Cycloaliphatic epoxy polyurethane acrylate ultraviolet-curable coating and preparation method of ultraviolet-curable coating
A technology of epoxy urethane acrylate and urethane acrylate, which is applied in polyurea/polyurethane coatings, coatings, etc., can solve the problems of brittle coating films and small molecular weight of prepolymers, and achieve good flexibility, small shrinkage, and Strong impact resistance
- Summary
- Abstract
- Description
- Claims
- Application Information
AI Technical Summary
Problems solved by technology
Method used
Image
Examples
Embodiment 1
[0034] Step 1: Synthesis of urethane acrylate
[0035] Add 222kg of isophorone diisocyanate, 5kg of p-hydroxyanisole, and 11kg of dibutyltin dilaurate into a reaction kettle equipped with a stirring device and a temperature control system, heat up to 25°C after mixing, and slowly add 130kg of acrylic acid under stirring Hydroxypropyl ester, then heated up to 30°C, reacted for 1 hour, and discharged to obtain polyurethane acrylate.
[0036] Step 2: Preparation of Modified Cycloaliphatic Epoxy Resin
[0037] Add 98kg maleic anhydride and 200kg polyethylene glycol (average molecular weight is 200) in the reaction kettle equipped with stirring device and temperature control system, and add 0.5kg polymerization inhibitor p-hydroxyanisole, and heat up to 75°C After 1.5 hours of stirring, the reaction was stopped to obtain maleic anhydride polyethylene glycol monoester, and then the temperature of the system was raised to 100 ° C, and 504 kg of alicyclic epoxy resin——3,4-cyclocyclic...
Embodiment 2
[0044] Step 1: Synthesis of urethane acrylate
[0045] Same as Example 1.
[0046] Step 2: Preparation of Modified Cycloaliphatic Epoxy Resin
[0047]Add 98kg maleic anhydride and 800kg polyethylene glycol (average molecular weight is 800) in the reactor that stirring device, temperature control system are housed, and add 1.4kg inhibitor p-hydroxyanisole, be heated up to 85 ℃ , stop the reaction after reacting under stirring for 1 hour to obtain maleic anhydride polyethylene glycol monoester, then raise the system temperature to 110°C, slowly add 166kg alicyclic epoxy resin——bis((3, 4-epoxycyclohexyl) methyl) adipate, and 0.5kg triethylamine, stop the reaction after 2 hours after the stirring reaction, cool down and discharge, and obtain a modified cycloaliphatic epoxy resin.
[0048] Step 3: Preparation of Modified Cycloaliphatic Epoxy Urethane Acrylate Prepolymer
[0049] Add 845kg of urethane acrylate monomer prepared in step 1 into a reaction kettle equipped with a stir...
Embodiment 3
[0054] Step 1: Synthesis of urethane acrylate
[0055] Same as Example 1.
[0056] Step 2: Preparation of Modified Cycloaliphatic Epoxy Resin
[0057] Add 98kg maleic anhydride and 400kg polypropylene glycol (average molecular weight is 400) in the reactor that stirrer, temperature control system are housed, and add 0.7kg inhibitor p-hydroxyanisole, be warming up to 65 ℃, in After reacting for 3 hours under stirring, the reaction was stopped to obtain polypropylene glycol monoester of maleic anhydride, then the temperature of the system was raised to 90° C., and 202 kg of cycloaliphatic epoxy resin——dicyclopentenyl ether dioxide was slowly added under the protection of nitrogen. And 0.6kg triethylamine, stirred for 8 hours to stop the reaction, cooled and discharged to prepare a modified cycloaliphatic epoxy resin.
[0058] Step 3: Preparation of Modified Cycloaliphatic Epoxy Urethane Acrylate Prepolymer
[0059] Add 422kg of urethane acrylate monomer prepared in step 1 int...
PUM
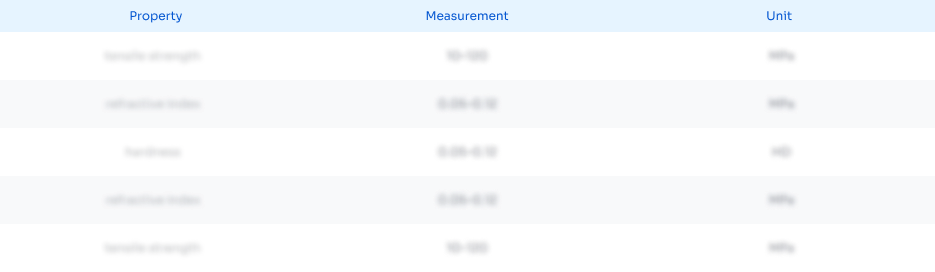
Abstract
Description
Claims
Application Information

- R&D
- Intellectual Property
- Life Sciences
- Materials
- Tech Scout
- Unparalleled Data Quality
- Higher Quality Content
- 60% Fewer Hallucinations
Browse by: Latest US Patents, China's latest patents, Technical Efficacy Thesaurus, Application Domain, Technology Topic, Popular Technical Reports.
© 2025 PatSnap. All rights reserved.Legal|Privacy policy|Modern Slavery Act Transparency Statement|Sitemap|About US| Contact US: help@patsnap.com