Method for preparing ceramic powder used for barium titanate-based low temperature co-fired plate
A technology of barium titanate powder and low-temperature co-firing is applied in the field of preparing ceramic powder for barium titanate-based low-temperature co-firing plate, which can solve the application limitation and reduce the sintering temperature of barium titanate and the sintering temperature of barium titanate powder. High problems, to achieve the effect of reducing sintering temperature, large surface activity, and fine grain
- Summary
- Abstract
- Description
- Claims
- Application Information
AI Technical Summary
Problems solved by technology
Method used
Image
Examples
Embodiment 1
[0016] A method for preparing ceramic powder for barium titanate-based low-temperature co-fired plates:
[0017] Take 63.1g of barium hydroxide octahydrate and dissolve it in 120ml of water at 80°C until saturated. Dissolve 34.1 g of tetrabutyl titanate in 120 ml of ethanol and heat to 80°C. The above two solutions were mixed so that the molar ratio of barium to titanium was 2.0 to form a soymilk-like white solution, which was poured into a high-pressure reactor and reacted at 240° C. for 48 hours to synthesize a barium titanate slurry. The barium titanate slurry was washed 8 times with water, and dried to obtain barium titanate powder. Take 50g barium titanate powder, add sintering accelerator B 2 o 3 -SiO 2 8.82g, of which B 2 o 3 6.17g, SiO 2 2.65g. Put it into a ball mill jar and mill it with water balls for 12 hours to meet the powder: water: ball = 1:2:3 (mass ratio), dry and grind, pass through a 200-mesh standard sieve to obtain barium titanate-based ceramics f...
Embodiment 2
[0019] A method for preparing barium titanate-based low-temperature co-fired plate ceramic powder:
[0020] Take 63.1g of barium hydroxide octahydrate and dissolve it in 120ml of water at 76°C until saturated. Take 37.8g of titanium isopropoxide and dissolve it in 150ml of isopropanol, and heat to 76°C. The above two solutions were mixed so that the molar ratio of barium to titanium was 1.8 to form a soymilk-like white solution, which was poured into a high-pressure reactor and reacted at 180° C. for 72 hours to synthesize a barium titanate slurry. The barium titanate slurry was washed with water for 4 times, and dried to obtain barium titanate powder. Take 50g barium titanate powder, add sintering accelerator B 2 o 3 -Bi 2 o 3 5.56g, of which B 2 o 3 3.34g, Bi 2 o 3 2.22g. Put it into a ball mill jar and mill it with water balls for 9 hours to meet the powder: water: ball = 1:1.5:2 (mass ratio), dry and grind, pass through a 200-mesh standard sieve to obtain barium ...
Embodiment 3
[0022] A method for preparing barium titanate-based low-temperature co-fired plate ceramic powder:
[0023] Take 63.1g of barium hydroxide octahydrate and dissolve it in 120ml of water at 80°C until saturated. Take 37g of tetrabutyl titanate and dissolve it in 120ml of isopropanol, and heat to 80°C. The above two solutions were mixed, and the barium-titanium molar ratio was 1.5 to form a soymilk-like white solution, which was poured into a high-pressure reactor and reacted for 50 hours at 200° C. to synthesize a barium titanate slurry. The barium titanate slurry was washed twice with water, and dried to obtain barium titanate powder. Take 50g barium titanate powder, add sintering accelerator B 2 o 3 -SiO 2 1g, of which B 2 o 3 0.5g, SiO 2 0.5g. Put it into a ball mill jar and mill it with water balls for 8 hours to meet the powder: water: ball = 1:1:1.5 (mass ratio), dry and grind, pass through a 200-mesh standard sieve to obtain barium titanate-based low-temperature c...
PUM
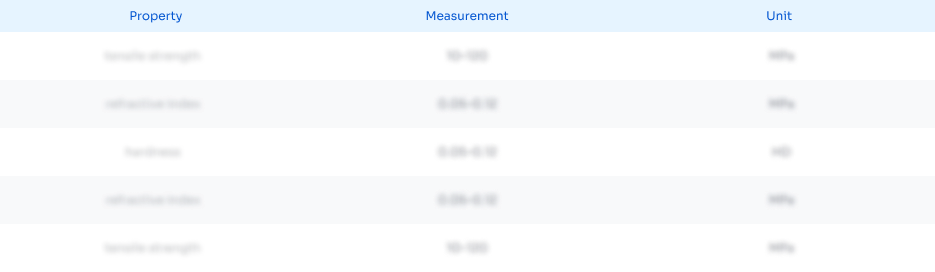
Abstract
Description
Claims
Application Information

- Generate Ideas
- Intellectual Property
- Life Sciences
- Materials
- Tech Scout
- Unparalleled Data Quality
- Higher Quality Content
- 60% Fewer Hallucinations
Browse by: Latest US Patents, China's latest patents, Technical Efficacy Thesaurus, Application Domain, Technology Topic, Popular Technical Reports.
© 2025 PatSnap. All rights reserved.Legal|Privacy policy|Modern Slavery Act Transparency Statement|Sitemap|About US| Contact US: help@patsnap.com