Preparation method of graphite film with high heat conductivity
A technology of high thermal conductivity graphite and graphite film, applied in chemical instruments and methods, inorganic chemistry, non-metallic elements, etc., can solve the problems of reduced thermal conductivity and heat dissipation performance, high cost of copper sheet, non-corrosion resistance, etc., and achieve a good degree of bubbles , Good cell domain size, high heat dissipation effect
- Summary
- Abstract
- Description
- Claims
- Application Information
AI Technical Summary
Problems solved by technology
Method used
Examples
Embodiment 1
[0023] First choose polyimide as the raw material, the thickness of polyimide is 15μm, and the thickness of graphite paper is 2mm. 1 piece of polyimide film, cross-stacked, and finally placed in a graphite boat. Then vacuumize the carbonization furnace to less than 5-10Pa, and then put the graphite boat filled with raw materials into the carbonization furnace for carbonization. It takes 0.5h to raise the temperature to 200°C in the first stage, 0.5h to 400°C in the second stage, and 0.5h to raise the temperature to 400°C in the third stage. It takes 1 hour to raise the temperature to 600°C for the first stage, 1 hour for the fourth stage to 800°C, 2.5 hours for the fifth stage to 1000°C, and 2.5 hours for the sixth stage to 1200°C. Finally, the carbonized material is moved to a graphitization furnace, and 20 g / cm2 is applied to the material, and it is carried out under an argon atmosphere. It takes 2 hours to raise the temperature to 1800°C, 2 hours to raise the temperature t...
Embodiment 2
[0025] First select polybenzoxazole as the raw material, the thickness is 30 μm, and the thickness of graphite paper is 3 mm. Cut the polybenzoxazole and graphite paper into a certain size for later use, and put 10 pieces of polybenzoxazole between every two pieces of graphite paper. Benzoxazole thin films, cross-stacked, and finally placed in graphite boats. Then vacuumize the carbonization furnace to less than 5-10Pa, and then put the graphite boat filled with raw materials into the carbonization furnace for carbonization. It takes 0.5h to raise the temperature to 200°C in the first stage, 0.5h to 400°C in the second stage, and 0.5h to raise the temperature to 400°C in the third stage. It takes 0.5 hours to raise the temperature to 600°C in the first stage, 1.5 hours to raise the temperature to 800°C in the fourth stage, 2 hours to raise the temperature to 1000°C in the fifth stage, and 3 hours to raise the temperature to 1200°C in the sixth stage. Finally, move the carboniz...
Embodiment 3
[0027] First select polythiazole as raw material, the thickness is 50 μm, and the thickness of graphite paper is 4 mm. Cut the polythiazole and graphite paper into a certain size and specification for later use. Put 30 pieces of polythiazole film between every two pieces of graphite paper, and stack them crosswise , and finally placed in a graphite boat. Then vacuumize the carbonization furnace to less than 5-10Pa, and then put the graphite boat filled with raw materials into the carbonization furnace for carbonization. It takes 0.5h to raise the temperature to 200°C in the first stage, 0.5h to 400°C in the second stage, and 0.5h to raise the temperature to 400°C in the third stage. It takes 0.5 hours to raise the temperature to 600°C for the first stage, 1 hour for the fourth stage to 800°C, 3 hours for the fifth stage to 1000°C, and 2.5 hours for the sixth stage to 1200°C. Finally, the carbonized material is moved to the graphitization furnace, and 35 g / cm2 is applied to the...
PUM
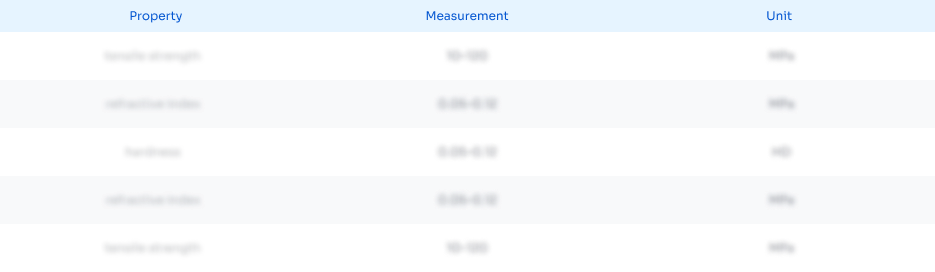
Abstract
Description
Claims
Application Information

- R&D Engineer
- R&D Manager
- IP Professional
- Industry Leading Data Capabilities
- Powerful AI technology
- Patent DNA Extraction
Browse by: Latest US Patents, China's latest patents, Technical Efficacy Thesaurus, Application Domain, Technology Topic, Popular Technical Reports.
© 2024 PatSnap. All rights reserved.Legal|Privacy policy|Modern Slavery Act Transparency Statement|Sitemap|About US| Contact US: help@patsnap.com