Flame-retardant reinforced PBT (polybutylene terephthalate) plastic meeting requirement for incombustibility of glow wire at temperature of 850 DEG C and preparation method thereof
A glow wire and plastic technology, applied in the field of flame retardant reinforced PBT plastic and its preparation, can solve the problems of loss of material mechanical properties, poor mechanical properties of PBT materials, and large amount of flame retardant added, so as to improve the glow wire temperature, overcome the The effect of easy separation and large contact area
- Summary
- Abstract
- Description
- Claims
- Application Information
AI Technical Summary
Problems solved by technology
Method used
Image
Examples
Embodiment 1
[0037] A 850-degree glow-wire non-combustible flame-retardant reinforced PBT plastic, which includes the following components by weight percentage:
[0038]
[0039]
[0040] The preparation method of the above-mentioned 850-degree glow-wire incombustible flame-retardant reinforced PBT plastic is:
[0041] (1) Take powdery PBT material, add flame retardant MCA, decabromodiphenylethane, brominated epoxy resin, sodium antimonate, TPP, EMA-g-GMA, zinc borate and mix evenly, and the mixing time is 5 minutes;
[0042] (2) Add granular PBT and antioxidant, lubricant, glass fiber and mix;
[0043] (3) Melt extrusion granulation.
[0044] The PBT plastic prepared above was taken for mechanical performance test, the mechanical performance test environment: 23 degrees, dry state, the results are shown in Table 1.
[0045] Table 1 PBT plastic mechanical properties test results
[0046]
Embodiment 2
[0048] A 850-degree glow-wire non-combustible flame-retardant reinforced PBT plastic, which includes the following components by weight percentage:
[0049]
[0050]
[0051] The preparation method of the above-mentioned 850-degree glow-wire incombustible flame-retardant reinforced PBT plastic is:
[0052] (1) Take powdery PBT material, add flame retardant MCA, decabromodiphenylethane, brominated epoxy resin, sodium antimonate, TPP, EMA-g-GMA, zinc borate and mix evenly, and the mixing time is 10 minutes;
[0053] (2) Add granular PBT and antioxidant, lubricant, glass fiber and mix;
[0054] (3) Melt extrusion granulation.
[0055] The PBT plastic prepared above was taken for mechanical performance test, the mechanical performance test environment: 23 degrees, dry state, the results are shown in Table 2.
[0056] Table 2 PBT plastic mechanical properties test results
[0057]
Embodiment 3
[0059] A 850-degree glow-wire non-combustible flame-retardant reinforced PBT plastic, which includes the following components by weight percentage:
[0060]
[0061] The preparation method of the above-mentioned 850-degree glow-wire incombustible flame-retardant reinforced PBT plastic is:
[0062] (1) Take powdery PBT material, add flame retardant MCA, decabromodiphenylethane, brominated epoxy resin, sodium antimonate, TPP, EMA-g-GMA, zinc borate and mix evenly, and the mixing time is 10 minutes;
[0063] (2) Add granular PBT and antioxidant, lubricant, glass fiber and mix;
[0064] (3) Melt extrusion granulation.
[0065] The PBT plastic prepared above was taken for mechanical performance test, the mechanical performance test environment: 23 degrees, dry state, the results are shown in Table 3.
[0066] Table 3 PBT plastic mechanical properties test results
[0067]
[0068]
PUM
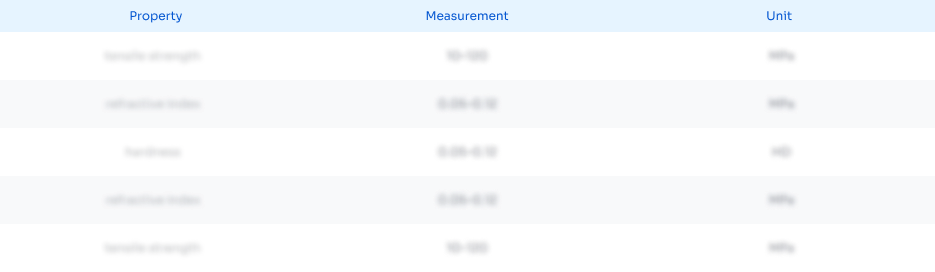
Abstract
Description
Claims
Application Information

- R&D Engineer
- R&D Manager
- IP Professional
- Industry Leading Data Capabilities
- Powerful AI technology
- Patent DNA Extraction
Browse by: Latest US Patents, China's latest patents, Technical Efficacy Thesaurus, Application Domain, Technology Topic, Popular Technical Reports.
© 2024 PatSnap. All rights reserved.Legal|Privacy policy|Modern Slavery Act Transparency Statement|Sitemap|About US| Contact US: help@patsnap.com