Converter steelmaking method
A converter steelmaking and converter technology, applied in the field of mechanical forging, can solve the problems of inability to efficiently reduce the sulfur content of molten iron, inability to reuse scrap steel blocks, and inability to efficiently remove them, so as to achieve small loss and heat loss, The effect of low cost and not easy to crack
- Summary
- Abstract
- Description
- Claims
- Application Information
AI Technical Summary
Problems solved by technology
Method used
Examples
Embodiment 1
[0033] In the molten iron mixing process, the converter is a cylindrical converter with a simple shape and convenient masonry. The furnace shell is easy to manufacture. The inner shape of the molten pool is relatively close to the track of the molten metal circulation. When the diameter of the molten pool is large enough, it can ensure a large The blowing under the oxygen supply intensity can minimize the spatter, and can also ensure a sufficient depth of the molten pool, so that the furnace lining has a longer life.
[0034] When loading the scrap steel block, use the scrap steel feeding car to load the scrap steel block into the converter.
[0035] In the gun down process, the oxygen passing time is 18min-22min.
[0036] The ingredients added to the slag are lime, fluorite, iron oxide scale and iron ore.
Embodiment 2
[0038] The rest is the same as the above-mentioned Example 1, except that the converter in the iron mixing process is a conical-spherical converter. Compared with the cylindrical-spherical converter with the same capacity, if the depth of the molten pool is the same, the molten The area of the pool is larger than that of the cylindrical type, which is beneficial to the metallurgical reaction. At the same time, the change of the molten pool is small with the erosion of the lining, which is beneficial to the steelmaking operation.
Embodiment 3
[0040] All the other are identical with described embodiment 1, and difference is, in lower gun process, the oxygen of the purity more than 99.5% that injects is changed into air, simultaneously, add the lime powder that oxygen content is equal, heat can be reduced , The resulting product does not affect the use effect.
[0041] The present invention is applicable to steelmaking methods using other furnaces, such as changing the converter in 2) to an electric furnace, and the temperature in the furnace is controlled at about 1300°C.
[0042] It can be known from practical application that the present invention desulfurizes the molten iron in the mixed iron car, so the cost is low and the efficiency is high. The method of supplying the molten iron by the molten iron tank car has little loss of molten iron and heat loss, saves energy, and adds scrap steel blocks to the converter. The scrap steel block can be reused, which saves resources and is more environmentally friendly. The...
PUM
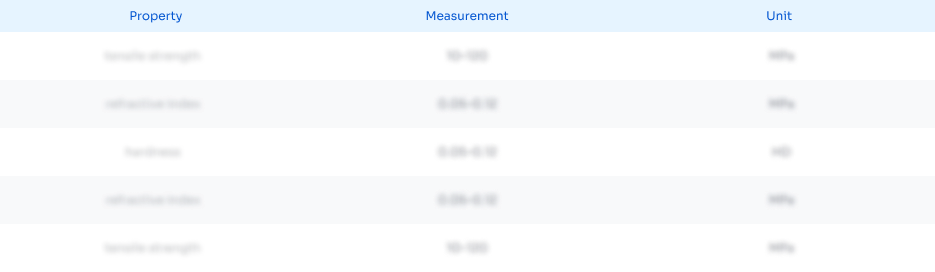
Abstract
Description
Claims
Application Information

- R&D
- Intellectual Property
- Life Sciences
- Materials
- Tech Scout
- Unparalleled Data Quality
- Higher Quality Content
- 60% Fewer Hallucinations
Browse by: Latest US Patents, China's latest patents, Technical Efficacy Thesaurus, Application Domain, Technology Topic, Popular Technical Reports.
© 2025 PatSnap. All rights reserved.Legal|Privacy policy|Modern Slavery Act Transparency Statement|Sitemap|About US| Contact US: help@patsnap.com