Manufacturing method of composite silver ribbon
A manufacturing method and composite tape technology, applied in the field of silver, can solve the problems of low silver oxide content, incapable of large-scale production, and incapable of continuous processing, and achieve the effects of good composite fastness, low requirements for manufacturing equipment, and easy processing
- Summary
- Abstract
- Description
- Claims
- Application Information
AI Technical Summary
Problems solved by technology
Method used
Examples
Embodiment 1
[0013] Embodiment 1: step A, the surface of copper strip and silver metal oxide strip is cleaned, removes oil stain and impurity on its surface, then offers the groove that matches with silver metal oxide strip on copper strip, the groove that offers on copper strip The width is equal to the width of the silver metal oxide band, and the depth of the groove is 150% of the height of the silver metal oxide band. Finally, the copper strip and the metal oxide strip are polished. Step B, put the copper strip into a continuous furnace for heating, the heating temperature is 550°C, and the tape running speed is 1.5m / min. A protective atmosphere is set in the heating furnace. The protective atmosphere is pure nitrogen or pure hydrogen. The air flow rate is 2m 3 / h. Step C, put the silver metal oxide strip into the groove on the copper strip after heating, then put the mixture of the silver metal oxide strip and the copper strip into the rolling mill for the first rolling, the rolling...
Embodiment 2
[0014] Embodiment 2: step A, the surface of copper strip and silver metal oxide strip is cleaned, removes oil stain and impurity on its surface, then offers the groove that matches with silver metal oxide strip on copper strip, the groove of opening on copper strip The width is equal to the width of the silver metal oxide band, and the depth of the groove is 125% of the height of the silver metal oxide band. Finally, the copper strip and the metal oxide strip are polished. Step B, put the copper strip into a continuous furnace for heating, the heating temperature is 720°C, and the tape running speed is 3.0m / min. A protective atmosphere is set in the heating furnace. The protective atmosphere is pure nitrogen or pure hydrogen. The air flow rate is 12m 3 / h. Step C, put the silver metal oxide strip into the groove on the copper strip after heating, then put the mixture of the silver metal oxide strip and the copper strip into the rolling mill for the first rolling, the rolling...
Embodiment 3
[0015]Embodiment 3: step A, the surface of copper strip and silver metal oxide strip is cleaned, removes oil stain and impurity on its surface, then offers the groove that matches with silver metal oxide strip on copper strip, the groove of opening on copper strip The width is equal to the width of the silver metal oxide band, and the depth of the groove is 125% of the height of the silver metal oxide band. Finally, the copper strip and the metal oxide strip are polished. Step B, put the copper strip into a continuous furnace for heating, the heating temperature is 600°C, and the tape running speed is 2.0m / min. A protective atmosphere is set in the heating furnace. The protective atmosphere is pure nitrogen or pure hydrogen. The air flow rate is 6.5m 3 / h. Step C, put the silver metal oxide strip into the groove on the copper strip after heating, then put the mixture of the silver metal oxide strip and the copper strip into the rolling mill for the first rolling, the rolling...
PUM
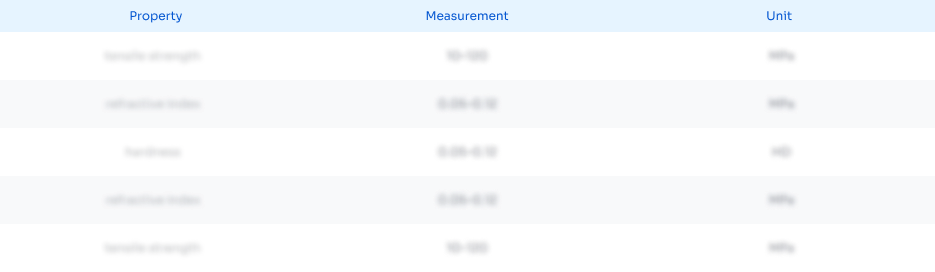
Abstract
Description
Claims
Application Information

- R&D Engineer
- R&D Manager
- IP Professional
- Industry Leading Data Capabilities
- Powerful AI technology
- Patent DNA Extraction
Browse by: Latest US Patents, China's latest patents, Technical Efficacy Thesaurus, Application Domain, Technology Topic, Popular Technical Reports.
© 2024 PatSnap. All rights reserved.Legal|Privacy policy|Modern Slavery Act Transparency Statement|Sitemap|About US| Contact US: help@patsnap.com