Method for recovering zinc, indium, iron, and lead from high-iron zinc oxide mixture smelted with zinc
A high-iron zinc oxide and mixture technology, which is applied in the field of lead, indium, iron, and zinc recovery, can solve the problems of poor recovery of indium, large environmental impact of ammonia gas, waste of resources, etc., and achieve good economic and social benefits. The effect of comprehensive recycling of resources and reasonable technology
- Summary
- Abstract
- Description
- Claims
- Application Information
AI Technical Summary
Problems solved by technology
Method used
Image
Examples
Embodiment 1
[0034] (1) Neutral leaching of high-iron zinc oxide mixture
[0035] 1. Raw material: high iron zinc oxide mixture, waste electrolyte.
[0036] 2. Process purpose: add the waste electrolyte containing sulfuric acid and high-iron zinc oxide mixture raw materials into the immersion reaction tank, and react after the temperature rises to a certain condition, dissolve the zinc in the high-iron zinc oxide mixture raw materials, and ensure that the zinc oxide and other Impurities are well separated and a high concentration zinc sulfate solution is obtained.
[0037] 3. Process conditions: (1) The initial H?SO? concentration of the leaching solution is 160g / l (2) The temperature is 65°C (3) The reaction time is 2h (4) The final acidity PH=4.5.
[0038] 4. Operation method: first use the delivery pump to pump the waste electrolyte containing sulfuric acid into the reaction tank, then turn on the agitator until the volume of the solution reaches 70m 3 Stop feeding the liquid, start t...
Embodiment 2
[0074] (1) Neutral leaching of high-iron zinc oxide mixture
[0075] 1. Raw material: high iron zinc oxide mixture, waste electrolyte.
[0076] 2. Process purpose: add the waste electrolyte containing sulfuric acid and high-iron zinc oxide mixture raw materials into the immersion reaction tank, and react after the temperature rises to a certain condition, dissolve the zinc in the high-iron zinc oxide mixture raw materials, and ensure that the zinc oxide and other Impurities are well separated and a high concentration zinc sulfate solution is obtained.
[0077] 3. Process conditions: (1) The initial H2SO4 concentration of the leaching solution is 175g / l (2) The temperature is 70-75°C (3) The reaction time is 2-3h (4) The final acidity is PH5.0.
[0078] 4. Operation method: first use the delivery pump to pump the waste electrolyte into the reaction tank, then turn on the agitator until the volume of the solution reaches 70m 3 Stop feeding the liquid, start to heat up the solu...
PUM
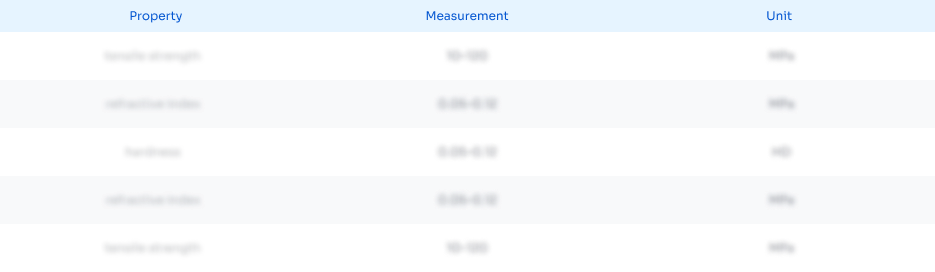
Abstract
Description
Claims
Application Information

- R&D
- Intellectual Property
- Life Sciences
- Materials
- Tech Scout
- Unparalleled Data Quality
- Higher Quality Content
- 60% Fewer Hallucinations
Browse by: Latest US Patents, China's latest patents, Technical Efficacy Thesaurus, Application Domain, Technology Topic, Popular Technical Reports.
© 2025 PatSnap. All rights reserved.Legal|Privacy policy|Modern Slavery Act Transparency Statement|Sitemap|About US| Contact US: help@patsnap.com