Preparation method of epoxy anticorrosive coating
An epoxy anti-corrosion coating, weight percentage technology, applied in the direction of anti-corrosion coatings, epoxy resin coatings, polyurea/polyurethane coatings, etc., can solve the problems of corrosion and corrosion medium seeping into the film, and achieve reduced viscosity, low cost, Effect of improving impact resistance
- Summary
- Abstract
- Description
- Claims
- Application Information
AI Technical Summary
Problems solved by technology
Method used
Examples
Embodiment 1
[0016] The preparation method of epoxy anticorrosion coating is:
[0017] (1) By weight, weigh 150g deionized water, 300g bisphenol A epoxy resin, 150g phenalkamine, 100g silicone, 85g polyurethane, 100g nitrile rubber, 5g dispersant, 4g defoamer, 4g anti-corrosion agent, and added to the dispersion tank together, dispersed and stirred at the speed of 300-500r / min in the dispersion tank for 5-10 minutes to obtain a mixture.
[0018] (2) Weigh 100g of flaky high wear-resistant pigments and fillers and 2g of leveling agent into the mixture, disperse and stir at the speed of 1000-1500r / min in the dispersion tank for 10-15 minutes to obtain an epoxy anti-corrosion coating. The flaky high wear-resistant pigments and fillers consist of 320 mesh glass flakes with a content of 2g, 160 mesh glass flakes with a content of 3g and sericite powder with a content of 5g.
Embodiment 2
[0020] The preparation method of epoxy anticorrosion coating is:
[0021] (1) By weight, weigh 160g deionized water, 400g bisphenol A epoxy resin, 80g phenalkamine, 50g silicone, 50g polyurethane, 120g nitrile rubber, 9g dispersant, 8g defoamer, 8g anticorrosion agent, and added to the dispersion tank together, dispersed and stirred at the speed of 300-500r / min in the dispersion tank for 5-10 minutes to obtain a mixture.
[0022] (2) Weigh 110g of flaky high wear-resistant pigments and fillers and 5g of leveling agent into the mixture, disperse and stir at the speed of 1000-1500r / min in the dispersion tank for 10-15 minutes to obtain an epoxy anti-corrosion coating. The flaky high wear-resistant pigments and fillers consist of 320 mesh glass flakes with a content of 2g, 160 mesh glass flakes with a content of 3g and sericite powder with a content of 6g.
Embodiment 3
[0024] The preparation method of epoxy anticorrosion coating is:
[0025] (1) By weight, weigh 150g deionized water, 300g bisphenol A epoxy resin, 80g phenalkamine, 50g silicone, 100g polyurethane, 120g NBR, 9g dispersant, 8g defoamer, 8g anticorrosion agent, and added to the dispersion tank together, dispersed and stirred at the speed of 300-500r / min in the dispersion tank for 5-10 minutes to obtain a mixture.
[0026] (2) Weigh 170g of flaky high wear-resistant pigments and fillers and 5g of leveling agent into the mixture, disperse and stir at the speed of 1000-1500r / min in the dispersion tank for 10-15 minutes to obtain an epoxy anti-corrosion coating. The flaky high wear-resistant pigments and fillers consist of 320 mesh glass flakes with a content of 4g, 160 mesh glass flakes with a content of 6g, and sericite powder with a content of 7g.
PUM
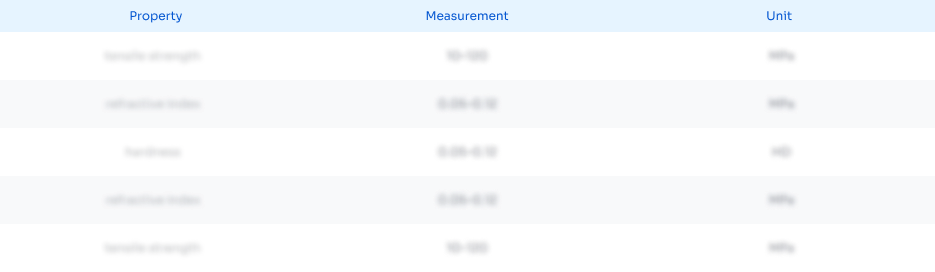
Abstract
Description
Claims
Application Information

- Generate Ideas
- Intellectual Property
- Life Sciences
- Materials
- Tech Scout
- Unparalleled Data Quality
- Higher Quality Content
- 60% Fewer Hallucinations
Browse by: Latest US Patents, China's latest patents, Technical Efficacy Thesaurus, Application Domain, Technology Topic, Popular Technical Reports.
© 2025 PatSnap. All rights reserved.Legal|Privacy policy|Modern Slavery Act Transparency Statement|Sitemap|About US| Contact US: help@patsnap.com