Method for preparing thin layer graphene on surface of metal catalyst
A technology of metal catalyst and thin-layer graphene, which is applied in the direction of metal material coating process, coating, gaseous chemical plating, etc., can solve the problems of controllability and uniformity of high-quality graphene film layers, etc. Achieve the effect of reducing carbon content, simple process and promoting segregation
- Summary
- Abstract
- Description
- Claims
- Application Information
AI Technical Summary
Problems solved by technology
Method used
Image
Examples
Embodiment 1
[0054] Example 1 The method for preparing thin-layer graphene comprises the steps:
[0055] (1) Thin film deposition of any of the catalysts Ni, Fe, Co and CuNi alloys: using magnetron sputtering on SiO 2 / Si wafer is coated with a catalyst film with a thickness of 270 nm;
[0056] (2) Carburizing: During the carburizing process, the conventional CVD method is used to introduce CH 4 (20 sccm) + H 2 (100 sccm) + Ar(100 sccm) mixed gas;
[0057] (3) Hydrogen etching: the sample was slowly heated to 970 °C for hydrogen etching (flow rate of 550 sccm). During the single hydrogen etching process, the original disordered graphene film or the first Removal of graphene formed at metal catalyst grain boundaries during one-step CVD process;
[0058] (4) Graphene segregation growth: After hydrogen etching, argon gas (600 sccm) was passed through the quartz tube for 2 minutes to exhaust the hydrogen, and then the sample was rapidly cooled to room temperature, and segregated graphene...
Embodiment 2
[0059] Example 2 The method for preparing thin-layer graphene comprises the steps:
[0060] (1) Deposition of any one or several alloy films of catalysts Ni, Fe, Co, Cu, Pt, Ru: use electron beam evaporation to coat a catalyst film with a thickness of 300 nm on the MgO substrate;
[0061] (2) Gas carburization: C is introduced into PECVD during carburization 2 h 2 (20 sccm) + H 2 (30 sccm) + Ar(30 sccm) mixed gas;
[0062] (3) Plasma etching: the sample was slowly heated (up to 1080 °C) for hydrogen plasma etching (flow rate of 500 sccm). Removal of nascent disordered carbon layers on the surface of the metal catalyst or graphene formed at the grain boundaries of the metal catalyst during the first PECVD process in a separate plasma etching process;
[0063] (4) Graphene segregation growth: After hydrogen etching, argon gas (400 sccm) was passed through the quartz tube for 2 minutes to exhaust the hydrogen, and then the sample was rapidly cooled to room temperature, and...
Embodiment 3
[0064] Example 3 The method for preparing thin-layer graphene comprises the steps:
[0065] (1) Catalyst Pt, Ru, Co and CuNi alloy film deposition: using thermal evaporation on SiO 2 The substrate is coated with a catalyst film with a thickness of 650 nm;
[0066] (2) Solid carburizing: PMMA, PVP, PVA, PE, sugar, activated carbon, amorphous carbon, acetylene black, carbon black. Moreover, the solid carbon source can be evenly distributed on the surface of the catalyst in the form of solution and powder, with a thickness of 1 mm;
[0067] (3) Etching: The sample was slowly heated to 1080 °C for hydrogen etching (flow rate of 500 sccm). Removal of the original disordered graphene film on the surface of the metal catalyst or the graphene formed at the grain boundary of the metal catalyst during the first step of CVD in a separate hydrogen etching process;
[0068] (4) Graphene segregation growth: After hydrogen etching, argon gas (600 sccm) was passed through the quartz tube...
PUM
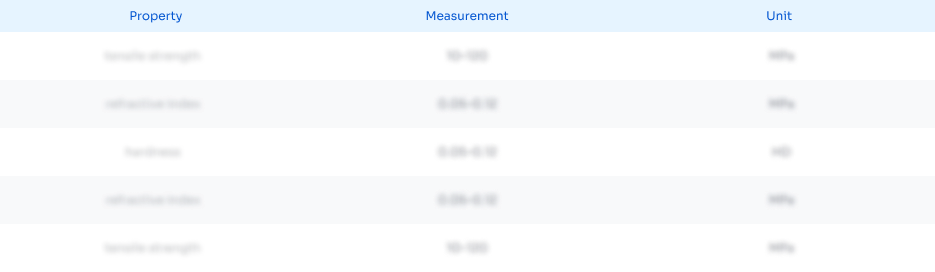
Abstract
Description
Claims
Application Information

- R&D
- Intellectual Property
- Life Sciences
- Materials
- Tech Scout
- Unparalleled Data Quality
- Higher Quality Content
- 60% Fewer Hallucinations
Browse by: Latest US Patents, China's latest patents, Technical Efficacy Thesaurus, Application Domain, Technology Topic, Popular Technical Reports.
© 2025 PatSnap. All rights reserved.Legal|Privacy policy|Modern Slavery Act Transparency Statement|Sitemap|About US| Contact US: help@patsnap.com