Method for preparing acrylic acid from glycerin as raw material
A technology of acrylic acid and glycerin, which is applied in the preparation of carboxylates, chemical instruments and methods, and the preparation of organic compounds, etc., can solve the problems of catalyst deactivation, low yield of acrylic acid, and reduction of catalytic active centers, so as to simplify the process and save cost, and the effect of extending the service life
- Summary
- Abstract
- Description
- Claims
- Application Information
AI Technical Summary
Problems solved by technology
Method used
Image
Examples
Embodiment 1
[0019] Put 38.1 grams of copper nitrate hexahydrate, 1.1 grams of cerium nitrate hexahydrate and 50.5 grams of ferric nitrate nonahydrate into a beaker, add 10 mL of deionized water, place in a water bath at 60°C, heat to dissolve, stir well, and then evaporate to dryness. Drying at 120°C for 12 hours, and calcining at 500°C for 4 hours in an air atmosphere, the prepared oxo-salt catalyst is Cu 1.03 Ce 0.02 Fe 1.00 o z .
[0020] 2mL oxo acid salt catalyst Cu 1.03 Ce 0.02 Fe 1.00 o z Mix it with 4mL of quartz sand and transfer it into a glass reactor with an inner diameter of 15mm, and use quartz fibers to fix the catalyst up and down. Nitrogen is introduced, and the reaction is heated to 310°C for activation for 1 hour, and then the mixed gas with a molar ratio of glycerin: water: nitrogen: oxygen = 10:12:8.25:0.125 is preheated at 290°C and then passed into the reactor. Airspeed is 100h -1 , the reaction temperature is 310°C. The reacted product was collected with ...
Embodiment 2
[0022] Put 10.0 g of titanium dioxide sol, 38.6 g of cobalt nitrate hexahydrate, and 1.5 g of zinc nitrate hexahydrate into a beaker, add 10 mL of deionized water, place in a 60°C water bath, heat and stir thoroughly, and then evaporate to dryness. Drying at 120°C for 12 hours, and calcining at 650°C for 4 hours in an air atmosphere, the prepared oxo-salt catalyst is Co 1.06 Zn 0.04 Ti 1.00 o z . The catalytic reaction conditions are the same as in Example 1. The reaction results are shown in Table 1.
Embodiment 3
[0024] Put 154.5 grams of ammonium heptamolybdate, 1.5 grams of nickel nitrate hexahydrate, and 43.4 grams of ferric nitrate nonahydrate into a beaker, add 10 mL of deionized water, place in a water bath at 60°C, heat and stir thoroughly, and then evaporate to dryness. Dry at 120°C for 12 hours, and bake at 550°C for 4 hours in the air atmosphere, the prepared oxo acid salt catalyst is Fe0.86 Ni 0.04 Mo 1.00 o z . The catalytic reaction conditions are the same as in Example 1. The reaction results are shown in Table 1.
PUM
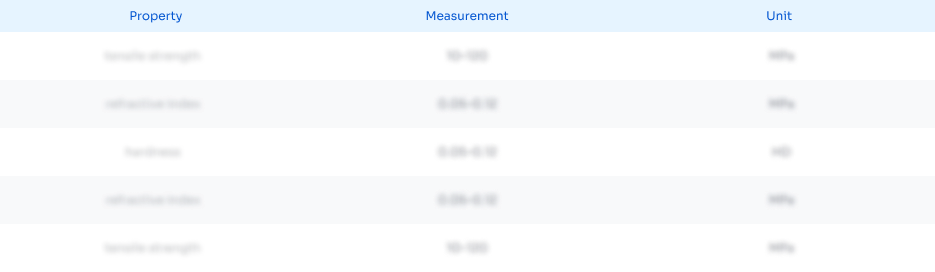
Abstract
Description
Claims
Application Information

- Generate Ideas
- Intellectual Property
- Life Sciences
- Materials
- Tech Scout
- Unparalleled Data Quality
- Higher Quality Content
- 60% Fewer Hallucinations
Browse by: Latest US Patents, China's latest patents, Technical Efficacy Thesaurus, Application Domain, Technology Topic, Popular Technical Reports.
© 2025 PatSnap. All rights reserved.Legal|Privacy policy|Modern Slavery Act Transparency Statement|Sitemap|About US| Contact US: help@patsnap.com