Method for reducing molten steel nitrogen in steelmaking link
A molten steel and link technology, applied in the direction of manufacturing converters, etc., can solve the problems of inability to reduce nitrogen absorption in molten steel, inability to directly reduce post-blowing, difficult operation of ore addition, etc., and achieve good application effects, increase costs, and normal and stable processes. Effect
- Summary
- Abstract
- Description
- Claims
- Application Information
AI Technical Summary
Problems solved by technology
Method used
Examples
Embodiment Construction
[0018] A method for reducing molten steel nitrogen in the steelmaking link provided by the invention comprises the following steps:
[0019] Step S1: Controlling the reblowing parameters of the converter and adjusting them in stages;
[0020] Sampling and testing by comparison test, analyzing the data (TSO assay nitrogen), summing up that it is beneficial to control nitrogen to appropriately reduce the reblowing flow rate in the middle and later stages of blowing and tapping process For control, from the initial when the oxygen supply is 0%-50%, the re-blowing argon flow is controlled at 300m 3 / h, when the oxygen supply is 50%-80%, the reblowing argon flow rate is controlled at 480m 3 / h, when the oxygen supply is 80%-100%, the reblowing argon flow rate is controlled at 600m 3 / h, the re-blowing argon flow rate in the tapping process is controlled at 300m 3 / h. Adjusted so that when the oxygen supply is 0%-50%, the reblowing argon flow is controlled at 300m 3 / h, when th...
PUM
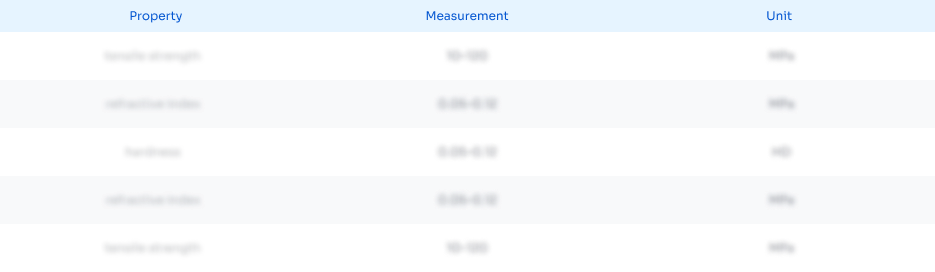
Abstract
Description
Claims
Application Information

- R&D
- Intellectual Property
- Life Sciences
- Materials
- Tech Scout
- Unparalleled Data Quality
- Higher Quality Content
- 60% Fewer Hallucinations
Browse by: Latest US Patents, China's latest patents, Technical Efficacy Thesaurus, Application Domain, Technology Topic, Popular Technical Reports.
© 2025 PatSnap. All rights reserved.Legal|Privacy policy|Modern Slavery Act Transparency Statement|Sitemap|About US| Contact US: help@patsnap.com