Magnesium alloy surface chromium-free composite passivation solution preparation process
A technology of passivation solution and magnesium alloy, which is applied in the coating process of metal materials, etc., to achieve the effects of fast film formation, high efficiency and good environmental protection effect
- Summary
- Abstract
- Description
- Claims
- Application Information
AI Technical Summary
Problems solved by technology
Method used
Examples
Embodiment 1
[0010] A preparation process for a chromium-free composite passivation solution on the surface of a magnesium alloy, the composition of the passivation solution is: the composition of the passivation solution used in the process is: sodium molybdate 12g / L, manganese dihydrogen phosphate 8g / L, phosphoric acid Calcium dihydrogen 4g / L, zinc oxide 16g / L, 85% phosphoric acid 26g / L, sodium nitrate 8g / L, calcium chlorate 2g / L, boric acid 4g / L, strontium chloride 1g / L, potassium peroxide 4g / L L, OP-100.3g / L, and the balance is deionized water; the preparation process is: take an appropriate amount of deionized water, dilute phosphoric acid, then slowly add zinc oxide that has been adjusted into a paste in advance, stir while adding, and wait until It is all dissolved, and then sequentially add sodium molybdate, manganese dihydrogen phosphate, calcium dihydrogen phosphate, sodium nitrate, calcium chlorate, boric acid, strontium chloride, potassium peroxide, OP-10 and the remaining deion...
Embodiment 2
[0012] A preparation process for a chromium-free composite passivation solution on the surface of a magnesium alloy, the composition of the passivation solution is: the composition of the passivation solution used in the process is: sodium molybdate 14g / L, manganese dihydrogen phosphate 6g / L, phosphoric acid Calcium dihydrogen 6g / L, zinc oxide 14g / L, 85% phosphoric acid 28g / L, sodium nitrate 6g / L, calcium chlorate 4g / L, boric acid 2g / L, strontium chloride 3g / L, potassium peroxide 2g / L L, OP-100.5g / L, and the balance is deionized water; the preparation process is: take an appropriate amount of deionized water, dilute phosphoric acid, then slowly add zinc oxide that has been adjusted into a paste in advance, stir while adding, and wait for It is completely dissolved, and then sequentially add sodium molybdate, manganese dihydrogen phosphate, calcium dihydrogen phosphate, sodium nitrate, calcium chlorate, boric acid, strontium chloride, potassium peroxide, OP-10 and the remaining ...
Embodiment 3
[0014] A preparation process for a chromium-free composite passivation solution on the surface of a magnesium alloy. The passivation solution is composed of: sodium molybdate 13g / L, manganese dihydrogen phosphate 7g / L, calcium dihydrogen phosphate 5g / L, zinc oxide 15g / L L, 85% phosphoric acid 27g / L, sodium nitrate 7g / L, calcium chlorate 3g / L, boric acid 3g / L, strontium chloride 2g / L, potassium peroxide 3g / L, OP-100.4g / L, balance It is deionized water; the preparation process is: take an appropriate amount of deionized water, dilute phosphoric acid, then slowly add zinc oxide that has been adjusted into a paste in advance, stir while adding, and wait for it to completely dissolve, then add sodium molybdate, Manganese dihydrogen phosphate, calcium dihydrogen phosphate, sodium nitrate, calcium chlorate, boric acid, strontium chloride, potassium peroxide, OP-10 and the remaining deionized water were added, stirred for 25 minutes, and then adjusted to pH 2.5.
PUM
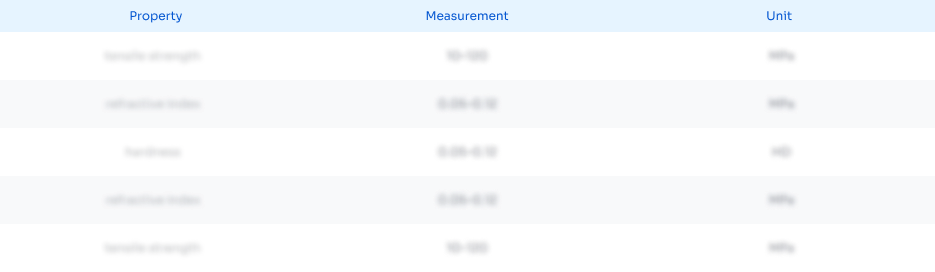
Abstract
Description
Claims
Application Information

- Generate Ideas
- Intellectual Property
- Life Sciences
- Materials
- Tech Scout
- Unparalleled Data Quality
- Higher Quality Content
- 60% Fewer Hallucinations
Browse by: Latest US Patents, China's latest patents, Technical Efficacy Thesaurus, Application Domain, Technology Topic, Popular Technical Reports.
© 2025 PatSnap. All rights reserved.Legal|Privacy policy|Modern Slavery Act Transparency Statement|Sitemap|About US| Contact US: help@patsnap.com