Method for recycling gold and copper from copper-containing oxidization gold ores
A technology for copper oxidation and gold recovery, which is applied in the improvement of process efficiency, photographic technology, instruments, etc., can solve the problems of affecting the effect of activated carbon adsorption of gold, occupying the active points of activated carbon adsorption, and the effect of copper removal is not very ideal, and achieves leaching. The time is shortened, the leaching effect is obvious, and the effect of reducing infrastructure investment
- Summary
- Abstract
- Description
- Claims
- Application Information
AI Technical Summary
Problems solved by technology
Method used
Image
Examples
Embodiment 1
[0021] The raw ore of a copper oxide gold ore has a gold content of 5.7g / t and a copper content of 0.6%. (1) The raw ore is firstly crushed, and the raw ore is crushed 4 ) 2 SO 4 , 5.4 grams of CaO, 0.6 grams of NaCN; (3) Use a mechanical stirring device to adjust the slurry after adding the leaching agent, so that the slurry is in a suspended state in the electrolytic cell, and the electrodeposition condition is to use a titanium plate coated with ruthenium iridium as the anode , the cathode adopts graphite cathode, the pole spacing is 5mm, and the current density is 150A / m 2 , the temperature of the electrowinning solution is normal temperature; (4) Connect direct current, after 12 hours of electrowinning of the ore pulp, filter and dry the leached slag, analyze the slag gold content and calculate the slag gold leaching rate, and analyze and test the slag-calculated gold leaching rate Reach 90%. (5) The supplementary part of the leaching reagent and water after electrowin...
Embodiment 2
[0024] Except that steps (1), (3), (4), and (5) are identical to Example 1, its embodiment data are as follows:
[0025] Take 300 grams of finely ground ore samples, add 750 mL of water to make a slurry, add 5.4 grams of NH to the slurry 4 HCO 3 , 5.4 g Ca(OH) 2 , 0.3 gram of NaCN; the leached slag was filtered and dried, the slag gold content was analyzed and the slag gold leaching rate was calculated, and the slag gold leaching rate reached 90%. After the filtrate after electrowinning is supplemented with some chemicals to the initial concentration, it is mixed with raw ore samples to continue electrowinning. The electrowinning conditions are the same as the first electrowinning, and the slag gold leaching rate is 90%.
Embodiment 3
[0027] Except that step (1) is identical with example 1, its embodiment data are as follows:
[0028] Take 300 grams of finely ground ore samples, add 750 mL of water to make a slurry, add 5.4 grams (NH 4 ) 2 SO 4 , 5.4 grams of CaO, 0.6 grams of NaCN; the pulp after adding the leaching agent is adjusted by a mechanical stirring device, so that the pulp is in a suspended state in the electrolytic cell. Cathode, the pole spacing is 20mm, the current density is 50A / m 2 , The temperature of the electrolysis solution is normal temperature; after 24 hours of electrolysis of the ore pulp, the leaching residue is filtered and dried, and the gold content is analyzed; the gold leaching rate reaches 91%.
[0029] Conventional method leaching comparison experiment: take 300 grams of finely ground ore samples, add 750 mL of water to make a slurry, add 5.4 grams (NH 4 ) 2 SO 4 , 5.4 grams of CaO, 0.6 grams of NaCN, stirring and leaching in a glass container for 48 hours, after leachi...
PUM
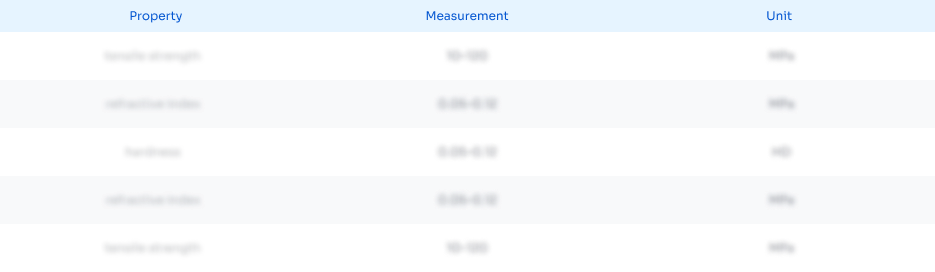
Abstract
Description
Claims
Application Information

- R&D Engineer
- R&D Manager
- IP Professional
- Industry Leading Data Capabilities
- Powerful AI technology
- Patent DNA Extraction
Browse by: Latest US Patents, China's latest patents, Technical Efficacy Thesaurus, Application Domain, Technology Topic, Popular Technical Reports.
© 2024 PatSnap. All rights reserved.Legal|Privacy policy|Modern Slavery Act Transparency Statement|Sitemap|About US| Contact US: help@patsnap.com