Method for directly extracting vanadium from high-calcium vanadium slag by roasting-alkali leaching
A technology of alkali leaching and vanadium slag is applied in the field of direct roasting of high-calcium vanadium slag-alkali leaching vanadium, which can solve problems such as vanadium extraction from high-calcium vanadium slag, and achieve the effects of improving purity, simple operation process and low price.
- Summary
- Abstract
- Description
- Claims
- Application Information
AI Technical Summary
Problems solved by technology
Method used
Examples
Embodiment 1
[0027] CaO / V 2 o 5 The high-calcium-vanadium slag with a molar ratio of 5 was crushed, sieved with a 200-mesh sieve, and the under-sieve was put into a muffle furnace, and roasted at 950°C for 2.5h. During the roasting process, the furnace door of the muffle furnace is half-opened to ensure that the entire roasting process is in an oxidizing atmosphere. And stir once every 15 minutes during the roasting process to prevent the vanadium slag from sticking during the roasting process, resulting in insufficient oxidation of the vanadium slag. After roasting, take out the vanadium slag clinker and cool it to room temperature in air.
[0028] The roasted vanadium slag clinker is crushed, sieved with a 200-mesh sieve, and the undersize is collected. Measure 48 mL of sodium carbonate solution with a concentration of 160 g / L with a graduated cylinder, first pour 40 mL of sodium carbonate solution into the three-necked bottle, then weigh 4 g of vanadium slag clinker and pour it into ...
Embodiment 2
[0031] CaO / V 2 o 5 The high-calcium-vanadium slag with a molar ratio of 4 was crushed, sieved with a 200-mesh sieve, and the under-sieved material was put into a muffle furnace and calcined at 750 °C for 2 h. During the roasting process, the furnace door of the muffle furnace is half-opened to ensure that the entire roasting process is in an oxidizing atmosphere. And stir once every 15 minutes during the roasting process to prevent the vanadium slag from sticking during the roasting process, resulting in insufficient oxidation of the vanadium slag. After roasting, take out the vanadium slag clinker and cool it to room temperature in air.
[0032]The roasted vanadium slag clinker is crushed, sieved with a 200-mesh sieve, and the undersize is collected. Use a measuring cylinder to measure 32 mL of sodium carbonate solution with a concentration of 100 g / L, first pour 25 mL of sodium carbonate solution into a three-necked bottle, then weigh 4 g of vanadium slag clinker and pour...
Embodiment 3
[0035] CaO / V 2 o 5 The high-calcium-vanadium slag with a molar ratio of 3 was crushed, sieved with a 200-mesh sieve, and the under-sieved material was put into a muffle furnace and calcined at 600 °C for 1.5 h. During the roasting process, the furnace door of the muffle furnace is half-opened to ensure that the entire roasting process is in an oxidizing atmosphere. And stir once every 15 minutes during the roasting process to prevent the vanadium slag from sticking during the roasting process, resulting in insufficient oxidation of the vanadium slag. After roasting, take out the vanadium slag clinker and cool it to room temperature in air.
[0036] The roasted vanadium slag clinker is crushed, sieved with a 200-mesh sieve, and the undersize is collected. Use a graduated cylinder to measure 16 mL of sodium carbonate solution with a concentration of 40 g / L, first pour 10 mL of sodium carbonate solution into a three-necked bottle, then weigh 4 g of vanadium slag clinker and po...
PUM
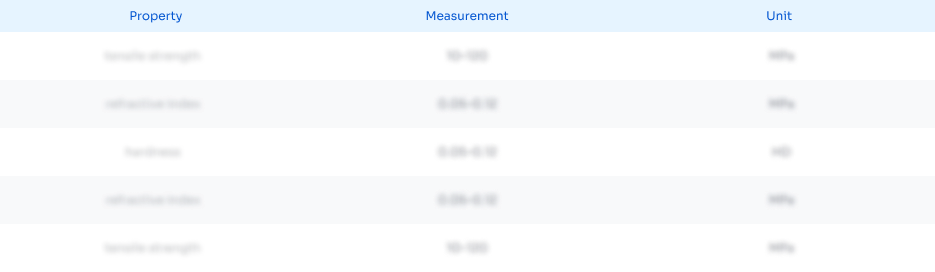
Abstract
Description
Claims
Application Information

- Generate Ideas
- Intellectual Property
- Life Sciences
- Materials
- Tech Scout
- Unparalleled Data Quality
- Higher Quality Content
- 60% Fewer Hallucinations
Browse by: Latest US Patents, China's latest patents, Technical Efficacy Thesaurus, Application Domain, Technology Topic, Popular Technical Reports.
© 2025 PatSnap. All rights reserved.Legal|Privacy policy|Modern Slavery Act Transparency Statement|Sitemap|About US| Contact US: help@patsnap.com