Anti-corrosion copper-based brake material with high friction coefficient and preparation method of anti-corrosion copper-based brake material
A high friction coefficient and brake material technology, applied in the field of high friction coefficient corrosion-resistant copper-based brake materials and its preparation, can solve the problems of low static friction coefficient and resistance to seawater corrosion, so as to improve the friction coefficient and overcome poor corrosion resistance , The effect of reducing the amount of wear
- Summary
- Abstract
- Description
- Claims
- Application Information
AI Technical Summary
Problems solved by technology
Method used
Examples
Embodiment 1
[0025] A high friction coefficient corrosion-resistant copper-based brake material, its formula contains 34% copper, 12% carbon, 6% titanium, 6% nickel, 10% quartz sand, 9% silicon carbide by weight , 6% mullite, 8% molybdenum disulfide and 9% molybdenum trioxide. Its preparation method is as follows: (1) dry the powder of compound components such as quartz sand, silicon carbide, mullite, molybdenum disulfide, and molybdenum trioxide for use; Proportionally add graphite powder, titanium powder, nickel powder, quartz sand powder, silicon carbide powder, mullite powder, molybdenum disulfide powder, molybdenum trioxide powder, etc., and mix them evenly; (3) weigh 50 grams of mixed Put the powder into the mold, and press it into the original sheet-shaped green body by cold pressing, and the molding pressure is 350MPa; (4) Put the cold-pressed green sheet into the sintering furnace and heat it under the protective atmosphere of argon. Bottom sintering, the sintering temperature is...
Embodiment 2
[0028] A high friction coefficient corrosion-resistant copper-based brake material, its formula contains 79% copper, 6% carbon, 2% titanium, 2% nickel, 4% quartz sand, 3% silicon carbide by weight , 2% mullite and 2% molybdenum trioxide. Its preparation method is as follows: (1) dry the powders of compound components such as quartz sand, silicon carbide, mullite, molybdenum trioxide, etc.; , titanium powder, nickel powder, quartz sand powder, silicon carbide powder, mullite powder, molybdenum trioxide powder, etc., and mix it uniformly; (3) take 50 grams of uniformly mixed powder and put it into the mold, and The original sheet-shaped green body is pressed by cold pressing, and the forming pressure is 450MPa; (4) The cold-pressed green disc is put into a sintering furnace and sintered under an argon protective atmosphere, and the sintering temperature is 800°C. The sintering time is 100 minutes; during the sintering process, when the temperature of the green body rises to 40-...
Embodiment 3
[0031] A high friction coefficient corrosion-resistant copper-based brake material, its formula contains 60% copper, 8% carbon, 4% titanium, 3% nickel, 2% tin, 6% quartz sand, 5% silicon carbide, 4% mullite, 3% molybdenum disulfide and 5% molybdenum trioxide. Its preparation method is as follows: (1) dry the powder of compound components such as quartz sand, silicon carbide, mullite, molybdenum disulfide, and molybdenum trioxide for use; Add graphite powder, titanium powder, nickel powder, tin powder, quartz sand powder, silicon carbide powder, mullite powder, molybdenum disulfide powder, molybdenum trioxide powder, etc., and mix them evenly; (3) weigh 50 grams Put the uniformly mixed powder into the mold, and press it into the original sheet-shaped green body by cold pressing, and the molding pressure is 380MPa; (4) put the cold-pressed green sheet into the sintering furnace and Sintering under air protection atmosphere, the sintering temperature is 830℃, and the sintering t...
PUM
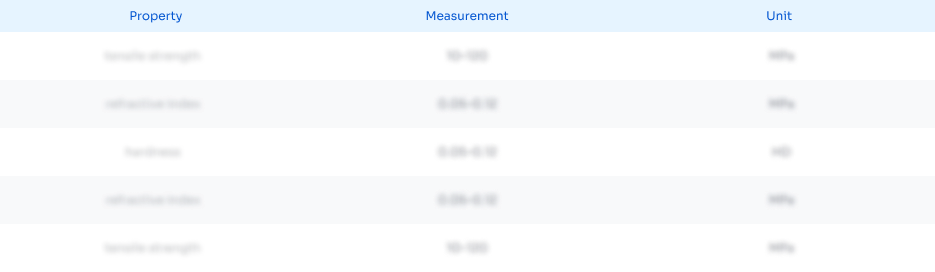
Abstract
Description
Claims
Application Information

- R&D Engineer
- R&D Manager
- IP Professional
- Industry Leading Data Capabilities
- Powerful AI technology
- Patent DNA Extraction
Browse by: Latest US Patents, China's latest patents, Technical Efficacy Thesaurus, Application Domain, Technology Topic, Popular Technical Reports.
© 2024 PatSnap. All rights reserved.Legal|Privacy policy|Modern Slavery Act Transparency Statement|Sitemap|About US| Contact US: help@patsnap.com