Method for recovering carbon fiber by cracking waste carbon fiber composite material
A technology for recycling carbon fiber and composite materials, which is applied in the field of cracking and recycling carbon fiber from waste carbon fiber composite materials. It can solve the problems that affect the cutting and/or crushing processing and reuse performance of recycled carbon fiber, serious oxidation reaction of carbon fiber, and easy carbon formation on the surface of carbon fiber. Achieve the effects of improved convenience, low processing cost, and simple equipment
- Summary
- Abstract
- Description
- Claims
- Application Information
AI Technical Summary
Problems solved by technology
Method used
Examples
Embodiment 1
[0024] The resin matrix of the selected discarded carbon fiber composite material plate is epoxy resin composite, and the weight content of carbon fiber is 63%. The carbon fiber composite material plate is broken into fragments, and the mass is weighed to be 10.0kg (the content of carbon fiber in the calculation=10.0×0.63=6.300kg) is put into the cracking furnace, and nitrogen gas is introduced into the furnace door for 5-10 minutes after closing the furnace door. The air in the furnace is completely exhausted to form an oxygen-free inert environment. Raise the temperature of the cracking furnace to 350°C, so that the resin in the carbon fiber reinforced resin composite material undergoes thermal cracking reaction for 2.0 hours at this temperature, and the cracked products are discharged out of the furnace with the airflow. Stop heating, and take out the cracking residual product after the temperature of the cracking furnace drops to normal temperature, the product is a small ...
Embodiment 2
[0028] Cracking furnace temperature is set to 600 ℃, all the other operations are identical with embodiment 1. The product is a mass of aggregated carbon fibers with a small amount of carbon on the surface. The product weighs 6.634kg. The calculated carbon content on the surface of the carbon fiber is:
[0029] (6.634-6.300) / 6.300=5.3wt%
[0030] The obtained carbon fibers were cut and pulverized, and the results showed that the carbon fibers had good processability in the subsequent cutting and / or pulverizing sections, and the obtained chopped fibers and powder fibers had good dimensional uniformity.
Embodiment 3
[0032] The temperature of the cracking furnace is set to 900°C and the thermal decomposition time is 0.5hr, and all the other operations are the same as in Example 1. The product is a mass of aggregated carbon fibers with a small amount of carbon on the surface. The product weighs 6.337kg, and the calculated carbon content on the surface of the carbon fiber is:
[0033] (6.337-6.300) / 6.300=0.58wt%
[0034] The obtained carbon fibers were cut and pulverized, and the results showed that the carbon fibers had better processability in the subsequent cutting and / or pulverizing sections, and the dimensional uniformity of the obtained chopped fibers and powder fibers was better.
PUM
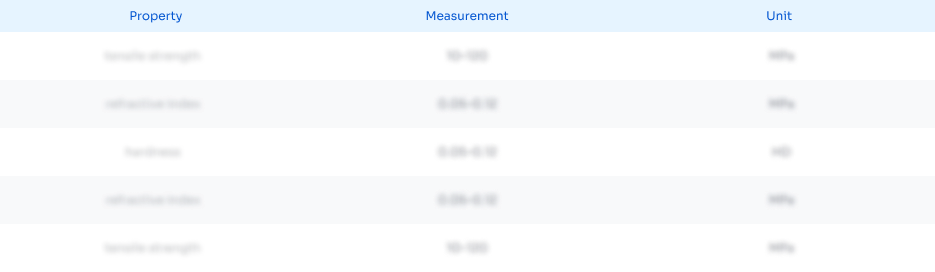
Abstract
Description
Claims
Application Information

- R&D
- Intellectual Property
- Life Sciences
- Materials
- Tech Scout
- Unparalleled Data Quality
- Higher Quality Content
- 60% Fewer Hallucinations
Browse by: Latest US Patents, China's latest patents, Technical Efficacy Thesaurus, Application Domain, Technology Topic, Popular Technical Reports.
© 2025 PatSnap. All rights reserved.Legal|Privacy policy|Modern Slavery Act Transparency Statement|Sitemap|About US| Contact US: help@patsnap.com