Preparation method of hydrotalcite and polyimide composite foam material
A polyimide and composite foam technology, which is applied in the field of preparation of hydrotalcite/polyimide composite foam materials, can solve the slow reaction speed of aromatic diacid diester, reduce the flame retardancy of materials, low reaction degree, etc. problem, to achieve the effect of uniform cells, improved flame retardancy, and simple preparation process
- Summary
- Abstract
- Description
- Claims
- Application Information
AI Technical Summary
Problems solved by technology
Method used
Examples
preparation example Construction
[0033] The preparation method of the hydrotalcite / polyimide composite foam material is characterized in that: the hydrotalcite includes: binary and ternary components composed of magnesium, aluminum, nickel, calcium, copper and rare earth metal elements. Hydrotalcite.
[0034] The aromatic dianhydrides include: pyromellitic dianhydride (PMDA), 3,3′,4,4′-benzophenone tetraacid dianhydride (BTDA), 3,3′,4,4′- Biphenyl tetra-acid dianhydride (BPDA), 3,3′,4,4′-diphenyl ether tetra-acid dianhydride (ODPA), 3,3′,4,4′-biphenyl sulfone tetracarboxylic acid di anhydride (DSDA).
[0035] The polar solvent includes: N-methylpyrrolidone, N,N-dimethylformamide, N,N-dimethylacetamide, and dimethylsulfoxide.
[0036] Described fatty alcohol comprises: methyl alcohol, ethanol.
[0037] The foam stabilizers include: non-hydrolyzable water-soluble polyether siloxane (AK8805, DC193, L580); surfactants include: non-ionic fluorocarbon surfactants ( FS-300, FSO-100), polyethylene oxide nonion...
Embodiment 1
[0042] In a 500ml three-necked flask, add 160 grams of N,N-dimethylformamide and 100 grams of 3,3′,4,4′-benzophenone tetra-acid dianhydride (BTDA) into the magnetic sub, and connect to reflux condensation Put cooling water into the tube, fully stir under the action of an electromagnetic stirrer and slowly raise the temperature to 110°C until the 3,3′,4,4′-benzophenone tetraacid dianhydride (BTDA) is completely dissolved and the solution is in a clear state Stop heating, and when the temperature drops to about 50°C, drop 18 grams of methanol into the turbid liquid with a constant pressure dropping funnel, and the dropping rate is controlled at 1-5 ml per minute, so that 3, 3', 4, 4' - Benzophenone tetra-acid dianhydride (BTDA) begins to undergo esterification reaction. After the esterification reaction is complete and the solution is clear and transparent again, the electromagnetic stirrer stops stirring, and the above solution is left to stand at room temperature to obtain a ne...
Embodiment 2
[0051] Take by weighing 20 grams of the diacid diester solution described in Example 1, add 3 grams of foam stabilizer, 3 grams of polyoxyethylene surfactant, 0.3 gram of fluorocarbon surfactant, 3 grams of composite catalyst, 5 grams of deionized water , After fully stirring, a clear and transparent foam combination solution is formed. Add 15 grams of nickel-aluminum hydrotalcite powder into the clear foam combination solution, and disperse under the action of ultrasonic waves to obtain a white emulsion.
[0052] Stir the white emulsion and 30 grams of polyphenyl polymethylene polyisocyanate with an electric stirring paddle quickly and evenly. When the mixture starts to foam and rises, it is quickly poured into the mold to foam freely. The foam intermediate is at room temperature. After standing still for 5 minutes, transfer to an electric blast drying oven heated to 180° C. for curing for 120 minutes to obtain a polyimide foam.
[0053] The relevant properties and propertie...
PUM
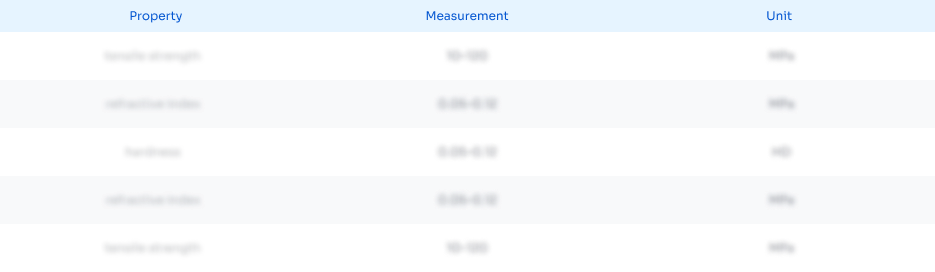
Abstract
Description
Claims
Application Information

- R&D
- Intellectual Property
- Life Sciences
- Materials
- Tech Scout
- Unparalleled Data Quality
- Higher Quality Content
- 60% Fewer Hallucinations
Browse by: Latest US Patents, China's latest patents, Technical Efficacy Thesaurus, Application Domain, Technology Topic, Popular Technical Reports.
© 2025 PatSnap. All rights reserved.Legal|Privacy policy|Modern Slavery Act Transparency Statement|Sitemap|About US| Contact US: help@patsnap.com