Comprehensive recycling technology for iron removal slag and blast furnace soot produced in zinc smelting process adopting high acid leaching wet method
A technology for blast furnace soot and hydrometallurgy zinc smelting, which is applied in the fields of process efficiency improvement, chemical instruments and methods, solid separation, etc., can solve the problems of loss of valuable metal resources, hidden dangers of environmental impact, and increased storage costs, and achieves pollution reduction. hidden dangers, comprehensive utilization, and the effect of saving carbon distribution
- Summary
- Abstract
- Description
- Claims
- Application Information
AI Technical Summary
Problems solved by technology
Method used
Image
Examples
Embodiment 1
[0028] Embodiment 1: see figure 1 , a high-acid leaching process for the comprehensive recycling of iron slag and blast furnace soot from wet zinc smelting, which includes the following steps:
[0029] (1) Preparation of raw materials: prepare mixed raw materials in proportions by weight of 20 parts of iron slag, 8 parts of sulfur concentrate, and 40 parts of blast furnace soot;
[0030] (2) Magnetization roasting: Send the mixed raw materials into the hopper of the magnetized roasting fluidized furnace through the conveyor belt and roast to obtain slag; control the feeding speed to add the mixed raw materials into the magnetized roasted fluidized furnace at a uniform speed, and the roasting temperature is about 800-900 ° C. The wind linear velocity is 0.3-0.6m / s, the air excess coefficient is -2-5%, and the sulfur dioxide concentration in the roasting flue gas is 8-10%. The roasting flue gas is sent to the acid system for acid production after the waste heat recovery of the w...
Embodiment 2
[0032] Example 2: see figure 1 , a high-acid leaching process for the comprehensive recycling of iron slag and blast furnace soot from wet zinc smelting, which includes the following steps:
[0033] (1) Preparation of raw materials: prepare mixed raw materials in proportions by weight of 23 parts of goethite slag, 11 parts of sulfur concentrate, 23 parts of blast furnace soot, 1 part of coke, and 1.5 parts of coal;
[0034] (2) Magnetization roasting: Send the mixed raw materials into the hopper of the magnetized roasting fluidized furnace through the conveyor belt and roast to obtain slag; control the feeding speed to add the mixed raw materials into the magnetized roasted fluidized furnace at a uniform speed, and the roasting temperature is about 800-900 ° C. The wind linear velocity is 0.3-0.6m / s, the air excess coefficient is -2-5%, and the sulfur dioxide concentration in the roasting flue gas is 8-10%. The roasting flue gas is sent to the acid system for acid production a...
Embodiment 3
[0036] Embodiment 3: see figure 2 , a high-acid leaching process for the comprehensive recycling of iron slag and blast furnace soot from wet zinc smelting, which includes the following steps:
[0037] (1) Preparation of raw materials: prepare mixed raw materials in proportions by weight of 26 parts of hematite slag, 10 parts of sulfur concentrate, and 33 parts of blast furnace soot;
[0038] (2) Magnetization roasting: Send the mixed raw materials into the hopper of the magnetized roasting fluidized furnace through the conveyor belt and roast to obtain slag; control the feeding speed to add the mixed raw materials into the magnetized roasted fluidized furnace at a uniform speed, and the roasting temperature is about 800-900 ° C. The wind linear velocity is 0.3-0.6m / s, the air excess coefficient is -2-5%, and the sulfur dioxide concentration in the roasting flue gas is 8-10%. The roasting flue gas is sent to the acid system for acid production after the waste heat recovery of...
PUM
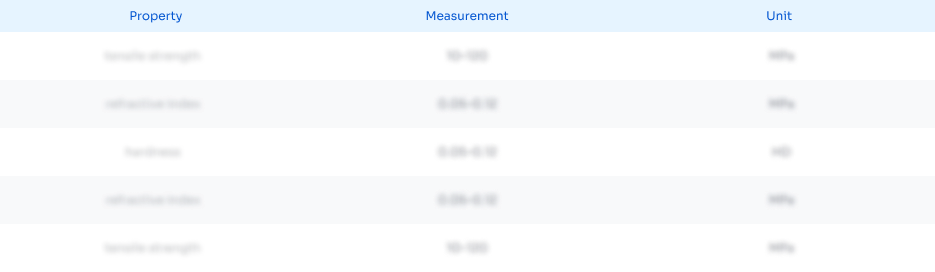
Abstract
Description
Claims
Application Information

- R&D
- Intellectual Property
- Life Sciences
- Materials
- Tech Scout
- Unparalleled Data Quality
- Higher Quality Content
- 60% Fewer Hallucinations
Browse by: Latest US Patents, China's latest patents, Technical Efficacy Thesaurus, Application Domain, Technology Topic, Popular Technical Reports.
© 2025 PatSnap. All rights reserved.Legal|Privacy policy|Modern Slavery Act Transparency Statement|Sitemap|About US| Contact US: help@patsnap.com