Thin-wall part complex working condition machining state monitoring method
A technology of processing state and complex working conditions, which is applied in the direction of instruments, computer control, simulators, etc., can solve the problems of complex thin-walled parts, single processing state monitoring items, and inability to reflect the coupling effect of various processing states, so as to ensure the quality of processing Quality, cost reduction effect
- Summary
- Abstract
- Description
- Claims
- Application Information
AI Technical Summary
Problems solved by technology
Method used
Image
Examples
Embodiment Construction
[0040] The following structural drawings and embodiments further illustrate the present invention.
[0041] like Figure 1-13 shown.
[0042] In this embodiment, aluminum alloy is used as the cutting test material, and a cemented carbide end mill is used as the cutting tool. The Kistler amplifier is used to collect mechanical signals, and the acceleration sensor is used to collect vibration signals.
[0043] figure 1 It is a flow chart of the complex working condition processing state monitoring method based on multi-sensor fusion and support vector machine of the present invention. like figure 1 As shown, a method for monitoring the processing status of thin-walled parts under complex working conditions, which includes the following steps:
[0044] 1. Test environment
[0045] The test conditions of this embodiment include a five-axis numerical control machine tool, a three-way dynamometer, and an acceleration sensor; two cutting tools are used: a non-wearing tool; and a...
PUM
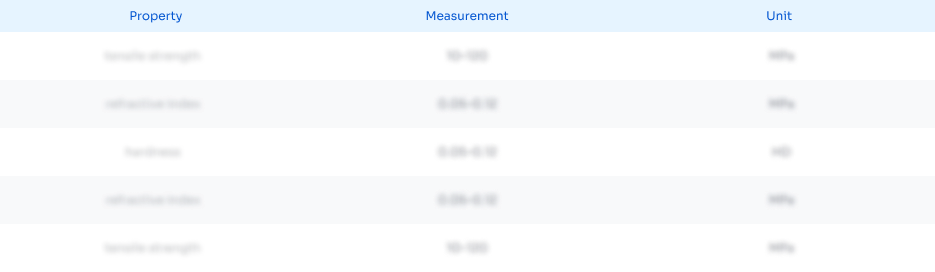
Abstract
Description
Claims
Application Information

- R&D
- Intellectual Property
- Life Sciences
- Materials
- Tech Scout
- Unparalleled Data Quality
- Higher Quality Content
- 60% Fewer Hallucinations
Browse by: Latest US Patents, China's latest patents, Technical Efficacy Thesaurus, Application Domain, Technology Topic, Popular Technical Reports.
© 2025 PatSnap. All rights reserved.Legal|Privacy policy|Modern Slavery Act Transparency Statement|Sitemap|About US| Contact US: help@patsnap.com