Preparation method for molybdenum disulfide/nitrogen-doped graphene three-dimensional composite material and application of molybdenum disulfide/nitrogen-doped graphene three-dimensional composite material
A nitrogen-doped graphene and molybdenum disulfide technology, applied in the field of energy storage materials, can solve the problems of inability to adapt to large-scale production of electrode materials and low yield
- Summary
- Abstract
- Description
- Claims
- Application Information
AI Technical Summary
Problems solved by technology
Method used
Image
Examples
Embodiment 1
[0028] Add molybdenum disulfide powder and N-methylpyrrolidone solvent into the autoclave, react at 210°C for 2 hours, and after cooling, use the probe ultrasonic pulverizer to ultrasonicate the molybdenum disulfide N-methylpyrrolidone solution for 1 hour, and then disperse The solution was centrifuged at 1500 rpm for 40 minutes, and the upper layer was the stripped molybdenum disulfide / N-methylpyrrolidone dispersion. Add the molybdenum disulfide / N-methylpyrrolidone dispersion with a solute mass of 30 mg into the graphene oxide aqueous solution with a solute mass of 30 mg, and stir to form a uniform molybdenum disulfide / graphene oxide dispersion. Add 300 mg of sodium chloride and stir until completely dissolved. After 24 hours of coagulation of the dispersion, the flocs in the lower layer are centrifuged to obtain a molybdenum disulfide / graphene oxide three-dimensional assembly. Add hydrazine hydrate solution (mass fraction 80%, 10ml) to molybdenum disulfide / graphene oxide, re...
Embodiment 2
[0030] Add molybdenum disulfide powder and N-methylpyrrolidone solvent into the autoclave, react at 220°C for 3 hours, and after cooling, use the probe ultrasonic pulverizer to ultrasonicate the molybdenum disulfide N-methylpyrrolidone solution for 1 hour, and then disperse The solution was centrifuged at 1500 rpm for 45 minutes, and the upper layer was the stripped molybdenum disulfide / N-methylpyrrolidone dispersion. The molybdenum disulfide / N-methylpyrrolidone dispersion with a solute mass of 60 mg was added to the graphene oxide aqueous solution with a solute mass of 30 mg, and stirred to form a uniform molybdenum disulfide / graphene oxide dispersion. Add 300 mg of sodium chloride and stir until completely dissolved. After 24 hours of coagulation of the dispersion, the flocs in the lower layer are centrifuged to obtain a molybdenum disulfide / graphene oxide three-dimensional assembly. Add hydrazine hydrate solution (mass fraction 80%, 12ml) to molybdenum disulfide / graphene ox...
Embodiment 3
[0032] Add molybdenum disulfide powder and N-methylpyrrolidone solvent into the autoclave, react at 220°C for 3 hours, and after cooling, use the probe ultrasonic pulverizer to ultrasonicate the molybdenum disulfide N-methylpyrrolidone solution for 1 hour, and then disperse The solution was centrifuged at 1500 rpm for 45 minutes, and the upper layer was the stripped molybdenum disulfide / N-methylpyrrolidone dispersion. The molybdenum disulfide / N-methylpyrrolidone dispersion with a solute mass of 90 mg was added to the graphene oxide aqueous solution with a solute mass of 30 mg, and stirred to form a uniform molybdenum disulfide / graphene oxide dispersion. Add 300 mg of sodium chloride and stir until completely dissolved. After 24 hours of coagulation of the dispersion, the flocs in the lower layer are centrifuged to obtain a molybdenum disulfide / graphene oxide three-dimensional assembly. Add hydrazine hydrate solution (mass fraction 80%, 12ml) to molybdenum disulfide / graphene ox...
PUM
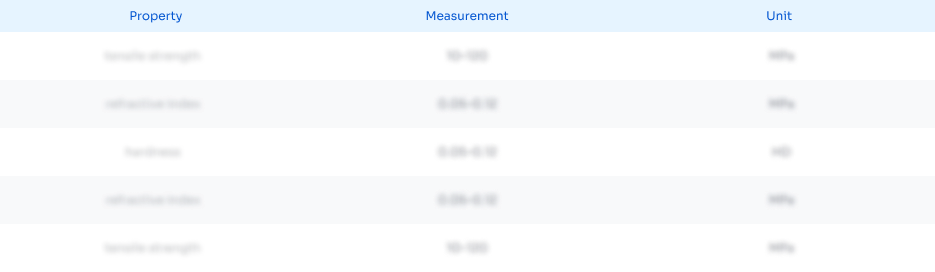
Abstract
Description
Claims
Application Information

- R&D Engineer
- R&D Manager
- IP Professional
- Industry Leading Data Capabilities
- Powerful AI technology
- Patent DNA Extraction
Browse by: Latest US Patents, China's latest patents, Technical Efficacy Thesaurus, Application Domain, Technology Topic, Popular Technical Reports.
© 2024 PatSnap. All rights reserved.Legal|Privacy policy|Modern Slavery Act Transparency Statement|Sitemap|About US| Contact US: help@patsnap.com