Micro-fluorine glass etching and polishing method
A technology of etching and polishing and micro-fluorine glass, which is applied in the field of glass etching and polishing and micro-fluorine glass etching and polishing, to achieve the effects of high safety, fast etching rate and large depth
- Summary
- Abstract
- Description
- Claims
- Application Information
AI Technical Summary
Problems solved by technology
Method used
Image
Examples
example 1
[0016] Sodium fluoride (inorganic salt 1) and sodium sulfate (inorganic salt 2) were ground separately, and then mixed with sodium dihydrogen phosphate and water in a weight ratio of 10:8:1:1 to prepare an etching solution. Then apply the etchant to the pretreated glass. After standing at 25°C for 1 hour, the glass surface was cleaned. The surface morphology was observed by scanning electron microscope. Pretreatment steps: ultrasonic washing (low frequency) - acid washing (mixture of dichromic acid and sulfuric acid in any proportion) - immersion in organic solvent acetone for 3 minutes - distilled water washing - heating - sticking a protective layer.
[0017] Such as figure 1 , It was found that the etching surface was uneven, the surface was whitish, there was side etching, and the etching depth was very small.
[0018] Experimental data: 17.4801 grams before etching and 17.4431 grams after etching
[0019] Erosion depth: m before etching - m after etching = 17.4801-17...
example 2
[0021] ① Grind sodium fluoride and sodium sulfate separately, and make an etching solution with sodium dihydrogen phosphate, water and starch (to adjust the viscosity of the solution) in a ratio of 10:8:1:1:5, and then mix the etching solution Apply to pre-treated glass. After standing at 28OC for 1 hour, the glass surface was cleaned. The surface morphology was observed by scanning electron microscopy, such as figure 2 .
[0022] Experimental data: 17.0375 grams before etching; 17.4063 grams after etching;
[0023] Erosion depth: m before etching - m after etching = 17.0375-17.4063 = 0.0375;
[0024] ②Grind sodium fluoride and sodium sulfate separately, and make an etching solution with sodium dihydrogen phosphate, water and starch (to adjust the viscosity of the solution) in a ratio of 10:8:1:6:5, and then mix the etching solution Apply to pre-treated glass. After being placed at 28OC for 1 hour, the glass surface was cleaned and its surface morphology was observed wit...
example 3
[0029] ①After grinding sodium fluoride and sodium sulfate separately, make etching solution with sodium dihydrogen phosphate, water, and active agent sodium tetraborate in a ratio of 10:8:1:1:5, and then apply the etching solution on the pretreatment After the good glass is placed at 28OC for 1 hour, the glass surface is cleaned. The surface morphology was observed by scanning electron microscopy, such as Figure 4 .
[0030] Experimental data: 17.2908 grams before etching; 17.1773 grams after etching;
[0031] Erosion depth: m before etching - m after etching = 17.2908-1773 = 0.1135;
[0032] ②Grind sodium fluoride and sodium sulfate separately, and make an etching solution with sodium dihydrogen phosphate, water, and active agent sodium tetraborate at a ratio of 10:8:1:6:5, and then apply the etching solution on the pre- Treated glass. After standing at 28OC for 1 hour, the glass surface was cleaned. The surface morphology was observed by scanning electron microscopy, s...
PUM
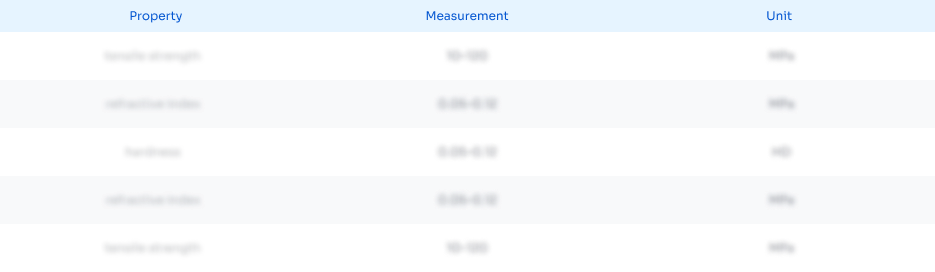
Abstract
Description
Claims
Application Information

- R&D
- Intellectual Property
- Life Sciences
- Materials
- Tech Scout
- Unparalleled Data Quality
- Higher Quality Content
- 60% Fewer Hallucinations
Browse by: Latest US Patents, China's latest patents, Technical Efficacy Thesaurus, Application Domain, Technology Topic, Popular Technical Reports.
© 2025 PatSnap. All rights reserved.Legal|Privacy policy|Modern Slavery Act Transparency Statement|Sitemap|About US| Contact US: help@patsnap.com