Preparation method for rare earth oxide through jet pyrolysis of rare earth chloride solution
A rare earth oxide and rare earth chloride technology, applied in rare earth metal compounds, chemical instruments and methods, inorganic chemistry, etc., can solve the problems of small particle size of rare earth oxide powder, large particle size of rare earth oxide powder, and long high temperature roasting cycle. , to achieve the effects of reducing pyrolysis energy consumption, uniform particle distribution, and improving pyrolysis conversion rate and
- Summary
- Abstract
- Description
- Claims
- Application Information
AI Technical Summary
Problems solved by technology
Method used
Image
Examples
Embodiment 1
[0054] A by LaCl 3 Preparation of La 2 o 3 method, the steps are as follows:
[0055] 1. CH 4 with O 2 Combustion in a jet burner to form CO 2 and H 2 The high-temperature mixed tail gas of O is directly pumped into the jet pyrolysis reactor as the working fluid and the heat source of the pyrolysis reaction, and the total gas flow rate is 3000Nm 3 / h, gas injection pressure 1.5MPa, CH 4 with O 2 The flow ratio of the two is 1:2, and the combustion reaction formula of the two is:
[0056] CH 4 (g)+2O 2 (g)=CO 2 (g)+2H 2 O(g)+△H 1 ;
[0057] 2. 50g / L LaCl 3 The solution is carried by the transported liquid inlet of the jet pyrolysis reactor into the reactor at a flow rate of 10,000L / h, and is heated and vaporized. The pyrolysis temperature reaches 1250-1300°C, and the pyrolysis reaction occurs rapidly to obtain La 2 o 3 Powder and containing HCl gas, water vapor, CO 2 High temperature pyrolysis tail gas with process oxygen; LaCl 3 The pyrolysis reaction of aqu...
Embodiment 2
[0063] A by CeCl 3 Preparation of CeO 2 method, the steps are as follows:
[0064] 1. Kerosene and O 2 Combustion in a jet burner to form CO 2 and H 2 The high-temperature mixed tail gas of O is directly pumped into the jet pyrolysis reactor as the working fluid and the heat source of the pyrolysis reaction, and the total gas flow rate is 5Nm 3 / h, gas injection pressure 1.5MPa, kerosene and O 2 The flow ratio of the two is 1:16, and the combustion reaction formula of the two is:
[0065] C 8 h 18 (g)+12.5O 2 (g)=8CO 2 (g)+9H 2 O(g)+△H 1 ;
[0066] 2. 175g / L CeCl 3 The solution is carried by the transported liquid inlet of the jet pyrolysis reactor at a flow rate of 10L / h into the reactor to be heated and vaporized. The pyrolysis temperature reaches 500-30°C, and the pyrolysis reaction occurs to obtain CeO 2 Powder and containing HCl gas, water vapor, CO 2 High temperature pyrolysis tail gas with process oxygen; CeCl 3 The pyrolysis reaction of aqueous solution...
Embodiment 3
[0072] A kind of NdCl 3 Preparation of Nd 2 o 3 method, the steps are as follows:
[0073] 1. Natural gas and O 2 The jet burner burns to form high-temperature mixed tail gas, which is directly pumped into the jet pyrolysis reactor as the working fluid and the heat source of the pyrolysis reaction. The total gas flow rate is 500Nm 3 / h, gas injection pressure 0.5MPa, natural gas and O 2 The flow ratio is 1:3.0;
[0074] 2. Prepare NdCl with a concentration of 300g / L 3 Solution 3000L, then add 300L of hydrogen peroxide solution with a mass concentration of 30% to the solution;
[0075] 3. The mixed solution is carried into the reactor by the transported liquid inlet of the jet pyrolysis reactor at a flow rate of 500L / h, heated and vaporized, and the pyrolysis temperature reaches 400-420°C, and the pyrolysis reaction occurs rapidly to obtain Nd 2 o 3 Powder and containing HCl gas, water vapor, CO 2 and high-temperature pyrolysis tail gas with process oxygen; under this ...
PUM
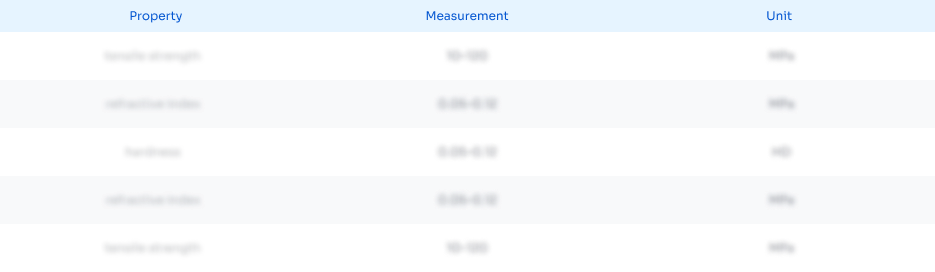
Abstract
Description
Claims
Application Information

- Generate Ideas
- Intellectual Property
- Life Sciences
- Materials
- Tech Scout
- Unparalleled Data Quality
- Higher Quality Content
- 60% Fewer Hallucinations
Browse by: Latest US Patents, China's latest patents, Technical Efficacy Thesaurus, Application Domain, Technology Topic, Popular Technical Reports.
© 2025 PatSnap. All rights reserved.Legal|Privacy policy|Modern Slavery Act Transparency Statement|Sitemap|About US| Contact US: help@patsnap.com