Waterborne polyurethane high-resilience plastic foam for automobile seats and preparation process thereof
A car seat and plastic foam technology, which is applied in the field of water-based polyurethane high-resilience plastic foam and its preparation, can solve problems such as weak resilience, damage to health, and insufficient resilience, so as to achieve good resilience performance, reduce costs, and The effect of improving quality
- Summary
- Abstract
- Description
- Claims
- Application Information
AI Technical Summary
Problems solved by technology
Method used
Examples
Embodiment 1
[0015] A water-based polyurethane high-resilience plastic foam for car seats, prepared from the following raw materials in parts by weight (kg): glycerol 70, ethylene oxide 25, propylene oxide 30, liquid paraffin 4, polypropylene oxide Ethylene oxide copolyether 3, diphenylmethane diisocyanate 160, potassium isooctanoate 6, quaternary ammonium formate 2, polydimethylsiloxane 5, sodium acetate 3, aluminum hydroxide 8, carbon black 6, antioxidant Agent TNP 4, ultraviolet absorber UVP-327 3, butyl stearate 2, silicone foam stabilizer 7, auxiliary agent 10; the auxiliary agent is made of the following raw materials in parts by weight (kg): aluminum tripolyphosphate 1. Potassium acetate 2, talcum powder 4, polybutadiene 2, zinc borate particles 12, triethylenediamine 3, ethyleneimine 1, stearic acid 7, sodium stearate 10, graphene 6, ethylene- Ethyl acrylate 7; the preparation method is: take the aluminum tripolyphosphate, potassium acetate, talcum powder, and zinc borate particles...
Embodiment 2
[0022] A water-based polyurethane high-resilience plastic foam for car seats, prepared from the following raw materials in parts by weight (kg): glycerol 75, ethylene oxide 27.5, propylene oxide 32.5, liquid paraffin 6, polypropylene oxide Ethylene oxide copolyether 4, diphenylmethane diisocyanate 165, potassium isooctanoate 7, quaternary ammonium formate 3, polydimethylsiloxane 6, sodium acetate 5, aluminum hydroxide 10, carbon black 8, antioxidant Agent TNP 5.5, ultraviolet absorber UVP-327 4, butyl stearate 2.5, organosilicon foam stabilizer 9, auxiliary agent 11; the auxiliary agent is made of the following raw materials in parts by weight (kg): aluminum tripolyphosphate 1.5, potassium acetate 2.5, talcum powder 4.5, polybutadiene 2.5, zinc borate particles 14, triethylenediamine 3.5, ethyleneimine 1.5, stearic acid 8, sodium stearate 11, graphene 7, ethylene- Ethyl acrylate 10; the preparation method is: weigh the aluminum tripolyphosphate, potassium acetate, talcum powde...
Embodiment 3
[0025] A water-based polyurethane high-resilience plastic foam for car seats, prepared from the following raw materials in parts by weight (kg): glycerol 80, ethylene oxide 30, propylene oxide 35, liquid paraffin 8, polypropylene oxide Ethylene oxide copolyether 5, diphenylmethane diisocyanate 170, potassium isooctanoate 8, quaternary ammonium formate 4, polydimethylsiloxane 7, sodium acetate 7, aluminum hydroxide 12, carbon black 10, antioxidant Agent TNP 7, ultraviolet absorber UVP-327 5, butyl stearate 3, silicone foam stabilizer 11, auxiliary agent 12; the auxiliary agent is made of the following raw materials in parts by weight (kg): aluminum tripolyphosphate 2. Potassium acetate 3, talcum powder 5, polybutadiene 3, zinc borate particles 16, triethylenediamine 4, ethyleneimine 2, stearic acid 9, sodium stearate 12, graphene 8, ethylene- Ethyl acrylate 13; the preparation method is: weigh the aluminum tripolyphosphate, potassium acetate, talcum powder, and zinc borate part...
PUM
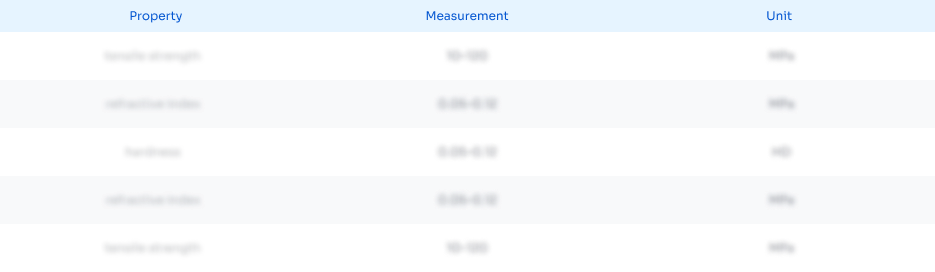
Abstract
Description
Claims
Application Information

- R&D Engineer
- R&D Manager
- IP Professional
- Industry Leading Data Capabilities
- Powerful AI technology
- Patent DNA Extraction
Browse by: Latest US Patents, China's latest patents, Technical Efficacy Thesaurus, Application Domain, Technology Topic, Popular Technical Reports.
© 2024 PatSnap. All rights reserved.Legal|Privacy policy|Modern Slavery Act Transparency Statement|Sitemap|About US| Contact US: help@patsnap.com