Industrial organic exhaust gas combustion catalyst and preparation method thereof
A technology for burning catalysts and organic waste gas, applied in chemical instruments and methods, physical/chemical process catalysts, metal/metal oxide/metal hydroxide catalysts, etc., can solve the problems of complex preparation process and reduced catalytic efficiency, and achieve The preparation process is simple, the reaction temperature is low, and the effect of low operating pressure difference
- Summary
- Abstract
- Description
- Claims
- Application Information
AI Technical Summary
Problems solved by technology
Method used
Image
Examples
Embodiment 1
[0028] Put 40.0g of alumina-coated cordierite honeycomb ceramic carrier in 3% dilute nitric acid solution for 3 hours, take it out and blow off the liquid in the pores with compressed air; then rinse with deionized water until it becomes neutral, and finally at 100 Dry in air at 120°C for 4 hours, and cool down for later use.
[0029] Weigh 6.16gCu(NO 3 ) 2 ·3H 2 O, 6.00g 50%Mn(NO 3 ) 2 , 8.34gFe(NO 3 ) 3 9H 2 O, 2.85gCe(NO 3 ) 4 , 0.35gAgNO 3 , respectively added deionized water to dissolve, mixed to obtain 65ml of active ingredient solution, and then added citric acid to adjust the pH value of the solution to 3. Immerse 20.0g of the surface-treated honeycomb ceramic carrier in the above solution, take it out after soaking for 10 minutes, blow off the remaining liquid in the pores with compressed air, dry it in the air at 100~120°C for 4 hours, and weigh it. The impregnation operation was repeated 4 times; finally, it was baked in air at 500°C for 5 hours to obtain...
Embodiment 2
[0031] Put 40.0g of alumina-coated mullite honeycomb ceramic carrier into 5% dilute nitric acid solution for 1 hour, take it out and blow off the liquid in the pores with compressed air; Dry in air at ~120°C for 4 hours, then cool for later use.
[0032] Weigh 10.56gCu(NO 3 ) 2 ·3H 2 O, 6.00g 50%Mn (NO 3 ) 2、 8.34g Fe(NO 3 ) 3 9H 2 O, 2.35gCe(NO 3 ) 4 , 0.52gAgNO 3 , respectively added deionized water to dissolve, mixed to obtain 70ml of active ingredient solution, and then added citric acid to adjust the pH of the solution to 2. Immerse 20.0g of the surface-treated honeycomb ceramic carrier in the above solution, take it out after immersion for 6 minutes, blow off the remaining liquid in the channels with compressed air, dry it in the air at 100~120°C for 3 hours, and weigh it. The impregnation operation was repeated three times; finally, it was baked in air at 550° C. for 7 hours to obtain a finished catalyst. The loading amount of active components calculated a...
Embodiment 3
[0034] Put 40.0g of alumina-coated cordierite honeycomb ceramic carrier in 5% dilute nitric acid solution for 0.5 hours, take it out and blow off the liquid in the pores with compressed air; then rinse with deionized water until it becomes neutral, and finally at 100 Dry in air at 120°C for 4 hours, and cool down for later use.
[0035] Weigh 5.56gCu(NO3 ) 2 ·3H 2 O, 4.05g50%Mn (NO 3 ) 2、 3.27g Fe(NO 3 ) 3 9H 2 O, 0.85gCe(NO 3 ) 4 , 0.16gAgNO 3 , respectively added deionized water to dissolve, mixed to obtain 60ml of active ingredient solution, and then added citric acid to adjust the pH value of the solution to 3. Immerse 20.0g of the surface-treated honeycomb ceramic carrier in the above solution, take it out after soaking for 10 minutes, blow off the remaining liquid in the pores with compressed air, dry it in the air at 100~120°C for 3 hours, and weigh it. The impregnation operation was repeated 5 times; finally, it was baked in air at 560°C for 7 hours to obtai...
PUM
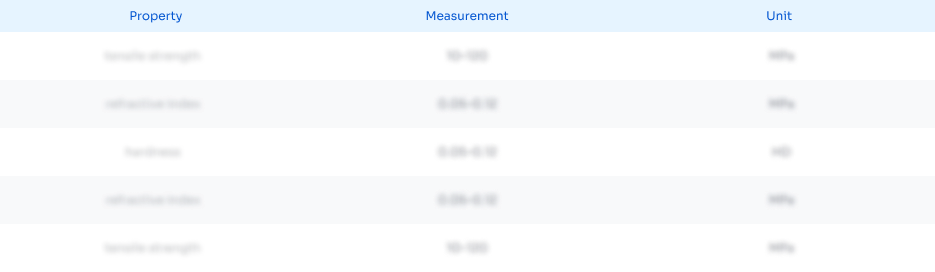
Abstract
Description
Claims
Application Information

- R&D Engineer
- R&D Manager
- IP Professional
- Industry Leading Data Capabilities
- Powerful AI technology
- Patent DNA Extraction
Browse by: Latest US Patents, China's latest patents, Technical Efficacy Thesaurus, Application Domain, Technology Topic, Popular Technical Reports.
© 2024 PatSnap. All rights reserved.Legal|Privacy policy|Modern Slavery Act Transparency Statement|Sitemap|About US| Contact US: help@patsnap.com