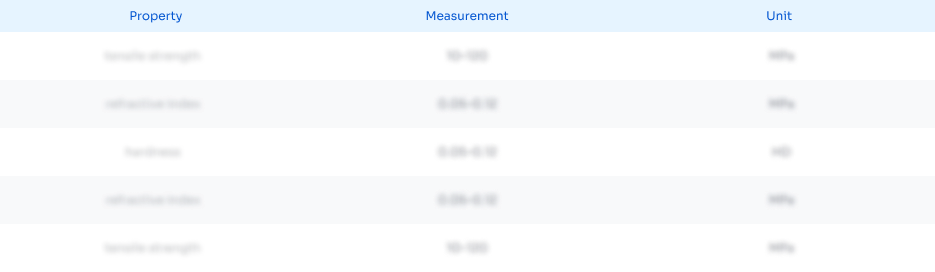
Abstract
Description
Claims
Application Information

- Generate Ideas
- Intellectual Property
- Life Sciences
- Materials
- Tech Scout
- Unparalleled Data Quality
- Higher Quality Content
- 60% Fewer Hallucinations
Browse by: Latest US Patents, China's latest patents, Technical Efficacy Thesaurus, Application Domain, Technology Topic, Popular Technical Reports.
© 2025 PatSnap. All rights reserved.Legal|Privacy policy|Modern Slavery Act Transparency Statement|Sitemap|About US| Contact US: help@patsnap.com