Preparation method and application of light alkane dehydrogenation catalyst with high thermal stability
A dehydrogenation catalyst, high thermal stability technology, applied in the direction of hydrocarbons, hydrocarbons, metal/metal oxide/metal hydroxide catalysts, etc., can solve the problem of carrier specific surface area decrease, catalyst activity decrease, active component Agglomeration and other problems, to achieve the effect of inhibiting carbon deposition, low probability of sintering and α-phase transformation, and simple preparation process
- Summary
- Abstract
- Description
- Claims
- Application Information
AI Technical Summary
Problems solved by technology
Method used
Examples
Embodiment 1
[0022] The catalyst preparation process is as follows:
[0023] Step a. Add aluminum sulfate to NaOH aqueous solution, stir, continue to drop NaOH aqueous solution to adjust the pH of the mixed solution to 12, filter, wash with deionized water, add dilute nitric acid to form a sol, then add sodium silicate, stir, and filter , aged for 40 hours, formed into drop balls, and then dried at 120°C for 2 hours; roasted at 600°C for 3 hours to obtain Si-containing γ-Al 2 o 3 small ball;
[0024]Step b. γ-Al containing Si element obtained in step a 2 o 3 Immerse the small ball carrier in aqueous solution of lanthanum nitrate at 80°C for 4h, then dry at 120°C for 2h; roast at 450°C for 8h; then dip in aqueous solution of sodium chloride at 80°C for 4h, then dry at 120°C for 2h; ℃, roasting for 8h;
[0025] Step c. γ-Al containing Si elements loaded with La and Na elements obtained in step b 2 o 3 The small ball carrier was impregnated with chloroplatinic acid aqueous solution, ti...
Embodiment 2
[0030] The catalyst preparation process is as follows:
[0031] Step a. Add aluminum trichloride to the KOH aqueous solution, stir, continue to drop the KOH aqueous solution to adjust the pH of the mixed solution to 8, filter, wash with deionized water, add dilute nitric acid to form a sol, and then add ethyl orthosilicate , stirred, filtered, aged for 15 hours, formed into drop balls, and then dried at 100°C for 5 hours; roasted at 450°C for 8 hours to obtain Si-containing γ-Al 2 o 3 small ball;
[0032] Step b. γ-Al containing Si element obtained in step a 2 o 3 The pellet carrier was impregnated with cerium nitrate aqueous solution at 90°C for 3h, then dried at 100°C for 5h; calcined at 550°C for 5h; then at 90°C, immersed in magnesium chloride aqueous solution for 3h, and then dried at 120°C for 2h; at 550°C, Roasting 5h;
[0033] Step c. γ-Al containing Si elements loaded with Ce elements and Mg elements obtained in step b 2 o 3 The small ball carrier was impregnat...
Embodiment 3
[0038] The catalyst preparation process is as follows:
[0039] Step a. Add aluminum nitrate to the ammonia solution, stir, continue to drop the ammonia solution to adjust the pH of the mixed solution to 10, filter, wash with deionized water, add dilute nitric acid to form a sol, then add silica sol, stir, filter, Aging for 24 hours, forming drop balls, then drying at 80°C for 10 hours; roasting at 550°C for 5 hours to obtain Si-containing γ-Al 2 o 3 small ball;
[0040] Step b. Using the Si-containing γ-Al obtained in step a 2 o 3 Immerse the small ball carrier in aqueous solution of lanthanum nitrate at 70°C for 6 hours, then dry at 80°C for 10 hours; roast at 500°C for 6 hours; then impregnate the aqueous solution of potassium nitrate at 70°C for 6 hours, then dry at 80°C for 10 hours; , roasted for 6h;
[0041] Step c. Si element-containing γ-Al loaded with La and K elements obtained in step b 2 o 3 The small ball carrier was impregnated with chloroplatinic acid aqu...
PUM
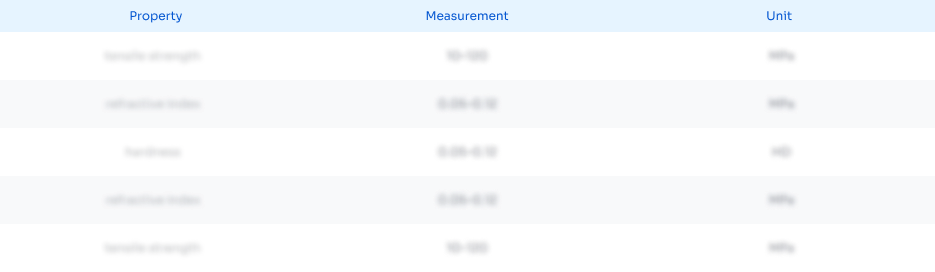
Abstract
Description
Claims
Application Information

- R&D Engineer
- R&D Manager
- IP Professional
- Industry Leading Data Capabilities
- Powerful AI technology
- Patent DNA Extraction
Browse by: Latest US Patents, China's latest patents, Technical Efficacy Thesaurus, Application Domain, Technology Topic, Popular Technical Reports.
© 2024 PatSnap. All rights reserved.Legal|Privacy policy|Modern Slavery Act Transparency Statement|Sitemap|About US| Contact US: help@patsnap.com