Environment-friendly weather-resistant flame-retardant PP material and preparation method thereof
An environmentally friendly and flame retardant technology, applied in the field of polypropylene materials, which can solve the problems of easy oxidation of hydrogen and poor weather resistance of PP
- Summary
- Abstract
- Description
- Claims
- Application Information
AI Technical Summary
Problems solved by technology
Method used
Image
Examples
Embodiment 1
[0022] Add 25 parts of homopolymerized PP, 40 parts of copolymerized PP, 27 parts of compound intumescent halogen-free flame retardant, 7 parts of talc, 0.3 parts of ultraviolet absorber, 0.4 parts of antioxidant, and 0.3 parts of ethylene bis stearamide Mix it evenly in a high-speed mixing barrel; then, knead in a twin-screw extruder, and the temperature of each section of the twin-screw is: T 1 =160°C, T 2 =170°C, T 3 =175°C, T 4 =180°C, T 5 =185°C, T 6 =190°C, twin-screw extruder speed r=350r.min -1 , and finally, extrude, cool, and pelletize to obtain an environmentally friendly weather-resistant and flame-retardant PP material.
Embodiment 2
[0024] Add 20 parts of homopolymerized PP, 45 parts of copolymerized PP, 25 parts of compound intumescent halogen-free flame retardant, 9 parts of talcum powder, 0.3 parts of ultraviolet absorber, 0.4 parts of antioxidant, and 0.3 parts of ethylene bis stearamide Mix it evenly in a high-speed mixing barrel; then, knead in a twin-screw extruder, and the temperature of each section of the twin-screw is: T 1 =160°C, T 2 =170°C, T 3 =175°C, T 4 =180°C, T 5 =185°C, T 6 =190°C, twin-screw extruder speed r=350r.min -1 , and finally, extrude, cool, and pelletize to obtain an environmentally friendly weather-resistant and flame-retardant PP material.
Embodiment 3
[0026] Add 29 parts of homopolymerized PP, 35 parts of copolymerized PP, 30 parts of compound intumescent halogen-free flame retardant, 5 parts of talcum powder, 0.3 parts of ultraviolet absorber, 0.4 parts of antioxidant, and 0.3 parts of ethylene bis stearamide Mix it evenly in a high-speed mixing barrel; then, knead in a twin-screw extruder, and the temperature of each section of the twin-screw is: T 1 =160°C, T 2 =170°C, T 3 =175°C, T 4 =180°C, T 5 =185°C, T 6 =190°C, twin-screw extruder speed r=350r.min -1 , and finally, extrude, cool, and pelletize to obtain an environmentally friendly weather-resistant and flame-retardant PP material.
PUM
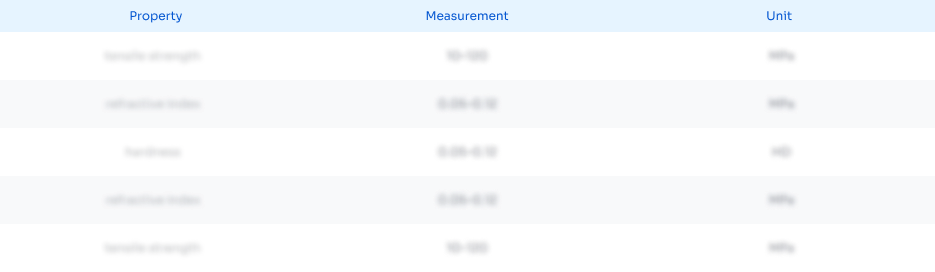
Abstract
Description
Claims
Application Information

- R&D
- Intellectual Property
- Life Sciences
- Materials
- Tech Scout
- Unparalleled Data Quality
- Higher Quality Content
- 60% Fewer Hallucinations
Browse by: Latest US Patents, China's latest patents, Technical Efficacy Thesaurus, Application Domain, Technology Topic, Popular Technical Reports.
© 2025 PatSnap. All rights reserved.Legal|Privacy policy|Modern Slavery Act Transparency Statement|Sitemap|About US| Contact US: help@patsnap.com