Mine wet mill liner and making method thereof
A wet method and lining technology, applied in the field of wear-resistant metal materials, can solve the problems of poor corrosion resistance and inapplicability of the lining of the tube mill, and achieve the advantages of reducing the frequency of replacing the lining, improving the service life and reducing the labor intensity. Effect
- Summary
- Abstract
- Description
- Claims
- Application Information
AI Technical Summary
Problems solved by technology
Method used
Image
Examples
Embodiment 1
[0024] (1) Smelting: Add clean and dry ordinary steel scrap, pig iron, stainless steel scrap, ferromolybdenum, nickel plate, and carbon-increasing waste electrodes into the smelting furnace, heat and melt, raise the temperature to 1550°C, and add them 10 minutes before tapping The preheated ferromanganese and ferrosilicon are subjected to precipitation deoxidation, the composition is adjusted, and then the preheated cobalt plate is added. When the temperature of the molten iron reaches 1550°C, the method of deep insertion of aluminum wire is used for diffusion deoxidation;
[0025] (2) Pouring: Crush the rare earth modifier into small pieces with a particle size of less than 45mm, and after drying below 200°C, place the package on the bottom of the ladle with iron sheet or tin foil paper, and use the method of pouring into the ladle to modify the molten steel. Then pour the molten steel into the steel ingot mold, the pouring temperature of the molten steel is 1460°C, the pourin...
Embodiment 2
[0029] (1) Smelting: Add clean and dry ordinary steel scrap, pig iron, stainless steel scrap, ferromanganese, ferromolybdenum, nickel plate, and carbon-increasing waste electrodes into the smelting furnace, heat and melt, and raise the temperature to 1300°C after adjusting the composition to pass , add ferrosilicon for precipitation deoxidation, 5 minutes before tapping the iron, adopt the method of deep insertion of aluminum wire for diffusion deoxidation, and then tap the iron;
[0030] (2) Pouring: Break the modified rare earth into small pieces with a particle size of less than 45mm, and after drying at 200°C, place the package on the bottom of the ladle with iron sheet or tin foil paper, and use the method of pouring into the ladle to modify the molten steel. Then pour the molten steel into the ingot mold, the pouring temperature of the molten steel is 1440°C, the pouring is first slow, medium fast, and then thin, and the steel ingot is poured by the bottom pour method;
...
Embodiment 3
[0034](1) Smelting: Add clean and dry ordinary steel scrap, pig iron, stainless steel scrap, ferromanganese, ferromolybdenum, nickel plate, and carbon-increasing waste electrodes into the smelting furnace, heat and melt, and raise the temperature to 1350°C after adjusting the composition to pass , adding preheated ferrosilicon for precipitation deoxidation, 5 minutes before tapping the iron, use the method of deep insertion of aluminum wire for diffusion deoxidation, and then tap the iron;
[0035] (2) Pouring: Break the modified rare earth into small pieces with a particle size of less than 45mm, and after drying at 200°C, place the package on the bottom of the ladle with iron sheet or tin foil paper, and use the method of pouring into the ladle to modify the molten steel. Then pour the molten steel into the ingot mold, the pouring temperature of the molten steel is 1450°C, the pouring is first slow, medium fast, and then thin, and the steel ingot is poured by the bottom pour ...
PUM
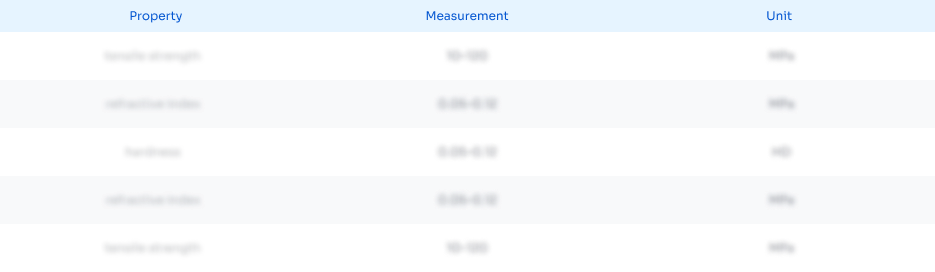
Abstract
Description
Claims
Application Information

- R&D Engineer
- R&D Manager
- IP Professional
- Industry Leading Data Capabilities
- Powerful AI technology
- Patent DNA Extraction
Browse by: Latest US Patents, China's latest patents, Technical Efficacy Thesaurus, Application Domain, Technology Topic, Popular Technical Reports.
© 2024 PatSnap. All rights reserved.Legal|Privacy policy|Modern Slavery Act Transparency Statement|Sitemap|About US| Contact US: help@patsnap.com