Metallization production method of efficient solar cells
A technology for solar cells and manufacturing methods, applied in the direction of final product manufacturing, sustainable manufacturing/processing, circuits, etc., can solve the problems of poor cell surface passivation effect, inability to print cell surface, large cell series resistance, etc., and achieve high conversion Efficiency, reduce manufacturing costs, improve the effect of short-circuit current
- Summary
- Abstract
- Description
- Claims
- Application Information
AI Technical Summary
Problems solved by technology
Method used
Examples
Embodiment 1
[0057] Monocrystalline single-sided solar cells:
[0058] After the monocrystalline silicon wafer is subjected to alkali texturing, it is polished and chemically cleaned with PSG equipment. After texturing and diffusion is completed, a 20nm silicon dioxide film is completed on the front and back of the cell, and then a 60nm silicon nitride film is prepared. , the first layer of grid lines made on the front of the cell by screen printing technology, the height is about 8μm±2μm, and then the aluminum back field and back electrode are manufactured by screen printing technology. After back sintering. With the new technology of the present invention, the gate line of the front electrode of the battery sheet is extended to a width of 40um, and 10um±2μm is superimposed on the original height. After annealing, a high-conversion and low-cost monocrystalline silicon single-sided battery is finally realized.
Embodiment 2
[0060] Monocrystalline bifacial solar cells:
[0061] After the monocrystalline silicon wafer is subjected to alkali texturing, it is polished and chemically cleaned with PSG equipment. After texturing and diffusion is completed, a 20nm silicon dioxide film is completed on the front and back of the cell, and then a 60nm silicon nitride film is prepared. , use screen printing technology to make the first layer of grid lines on the electrodes on both sides of the cell, with a height of about 8μm±2μm (no need to prepare aluminum back field and back electrode). Using the new technology of the present invention, the grid line of the front electrode of the battery sheet is extended to a width of 40um, and 10um±2μm is superimposed on the original height. After annealing, a single-crystal silicon double-sided battery with high conversion efficiency and low cost is finally realized .
Embodiment 3
[0063] Polycrystalline single-sided solar cells:
[0064] After the polycrystalline silicon wafer is acid-textured, it is polished and chemically cleaned with PSG equipment. After texturing and diffusion is completed, a 20nm silicon dioxide film is completed on the front and back of the cell, and then a 60nm silicon nitride film is prepared. The first layer of grid lines made by screen printing technology on the front of the cell has a height of about 8 μm ± 2 μm, and then the aluminum back field and back electrode are manufactured by screen printing technology. After back sintering. Using the new technology of the present invention, the grid line of the front electrode of the battery sheet is extended to a width of 40um, and the original height is superimposed on the original height of 10um±2μm. After annealing, a high conversion efficiency and low-cost monocrystalline silicon single-sided battery is finally realized .
PUM
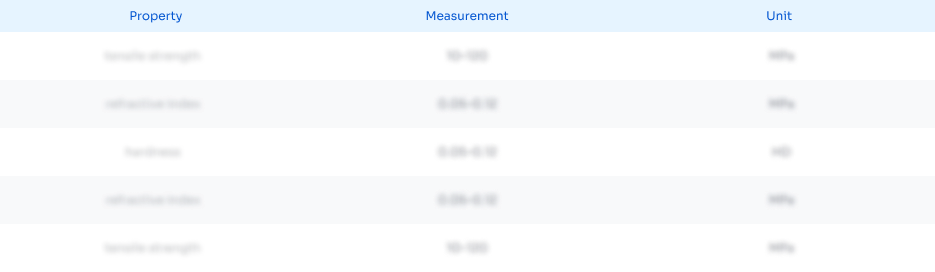
Abstract
Description
Claims
Application Information

- R&D
- Intellectual Property
- Life Sciences
- Materials
- Tech Scout
- Unparalleled Data Quality
- Higher Quality Content
- 60% Fewer Hallucinations
Browse by: Latest US Patents, China's latest patents, Technical Efficacy Thesaurus, Application Domain, Technology Topic, Popular Technical Reports.
© 2025 PatSnap. All rights reserved.Legal|Privacy policy|Modern Slavery Act Transparency Statement|Sitemap|About US| Contact US: help@patsnap.com