Thermoplastic polyurethane sheath material for automobile cables and preparation method thereof
A thermoplastic polyurethane, automotive cable technology, used in plastic/resin/wax insulators, organic insulators, etc., can solve the problems of limited use range, poor wear resistance, low impact strength, etc., achieve good physical and mechanical properties, wide range of uses, excellent The effect of abrasion resistance
- Summary
- Abstract
- Description
- Claims
- Application Information
AI Technical Summary
Problems solved by technology
Method used
Image
Examples
Embodiment Construction
[0013] A thermoplastic polyurethane sheathing material for automobile cables is prepared from the following raw materials in parts by weight: thermoplastic polyurethane 70, chlorosulfonated polyethylene 30, polybutylene succinate 20, aluminum diethylphosphinate 15, tripropyl borate 8, zinc tripolyphosphate 4, polytetrahydrofuran 6, rubber seed oil 8, calcium stearate 1.5, zinc stearate 2, chlorinated paraffin 5, bis(dodecylthio) dibutyltin 2.5, isopropyl dioleic acid acyloxy (dioctyl phosphoric acid acyloxy) titanate 2, p-nitrosophenol 2.5, toluene-2,4-diisocyanate 3.5, butyryl tri-n-hexyl citrate 15 , asbestos powder 10, fumed silica 18, rhodochrosite 12, (2,4-di-tert-butylphenyl) phosphite triester 2.5, modified stone powder 12;
[0014] The preparation method of the modified stone powder is as follows: (1) Weigh coke gemstone, volcanic stone, and attapulgite in a weight ratio of 7:5:4, mix evenly, calcinate at 780° C. for 1.5 hours, naturally cool to room temperature, pulve...
PUM
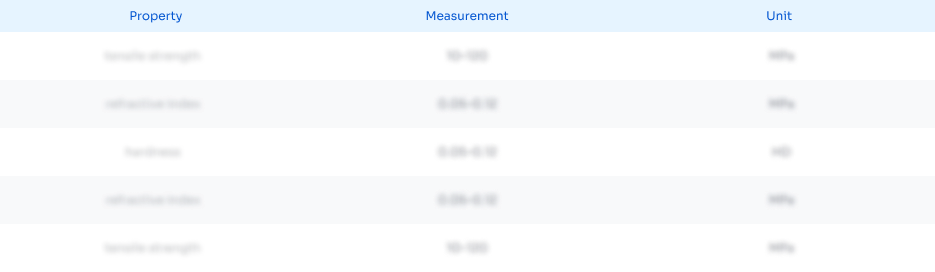
Abstract
Description
Claims
Application Information

- R&D Engineer
- R&D Manager
- IP Professional
- Industry Leading Data Capabilities
- Powerful AI technology
- Patent DNA Extraction
Browse by: Latest US Patents, China's latest patents, Technical Efficacy Thesaurus, Application Domain, Technology Topic, Popular Technical Reports.
© 2024 PatSnap. All rights reserved.Legal|Privacy policy|Modern Slavery Act Transparency Statement|Sitemap|About US| Contact US: help@patsnap.com