Process for recovering valuable metals from high-iron alloys
A technology for valuable metals and ferroalloys, which is applied in the technical field of recovering valuable metals from high-iron alloys, can solve the problems of low direct copper recovery rate, high cost of iron removal, increased consumption of copper extractant, etc., and shorten the process processes, reduce production costs, and avoid the effects of enrichment
- Summary
- Abstract
- Description
- Claims
- Application Information
AI Technical Summary
Problems solved by technology
Method used
Image
Examples
Embodiment 1
[0019] The mass percentage composition is Cu67.87%, Co5.71%, Fe23.46% high iron alloy powder, according to liquid-solid ratio 30:1 liquid-solid ratio is placed in the acidic solution that acid concentration is 0.3mol / L, according to 5g / Add additives, blow in air mixed with industrial oxygen for selective leaching, the reaction temperature is 90°C, filter after the reaction is completed, and the filter residue after drying is mainly goethite or hydrated iron oxide slag, and the composition is (mass percent % ) Cu 1, Co 0.08, Fe 50.1. The composition of the leaching solution (g / L) is Cu 44.83, Co 3.77, Fe 0.04, the leaching rate of copper is over 99%, and the leaching rate of cobalt is over 99.3%.
[0020] The selective leaching solution of the alloy is separated and purified by an extraction process. After copper extraction, the organic phase loaded with copper is stripped after copper electrolysis, and the obtained copper sulfate solution is removed from the copper electroly...
Embodiment 2
[0023] The mass percentage composition is Cu 12%, Co 5%, Fe 75% high iron alloy powder, according to the liquid-solid ratio of 5:1, the liquid-solid ratio is placed in the acidic solution with an acid concentration of 5mol / L, and the additive is added according to 20g / L. Bubble air mixed with industrial oxygen for selective leaching. The reaction temperature is 85°C at room temperature. After the reaction is completed, filter. The dried filter residue is mainly goethite or hydrated iron oxide slag. The composition is (mass percentage%) Cu 0.2, Co 0.05, Fe 56.1. The composition of the leaching solution (g / L) is Cu 20, Co 30, Fe 0.05, the leaching rate of copper is over 96%, and the leaching rate of cobalt is over 95%.
[0024] The leachate of the alloy is separated and purified by an extraction process. Copper extraction is first performed, and the copper sulfate solution obtained after the copper-loaded organic phase is back-extracted from the copper electrolysis solution is ...
PUM
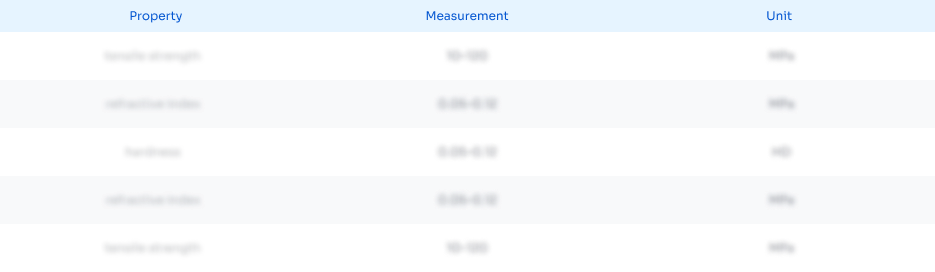
Abstract
Description
Claims
Application Information

- R&D
- Intellectual Property
- Life Sciences
- Materials
- Tech Scout
- Unparalleled Data Quality
- Higher Quality Content
- 60% Fewer Hallucinations
Browse by: Latest US Patents, China's latest patents, Technical Efficacy Thesaurus, Application Domain, Technology Topic, Popular Technical Reports.
© 2025 PatSnap. All rights reserved.Legal|Privacy policy|Modern Slavery Act Transparency Statement|Sitemap|About US| Contact US: help@patsnap.com