A kind of low-carbon low-silicon steel manufacturing method
A manufacturing method, low-carbon and low-silicon technology, applied in the manufacture of converters, etc., can solve the problems of high Al2O3 inclusions in deoxidation products, strong oxidation of molten steel, nodules in continuous casting nozzles, etc., to achieve convenient implementation, reduce steelmaking costs, The effect of improving cleanliness
- Summary
- Abstract
- Description
- Claims
- Application Information
AI Technical Summary
Problems solved by technology
Method used
Image
Examples
Embodiment 1
[0023] A method for manufacturing low-carbon and low-silicon steel. A 120t converter steelmaking plant manufactures SWRCH6A cold heading steel billets. The chemical composition control requirements of the steel are: C: 0.03%~0.06%, Si: ≤0.04%, Mn: 0.20~ 0.35%, P≤0.015%, S≤0.010%, Als: 0.025~0.045%, the balance is Fe and other unavoidable impurity elements; and smelted in a 120t converter → RH furnace vacuum treatment → LF furnace refining → billet continuous The production steps of casting are carried out.
[0024] The end point C of the converter is controlled within the range of 0.06%~0.10%, and the end point temperature is 1650~1670°C; 300kg of high-carbon ferromanganese is added during the tapping process of the converter for alloying; When the vacuum reaches 0.27Kpa for 7-8 minutes, the carbon content in the steel drops to 0.002%~0.02% and the free oxygen content drops to 120~200ppm by sampling analysis; after the vacuum reaches 0.27Kpa, add 60~80kg of aluminum to the ste...
Embodiment 2
[0026] A method for manufacturing low-carbon and low-silicon steel. A 120t converter steelmaking plant manufactures Q195LB low-carbon wire drawing steel billets. The chemical composition control requirements of the steel are: C: 0.03%~0.08%, Si: 0.02~0.06%, Mn: 0.10%~0.25%, P≤0.025%, S≤0.030%, the balance is Fe and other unavoidable impurity elements; it is produced by the production steps of converter → RH furnace vacuum treatment → billet continuous casting, and the end point of the converter is controlled : C: 0.06%~0.10%, molten pool temperature: 1680~1700℃; 100kg of high-carbon ferromanganese alloying is added during the tapping process of the converter; the free oxygen content of molten steel before RH furnace vacuum treatment is 250~500ppm, RH vacuum treatment for 7-8min vacuum When the vacuum degree reaches 0.27KPa, the range of carbon and oxygen content in the steel is 0.010%~0.030%, 150~250ppm respectively. After the vacuum degree reaches 0.27Kpa, add 30~40kg aluminum...
PUM
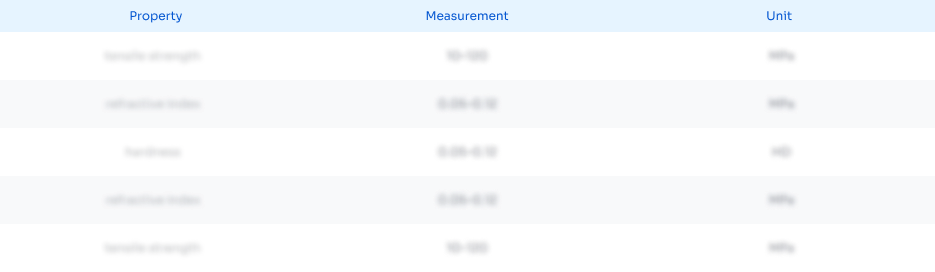
Abstract
Description
Claims
Application Information

- R&D
- Intellectual Property
- Life Sciences
- Materials
- Tech Scout
- Unparalleled Data Quality
- Higher Quality Content
- 60% Fewer Hallucinations
Browse by: Latest US Patents, China's latest patents, Technical Efficacy Thesaurus, Application Domain, Technology Topic, Popular Technical Reports.
© 2025 PatSnap. All rights reserved.Legal|Privacy policy|Modern Slavery Act Transparency Statement|Sitemap|About US| Contact US: help@patsnap.com