Method for preparing metal elementary substance
A metal elemental and metal technology, applied in the field of metallurgy, can solve problems such as difficult reduction of FeO in slag layer, wear of refractory lining, waste of iron resources, etc., and achieve the effect of improving metal reduction rate, reducing content, and improving reuse
- Summary
- Abstract
- Description
- Claims
- Application Information
AI Technical Summary
Problems solved by technology
Method used
Image
Examples
preparation example Construction
[0031] The method for preparing a simple substance according to an embodiment of the present invention has the following advantages:
[0032] 1. Coal powder is blown into the bottom, preheated by the liquid metal layer, and then passed through the slag layer to reduce the metal oxides in it, which can greatly reduce the content of metal oxides in the slag, improve the metal reduction rate, and reduce the waste of resources;
[0033] 2. Reduce the coal powder on the upper surface of the slag layer, reduce the loss of refractory materials, prolong the service life of refractory materials in the furnace, and improve the operating rate;
[0034] 3. The flexibility of fuel and reducing agent, the gas can include coke oven gas, natural gas, etc., and the pulverized coal can include lignite, bituminous coal, anthracite and other coal types;
[0035] 4. The high-temperature flue gas is used to preheat the gas after dedusting. The gas temperature increases, the liquid metal layer and t...
Embodiment 1
[0043] Preparation of metallic iron: During the preparation process, the reduction furnace contains molten iron and slag, which are divided into two layers in the furnace, the upper layer is the slag layer, and the lower layer is the molten iron. Continuously or intermittently add refractory iron ore into the furnace. Oxygen-enriched is sprayed into the furnace from a lance in the center of the furnace top, and the lance head is immersed in the slag layer of the molten pool. Iron minerals are melted into a liquid state under the action of high temperature, and iron oxide and coal powder sprayed into the bottom of the furnace undergo a reduction reaction to form molten iron. Under the action of the oxygen-enriched high-speed airflow from the spray gun, the molten pool is in a state of violent agitation. The high-temperature flue gas is heat-exchanged by the waste heat boiler to generate steam for power generation, dust is removed, the gas is preheated by the heat exchanger, an...
PUM
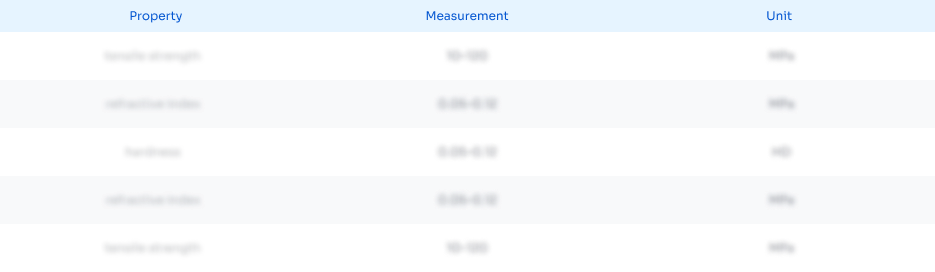
Abstract
Description
Claims
Application Information

- R&D Engineer
- R&D Manager
- IP Professional
- Industry Leading Data Capabilities
- Powerful AI technology
- Patent DNA Extraction
Browse by: Latest US Patents, China's latest patents, Technical Efficacy Thesaurus, Application Domain, Technology Topic, Popular Technical Reports.
© 2024 PatSnap. All rights reserved.Legal|Privacy policy|Modern Slavery Act Transparency Statement|Sitemap|About US| Contact US: help@patsnap.com